The Effects of Pore Size and Percentage Composition of Air Voids on Impact Energy Absorption of Al Foam using Numerical approach
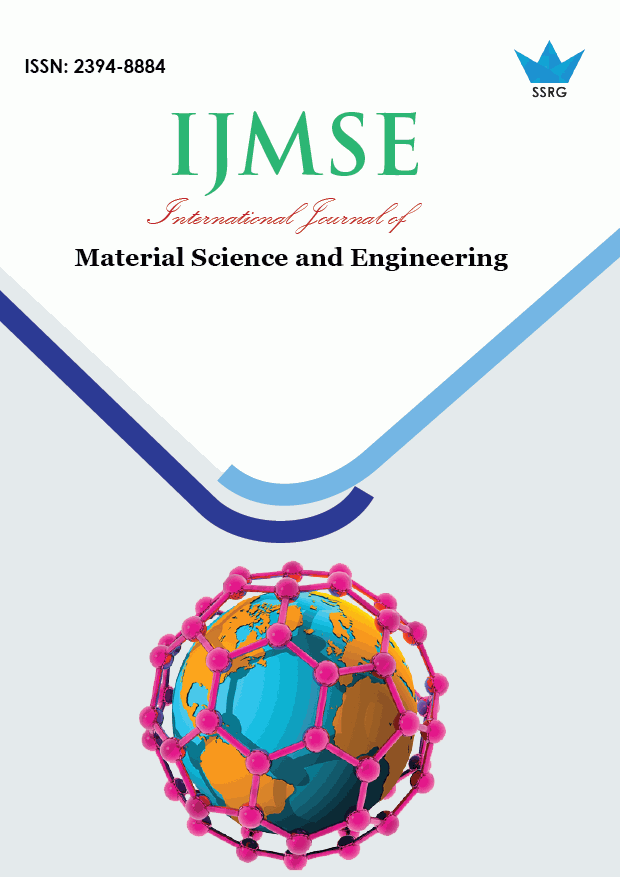
International Journal of Material Science and Engineering |
© 2023 by SSRG - IJMSE Journal |
Volume 9 Issue 1 |
Year of Publication : 2023 |
Authors : Seyfu Tiruneh Debebe |
How to Cite?
Seyfu Tiruneh Debebe, "The Effects of Pore Size and Percentage Composition of Air Voids on Impact Energy Absorption of Al Foam using Numerical approach," SSRG International Journal of Material Science and Engineering, vol. 9, no. 1, pp. 1-12, 2023. Crossref, https://doi.org/10.14445/23948884/IJMSE-V9I1P101
Abstract:
Recently, there has been a high interest in using lightweight aluminum foams for automotive, railway and aerospace operations. Because of its high ductility and deformability, Aluminum foam is generally used for energy absorption for crashworthiness applications. To keep safe and avoid occupant injuries, it is necessary to absorb the kinetic energy generated during impact. Thus, to absorb high kinetic energy, the crash box material needs a special material microstructure, which is light in weight and can absorb further energy than the being one like CaCo3, CBC, or SiC. B4C etc. In particular, the analysis of energy absorption of aluminum foam in automotive for energy absorption applications is limited. The main objective of this exploration is to analyze and optimize the porosity size and voids percentage on impact energy absorption of aluminum foam using a numerical approach. For this purpose, first, fifteen CAD Al foam samples were developed by using Digimat multi-scale material modeling software. Second, cubic elements with circular bubble shape at 5, 10 and 15 void percentage and at 1.5 mm, 2 mm,2.5 mm, 3 mm and 3.5 mm bubble sizes were modeled. Finally, the numerical analysis of impact energy by using ANSYS workbench19.2 Explicit dynamics by applying initial low velocity was performed. The parameters were compared to each other to optimize the proper percentage composition and cell size for the best energy absorption applications. The effects of bubble shape, foaming agent and percentage composition on energy immersion were discussed. In this study, the analysis was fulfilled by determining and comparing the energy absorptions of all the models and, finally, comparing them with existing foaming agents.
Keywords:
Absorption energy, Aluminum foam, Digimat, Fem analysis, Impact, Voids.
References:
[1] Xiaoqin Hao et al., "Factors Affecting the Compression and Energy Absorption Properties of Small-Sized Thin-Walled Metal Tubes," International Journal of Aerospace Engineering, vol. 2020, 2020. Crossref, https://doi.org/10.1155/2020/6135925
[2] Gauri B. Mahajan, and Dinesh N. Kamble, "Crash And Impact Strength Analysis of Structural Component of the Vehicle for Occupant Safety," International Journal of Scientific & Technology Research, vol. 4, no. 12, pp. 4288–4293, 2015.
