GC/MS study of the oil recovered by the oxidative thermal degradation of the mixture of HDPE, LDPE and different natural fibers of Indian origin
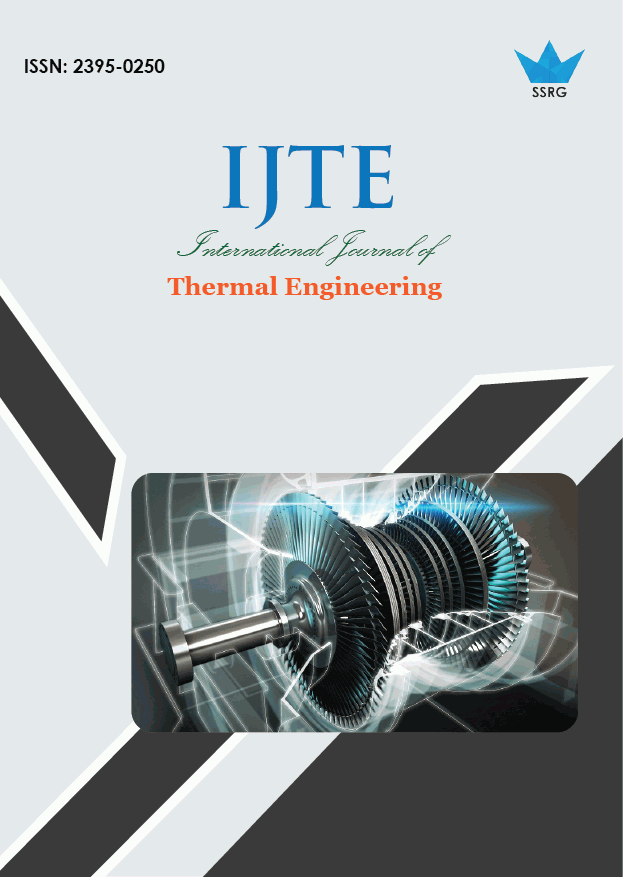
International Journal of Thermal Engineering |
© 2017 by SSRG - IJTE Journal |
Volume 3 Issue 3 |
Year of Publication : 2017 |
Authors : Savita Dixit |
How to Cite?
Savita Dixit, "GC/MS study of the oil recovered by the oxidative thermal degradation of the mixture of HDPE, LDPE and different natural fibers of Indian origin," SSRG International Journal of Thermal Engineering, vol. 3, no. 3, pp. 12-20, 2017. Crossref, https://doi.org/10.14445/23950250/IJTE-V3I5P103
Abstract:
According to the GC/MS analysis of the oil samples, recovered by the oxidative thermal degradation of the mixture of HDPE, LDPE and natural fibers of Indian origin, it was reported that on varying the natural fibers into the reaction mixture the resultant oxidative products were also varies. It was found that when the mixture of HDPE and LDPE degraded in the oxidative environment the recovered oxidative products were 1 ring chain saturated hydrocarbons, 1 saturated long chain hydrocarbon, 5 unsaturated long chain hydrocarbons and 1 methyl ester. Whenthe mixture of Jute, HDPE and LDPE thermally degraded the recovered oxidative products were 1 phytol, 2 saturated fatty acids, 2 unsaturated fatty acids and 2 silica containing derivatives, similarly when Flax fiber was used instead of Jute fiber the recovered oxidative products were 8 unsaturated long chain hydrocarbons and 3 methyl esters.
Keywords:
GC/MS, oxidative thermal degradation, hdpe, ldpe, natural fibers, oxidative products.
References:
1. M.A. Uddin, Y. Sakata, A. Muto, Y. Shiraga, K. Koizumi, Y. Kanada, K. Murata, 1998.Catalytic degradation of polyethylene and polypropylene into liquid hydrocarbons with mesoporous silica. Microporous Mesoporous Mater, 557–564.
2. J. Aguado, J.L. Sotelo, D.P. Serrano, J.A. Calles, J.M. Escola, 1997. Catalytic conversion of polyolefins into liquid fuels over MCM-41: Comparison with ZSM-5 and amorphous SiO2-Al2O3. Energy & Fuels, 11: 1225-1231.
