Microstructure and Weight Loss Corrosion Studies of Za-27 Metal Matrix Composites Containing Red Mud Particulates
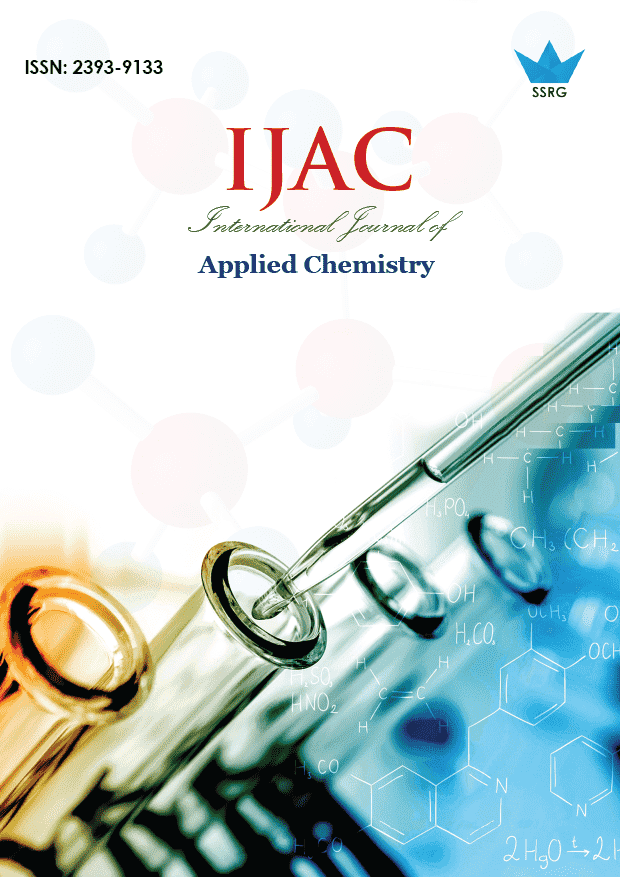
International Journal of Applied Chemistry |
© 2017 by SSRG - IJAC Journal |
Volume 4 Issue 2 |
Year of Publication : 2017 |
Authors : Jayaprakash, H.V., P.V.Krupakara |
How to Cite?
Jayaprakash, H.V., P.V.Krupakara, "Microstructure and Weight Loss Corrosion Studies of Za-27 Metal Matrix Composites Containing Red Mud Particulates," SSRG International Journal of Applied Chemistry, vol. 4, no. 2, pp. 13-16, 2017. Crossref, https://doi.org/10.14445/23939133/IJAC-V4I4P104
Abstract:
This paper deals with the high corrosion resistance developed by the metal matrix composites when compared with that of matrix alloy. Matrix selected is ZA-27 and reinforcement selected is red mud particulates, which is a ceramic material. It is obtained after the removal of aluminium from its ore, procured from Hindalco, Renikoot district, UP. The composites are prepared using liquid melt metallurgy technique using vortex method. Preheated but uncoated red mud particulates are added to the melt. Metal matrix composites containing 2, 4 and 6 weight percentage of red mud are prepared. Matrix was also casted in the same way for comparison. Bar castings are cut into cylindrical discs of 20mm diameter and 20mm thickness. Microstructures of the specimens are taken and studied for uniform distribution of particulates. Corrosion tests were conducted at room temperature (230 C) using conventional weight loss method according to ASTM G69-80. The corrodents used for the tests were 0.025, 0.05 and 0.1 normal solutions of hydrochloric acid, 0.25 M equimolar solutions of sodium chloride and sodium hydroxide. Corrosion rates were calculated using the formula 534DAT/W. In each case the corrosion rate in all corrodents decreases with increase in exposure time for matrix and metal matrix composites. As red mud content increases the composites become corrosion resistant due to insulating nature of ceramic material and less exposure of matrix alloy in those metal matrix composites. Corrosion rate in all concentrations of hydrochloric acid were high when compared to the corrosion rate in equimolar solutions of sodium chloride and sodium hydroxide. Hence the composites are more suitable for the use in saltish or marine environment
Keywords:
Hence the composites are more suitable for the use in saltish or marine environment.
References:
1. B.M.Girish "Fractography , Fluidity and tensile properties of aluminium/Haematite particle composite", Journal of Mateials Engineering and performance, vol. 8(3), (1999), pp309-314
2. B.M.Satish. "Effect of short glass fibers on the mechanical properties of cast ZA-27 alloy composites", Material and Design, vol. 17(5/6) (1996), pp245-250.
3. P.Reynaud "Cyclic fatigue ceramic-matrix composites at ambient and elevated temperatures". Composite Science and Technology, vol.56, (1996), pp809-814
4. S.C.Tjong & Z.Y.Ma, "The high temperature creep behaviour of aluminium matrix composite reinforced with SiC, Al2O3 and TiB2 particulates", Composite Science and Technology, vol.57, (1997) pp697-702.
5. H.Akubulut, M.Durman and F.Yilnaaz, "Higher temperature Young's Modulus of aluminium shore fire reinforced Al-Si MMCs produced by liquid infilteration", Materials Science and Technology, vol..14, pp299-305
6. M.K.Aghajanian, G.C.Atland, P.baron-Antolin, A.S.Nagelberg, "fabrication and properties of metal matrix composites for automotive brake calipers applications", Metal Matrix composites, Library of congress catalog card number 93-87522, Society of Automotive Engines, Inc, (1994), pp77-81.
7. M.A.Dellis, J.P.Keusternas, F.Delannay and J.Wergia, mater.Sci.Engg 135-253, (1991)
8. S.H.J.Lo, S. Dionne, M.Sahoo and H.M.Hatrone, J.of mater.Sci.27, 5681-5691 (1992)
9. W.Smith, Structures and Properties of Enginering alloys. 2ndedition McGraw-Hill, NewYork, (1993), p-567
10. R.J.Barnhurst and K.C.Farge in Proceedings of international symposium on Zinc-Aluminium, ZA Casting Alloys ed. G.P.Lewis, R.J.Barnhurst and C.A.Loong, CIM, Toronto, (1986), p85.
11. S.H.J.Lo, S. Dionne, M.Sahoo and H.M.Hatrone, J.of mater.Sci.27, 5681-5691 (1992)
12. W.Smith, Structures and Properties of Enginering alloys. 2ndedition McGraw-Hill, NewYork, (1993), p-567 13. N.Karni, G.B.Backay and M.Bamberger, J.Mat. Sci. Lett. 13, 541-544(1994)
14. K.H.W.Seah "Effect of artificial ageing on Tensile strength of ZA-27 short glass fiber reinforced composite", Journal of the institution of engineers, Singpore, vol. 38, no4, (1998).
15. B.M.Satish "Corrosion characteristics of ZA-27 / glass-fiber composites", Corrosion science, vol. 39(12), (1997), pp2143- 2150
16. Wu.Jianxin, Liu Wei LiPeng Xing & Wurenjie, "Effect of matrix alloying elements on the corrosion resistance of C /Al composites materials, Jr. of Mat.Sci. lett. Vol. 12, (1993). pp 1500-1501.
17. P.P.Trzaskoma, “Pit morphology of aluminium alloy and silicon carbide/aluminium alloy" Corrosion 46(5) (1990) 402-409
18. J.F.Mclyntyre, R.K.Conrad & S.L.GoHedge, "Technical note: The effect of heat treatment on the pitting behaviour of SiC / AA2124", Corrosion, vol.46(1990)902