Measurable Characterization of the Slight Force Transducer used in Nano indentation Tools
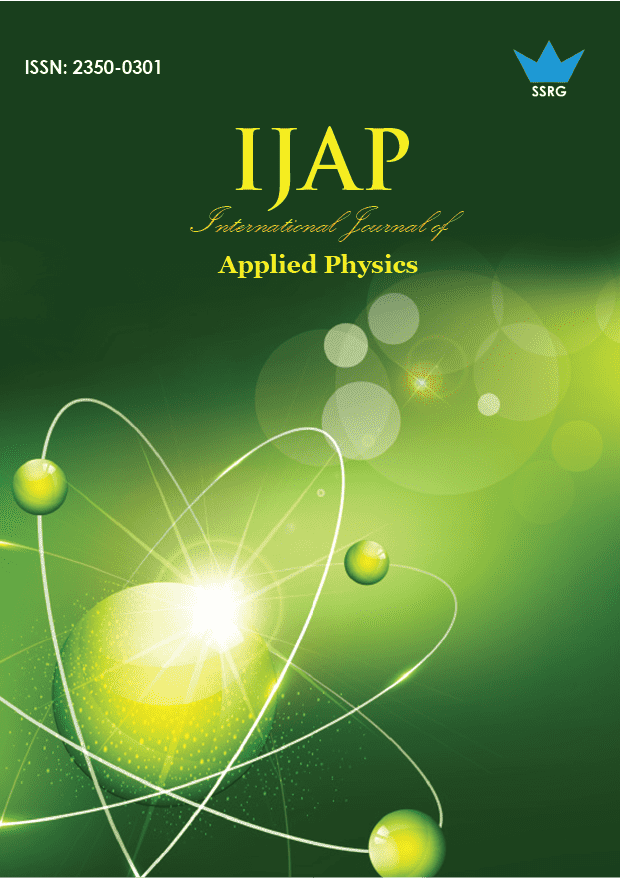
International Journal of Applied Physics |
© 2016 by SSRG - IJAP Journal |
Volume 3 Issue 3 |
Year of Publication : 2016 |
Authors : Benjamin, Alina |
How to Cite?
Benjamin, Alina, "Measurable Characterization of the Slight Force Transducer used in Nano indentation Tools," SSRG International Journal of Applied Physics, vol. 3, no. 3, pp. 19-23, 2016. Crossref, https://doi.org/10.14445/23500301/IJAP-V3I6P103
Abstract:
Quantitative description of the mechanical possessions of resources in micro nano scale using depth-sensing depression method demands high performance of nanoindentation instruments in use. In this paper, the efforts to standardize the capacitive control transducer of a profitable tool are obtainable, where the quasi-static characteristic of the force transducer has sustained calibrated by a whole compensation balance with a resolution of 1 nN. To examine the dynamic response of the transducer, an electrostatic MEMS (Micro-Electro-Mechanical System) based on nano-force transfer standard with nano-Newton resolution and a bandwidth up to 6 kHz have remained employed. Primary novel results designate that the power transducer below correction needs a detailed force indecision less than 300 nN in the calibration range of 1 mN; the transient period at contact opinions totals to 10 seconds; 3 the overshoot of engagement is pre-load dependent.
Keywords:
Nanometrology; Nanoindentation Instrument; Nano-Force Transducer; Microelectromechanical Systems; Nano-Force Calibration.
References:
[1] C. M. F. Doerner and W. D. Nix, “A Method for Interpreting the Data from Depth Sensing Indentation Instruments,” Journal of Materials Research, Vol. 1, No. 4, 1986, pp. 601-609.
[2] W. C. Oliver and G. M. Pharr, “An Improved Technique for Determining Hardness and Elastic Modulus Using Load and Displacement Sensing Indentation Experiment,” Journal of Materials Research, Vol. 7, No. 6, 1992, pp. 1564-1583.
[3] G. M. Pharr and A Bolshakov, “Understanding nanoindentation Unloading Curves,” Journal of Materials Research, Vol. 17, No. 10, 2002, pp. 2660-2671.
[4] ISO 14577-1, “Metallic Materials—Instrumented Indentation Test for Hardness and Materials Parameters—Part 1: Test Method,” International Organization for Standardization, Geneva, 2002.
[5] ISO 14577-2, “Metallic Materials—Instrumented Indentation Test for Hardness and Materials Parameters—Part 2: Verification and Calibration of Testing Machines,” International Organization for Standardization, Geneva, 2002.
[6] K. Herrman, N. M. Jennett, W. Wegener, J. Meneve and R. Seeman, “Progress in Determining the Area Function of Indenters Used for Nanoindentation,” Thin Solid Films, Vol. 377-378, 2000, pp. 394-400.
[7] Z. Li, K. Herrmann and F. Pohlenz, “A Comparative Approach for Calibration of the Depth Measuring System in a Nanoindentation Instrument,” Measurement, Vol. 39, No. 6, 2006, pp. 547-552.
[8] A. Yacoot and M. J. Downs, “The Use of x-Ray Interferometry to Investigate the Linearity of the NPL Differential Plane Mirror Optical Interferometer,” Measurement Science and Technology, Vol. 11, No. 8, 2000, pp. 1126- 1130.
[9] J. R. Pratt, J. A. Kramar, D. B. Newell and D. T. Smith, “Review of SI Traceable Force Metrology for Instrumented Indentation and Atomic Force Microscopy,” Measurement Science and Technology, Vol. 16, No. 11, 2005, pp. 2129-2137.
[10] Y. Huan, D. X. Liu, R. Yang and T. H. Zhang, “Analysis of the Practical Force Accuracy of Electromagnet-Based Nanoindenters,” Measurement, Vol. 43, No. 9, 2010, pp.1090-1093.