Optimized Steel Quenching Processes and Their New Modifications
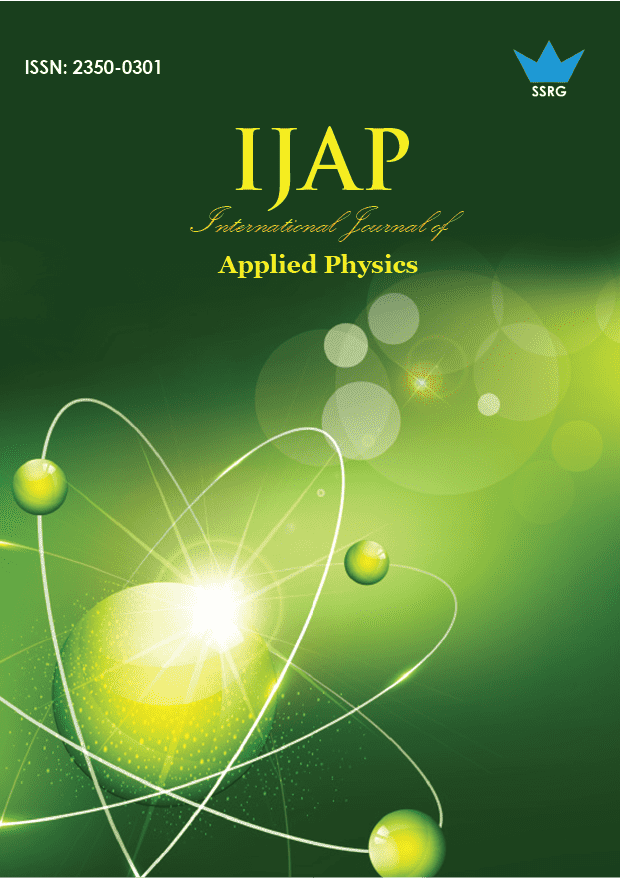
International Journal of Applied Physics |
© 2019 by SSRG - IJAP Journal |
Volume 6 Issue 2 |
Year of Publication : 2019 |
Authors : Nikolai Kobasko |
How to Cite?
Nikolai Kobasko, "Optimized Steel Quenching Processes and Their New Modifications," SSRG International Journal of Applied Physics, vol. 6, no. 2, pp. 79-86, 2019. Crossref, https://doi.org/10.14445/23500301/IJAP-V6I2P112
Abstract:
The paper discusses quenching steel parts in water flow when transient nucleate boiling process is completely absent. This process was called intensive
quenching (IQ-3) technology or direct convection which was patented in Ukraine and US. According to patented technology, IQ process should satisfy the direct convection criterion and should be interrupted at proper time to create optimal hardened layer resulting in maximal surface compressive residual stresses. Equipment for performing this technology is complicated and expensive. Author proposes a new modified IQ-3M technology that provides optimized hardened layer during conventional accelerated quenching via optimizing chemical composition of steel. In contrast to existing IQ-3 process, optimized hardened layer can be achieved in any size of steel part and technology is less costly which should be widely used in heat treating
industry. It is shown that cooling process should be interrupted at a time where nano – bainitic microstructure at the core of quenched steel parts is
formed and high surface compressive residual stresses after quenching are appeared. For this purpose, an optimal hardenabily steel is used which is patented in Ukraine. The new IQ-3M technology saves alloy elements, increases service life of steel components and reduces cost of new technology. For governing quenching process, the software was developed by Intensive Technologies Ltd (ITL), Kyiv, Ukraine. The main attention is paid to physics of the quenching process that significantly simplifies recipes development. The new idea, discussed in this paper, will be useful for engineers and scientists who are working on materials savings and environment improvement.
Keywords:
Nucleate boiling absence, direct convection, IQ-3M technology, service life, material savings, environment improvement, cost reduce.
References:
[1] H.K.D.H. Bhadeshia, Bainite in Steels: Theory and Practice (3rd Edition), Money Publishing, 2015, 616.
[2] N.I. Kobasko Austempering Processes That are Performed via Cold Liquids, Lambert Academic Publishing, 2019, 16 p., DOI: 10.1520/mnl64-eb, ISBN: 978-620-0-11330-6.
[3] N.I. Kobasko, Transient Nucleate boiling as a Basis for Designing Austempering and Martempering New Technologies, SSRG International Journal of Applied Physics (SSRG-IJAP) – Volume 6, Issue 2, 2019.
[4] N.I. Kobasko, Intensive Steel Quenching Methods, Theory and Technology of Quenching, B. Liscic, H. M. Tensi, and W. Luty,Eds., Springer-Verlag, Berlin 1992, , pp. 367–389.
[5] N.I. Kobasko, Steel Quenching in Liquid Media Under Pressure, Naukova Dumka, Kyiv, 1980, 206..
[6] N.I. Kobasko, Patent US 6,364,974 B2, 2002, Quenching apparatus and method for hardening steel parts. Assignee: IQ Technologies, Inc Appl. 09/551,082. Filed 18.04.2000. Available at: http://patents.com/us-6364974.html.
[7] M.A.Mikheev and I.M.Mikheeva, Basics of Heat Transfer (In Russion), Energy, Moscow. 1977.
[8] N.I. Kobasko, J.A., M.A. Aronov, J.A. Powell, G.E. Totten, G.E.,Intensive Quenching Systems: Engineering and Design, ASTM International. W. , USA, 2010, 234.
[9] G.M. Kondrat’ev,Thermal Measurements. Moscow: Mashgiz, 1957.
[10] A.V. Lykov, Theory of Heat Conductivity, Vysshaya Shkola, Moscow, 1967, 621.
[11] N.I. Kobasko, A Universal Correlation for the Calculation o f Heating and Cooling Time of Any Steel, Materials Performance and Characterization, Vol. 6, No. 1, 2017, pp. 551 – 565, DOI: 10.1520/MPC20170034
[12] V.G. Levich, Course of Theoretical Physics, Vol. I, Physmatgiz, Moscow, 1962, 695.
[13] N.I. Kobasko,A method for optimizing chemical composition of steels to reduce radically their alloy elements and increase service life of machine components, EUREKA: Physics and Engineering, Number 1, 2017, pp.3 -12, DOI: 10.21303/2461 4262.2016.00253 .
[14] Ukrainian Patent UA 114174, C2, Alloyed Low Hardenability Steel and Method of its Designing, Filed on Sep.23, 2013, File
number: a 2013 11311, Published on June 25, 2016 in Bulletin No. 12, Legal dayis May 10, 2017.
[15] N.I. Kobasko, Optimal hardenability steel and method for Its composing, Lambert Academic Publishing, Mauritius, 2018, 126.
[16] N.I. Kobasko, N.I., High Quality Steel vs Surface Polymeric
[17] L Layer Formed during Quenching, Lambert Academic Publishing, 2019, 106.
[18] M.A. Grossmann, Principles of Heat Treatment, American Society for Materials, Ohio, USA, 1964, 302.