3. T. Isoda, T. Nakahara,K. Kusakabe, S. Morooka, 1998. Catalytic cracking of polyethylene-liquefied oil over amorphous aluminosilicatecatalysts. Energy & Fuels, 12: 1161-1167.
4. J.M. Arandes, J. Eren˜ a, J. Bilbao, 2003. Valorization of polyolefins dissolved in light cycle oil over HY zeolites under fluid catalytic cracking unit conditions. Ind. Eng. Chem. Res. 42:3952- 3961.
5. J.M. Arandes, J. Eren˜ a, M. Olazar, J. Bilbao. 2004. Valorization of the blends polystyrene/light cycle oil and polystyrene- butadiene/light cycle oil over different HY zeolites under FCC unit conditions. Energy & Fuels, 18:218- 227.
6. A. Coelho, L. Costa, M.M. Marques, I.M. Fonseca, M.A.N.D.A. Lemos, F. Lemos, 2012.The effect of HZSM-5 zeolite acidity on the catalytic degradation of highdensity polyethylene using simultaneous DSC/TG analysis. Appl. Catal., A 413– 414: 183–191.
7. G. Elordi, M. Olazar, G. Lopez, M. Artetxe, J. Bilbao,2011. Continuous polyolefin cracking on an HZSM-5 zeolite catalyst in a conical spouted bed reactor. Ind. Eng. Chem. Res., 50:6061–6070.
8. J. Aguado, D.P. Serrano, J.M. Escola, E. Garagorri, J.A. Fernandez, 2000. Catalytic conversion of polyolefins into fuels over zeolite beta.Polym.Degrad. Stab.,69: 11–16.
9. G. Elordi, M. Olazar, G. Lopez, M. Amutio, M. Artetxe, R. Aguado, J. Bilbao, 2009. Catalytic pyrolysis of HDPE in continuous mode over zeolite catalysts in a conical spouted bed reactor. J. Anal. Appl. Pyrolysis, 85: 345–351.
10. K.P. Shadangi, K. Mohanty, 2015. Co-pyrolysis of Karanja and Niger seeds with waste polystyrene to produce liquid fuel. Fuel, 153: 492-498.
11. Y. Xue, S. Zhou, R.C. Brown, A. Kelkar, X. Bai, 2015. Fast pyrolysis of biomass and waste plastic in a fluidized bed reactor. Fuel, 156: 40-46.
12. P. Costa, F. Pinto, M. Miranda, R. André, M. Rodrigues, 2014.Study of the experimental conditions of the copyrolysis of rice husk and plastic wastes.Chem Eng., 39:1639-1644.
13. E. Önal, B.B. Uzun, A.E. Pütün, 2013.Bio-oil production via co-pyrolysis of almond shell as biomass and high density polyethylene. Energy Convers Manage., 78:704–10.
14. A. Aboulkas, T. Makayss, L. Bilali, K.E.l. harfi, M. Nadifiyine, M. Benchanaa, 2012. Co-pyrolysis of oil shale and High density polyethylene: Structural characterization of the oil. Fuel Processing Technology, 96: 203-208.
15. M. Brebu, S. Ucar, C. Vasile, J. Yanik, 2010. Co-pyrolysis of pine cone with synthetic polymers. Fuel, 89: 1911–8.
16. V.I. Sharypov, N. Marin, N.G.Beregovtsova, S.V. Baryshnikov, B.N. Kuznetsov, V.L. Cebolla, 2002. Copyrolysis of wood biomass and synthetic polymer mixtures. Part I: influence of experimental conditions on the evolution of solids, liquids and gases. J Anal ApplPyrol., 64: 15–28.
17. F. Paradela, F. Pinto, A.M. Ramos, I. Gulyurtlu, I. Cabrita, 2009. Study of the slow batch pyrolysis of mixtures of plastics, tyres and forestry biomass wastes. J Anal ApplPyrol., 85: 392–8.
18. E. Jakab, M. Blazsó, O. Faix, 2001.Thermal decomposition of mixtures of vinyl polymers and lignocellulosic materials. J Anal ApplPyrol., 58: 49–62.
19. S. Dixit, G. Dixit, V. Verma, 2016.Thermal degradation of polyethylene waste and jute fiber in oxidative environment and recovery of oil containing phytol and free fatty acids. Fuel, 179: 368-375. http://dx.doi.org/10.1016/j.fuel.2016.04.004