[3] Ahmet Güner, Mustafa Merih Arıkan, and Mehmet Nebioglu, "New Approaches to Aluminum Integral Foam Production with Casting Methods," Metals - Open Access Metallurgy Journal, vol. 5, no. 3, pp. 1553–1565, 2015. Crossref, https://doi.org/10.3390/met5031553
[4] Hadi Saputra, Jamasri, and Heru S. B. Rochardjo, "The Prediction of Energy-Absorption on the Car Crush Box," 3rd International Conference on Science and Technology - Computer (ICST), pp. 51–56, 2017. Crossref, https://doi.org/10.1109/ICSTC.2017.8011851
[5] Kresimir Grilec, Gojko Maric, and Katica Milos, "Aluminium Foams in the Design of Transport Means," Promet-Traffic & Transportation, vol. 24, no. 4, pp. 295–304, 2012. Crossref, https://doi.org/10.7307/ptt.v24i4.437
[6] Hamza A. Osman, "Characterization of Aluminium Foam Produced From Aluminium Scrap By Using CaCo3 as Foaming Agent," Journal of Engineering Science, vol. 45, no. 4, pp. 448–459, 2017. Crossref, https://doi.org/10.21608/JESAUN.2017.116283
[7] Ulhas K. Annigeri and G. B. Veeresh Kumar, "Effect of Reinforcement on Density, Hardness and Wear Behavior of Aluminum Metal Matrix Composites: A Review," Materials Today Procreedings, vol. 5, no. 5, pp. 11233–11237, 2018. Crossref, https://doi.org/10.1016/j.matpr.2018.02.002
[8] Jiannan Sun et al., "A High-Similarity Modeling Method for Low-Porosity Porous Material and Its Application in Bearing Cage Self - Lubrication Simulation," Materials (Basel),vol. 14, no. 18, pp. 5449, 2021. Crossref, https://doi.org/10.3390/ma14185449
[9] M. Aboraia, R. Sharkawi, and M. A. Doheim, "Production of Aluminium Foam and the Effect of Calcium Carbonate as a Foaming Agent," Journal of Engineering Sciences, vol. 39, no. 2, pp. 441–451, 2011.
[10] N. Gupta et al., "Testing of Foams," Handbook of Mechanics of Materials, pp. 2083 - 2122, 2019. Crossref, https://doi.org/10.1007/978- 981-10-6884-3_50
[11] H. K. Farahani, M. Ketabchi, and Sh. Zangeneh, "Determination of Johnson – Cook Plasticity Model Parameters for Inconel718," Journal of Materials Engineering and Performance, vol. 26, pp. 5284–5293, 2017. Crossref, https://doi.org/10.1007/s11665-017-2990- 2
[12] Vignesh Sampath, C. Lakshmana Rao, and Santhosh Reddy, "Energy Absorption of Faom Filled Aluminum Tubes Under Dynamic Bending," Procedia Manufacturing, vol. 7, pp. 225–233, 2017. Crossref, https://doi.org/10.1016/j.promfg.2016.12.054
[13] X. C. Xia et al., " Effects of Porosity and Pore Size on the Compressive Properties of Closed-Cell Mg Alloy Foam," Journal of Magnesium and Alloys, vol. 1, no. 4, pp. 330–335, 2013. Crossref, https://doi.org/10.1016/j.jma.2013.11.006
[14] Ana M. Amaro et al., "Mechanical Characterization of Diff erent Aluminium Foams at High Strain Rates," Materials, vol. 12, no. 9, pp. 1428, 2019. Crossref, https://doi.org/10.3390/ma12091428
[15] Nallely Trejo Rivera, Jesus Torres Torres, and Alfredo Flores Valdés, "A-242 Aluminium Alloy Foams Manufacture from the Recycling of Beverage Cans," Metals (Basel), vol. 9, no. 1, p. 92, 2019. Crossref, https://doi.org/10.3390/met9010092
[16] Ramasamy Karuppasamy, N. M. Sivaram, and Debabrata Barik, "Compressive Strength of Open Cell AL-SI 12 -FE Foam Produced Through Sand Casting Method," International Journal of Mechanical Engineering and Technology, vol. 9, no. 6, pp. 459–466, 2018.
[17] R. Pippan, and C. Motz "Deformation Behaviour of Closed-Cell Aluminium foams in Tension," Acta Materialia, vol. 49, no.13, pp. 2463-2470, 2001. Crossref, https://doi.org/10.1016/S1359-6454(01)00152-5
[18] Hamza Sulayman Abdullahi. Yicheng liang, and Shuming Gao, "Predicting The Elastic Properties of Closed-Cell Aluminum Foams : A Mesoscopic Geometric Modeling Approach," SN Applied Science, vol. 1, no. 380, 2019. Crossref, https://doi.org/10.1007/s42452-019- 0382-y
[19] Tiago Miguel and Encarnacao Nunes, "Multi-Objective Design Optimization of a Frontal Crash Energy Absorption System for a Road-Safe Vehicle," Aerospace Engineering, 2017.
[20] N.A. Rahman et al., "Energy Absorption Capability and Deformation of Laminated Panels for Armoured Vehicle Materials," International Journal of Automotive and Mechanical Engineering, vol. 13, no. 3, pp. 3657–3668, 2016. Crossref, https://doi.org/10.15282/ijame.13.3.2016.10.0300
[21] Dipen Kumar Rajak, L. A. Kumaraswamidhas, and S. Das, "Experimental Analysis to Improve Energy Absorption Properties of Rectangular Metal Section Subjected to Axial Loading," Materials Today Proceeding, vol. 3, no. 6, pp. 2207–2212, 2016. Crossref, https://doi.org/10.1016/j.matpr.2016.04.127
[22] G. Kavei, "Mechanical Properties of Aluminum Foam Fabricated by Aluminum Powders with Na or Carbamide Replica," AASCIT Journal of Materials, vol. 1, no. 2, pp. 22–30, 2015.