Detailed Modelling of Permanent Magnet Synchronous Motor (PMSM) for Electrical Forklifts Part-II designing of subsystem model of PMSM Block
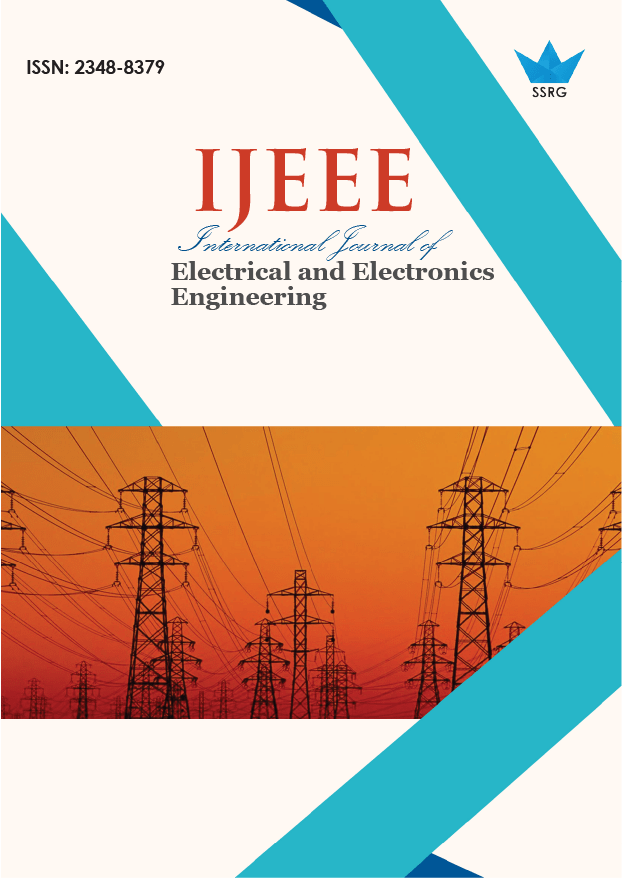
International Journal of Electrical and Electronics Engineering |
© 2016 by SSRG - IJEEE Journal |
Volume 3 Issue 11 |
Year of Publication : 2016 |
Authors : Aaditya Khare, Dr. Smita Shrivastava |
How to Cite?
Aaditya Khare, Dr. Smita Shrivastava, "Detailed Modelling of Permanent Magnet Synchronous Motor (PMSM) for Electrical Forklifts Part-II designing of subsystem model of PMSM Block," SSRG International Journal of Electrical and Electronics Engineering, vol. 3, no. 11, pp. 8-14, 2016. Crossref, https://doi.org/10.14445/23488379/IJEEE-V3I11P102
Abstract:
The research work deals with Detailed modelling of permanent magnet synchronous motor for electrical drives. In this paper we have discussed about mathematical modelling of PMSM for Electrical Forklifts designing aspects of subsystem of PMSM Block of the Main model. Permanent magnets to replace the electromagnetic pole with windings requiring a less electric energy supply source resulted in compact dc machines. Likewise in synchronous machines, the conventional electromagnetic field poles in the rotor are replaced by the PM poles and by doing so the slip rings and brush assembly are dispensed. With the advent power semiconductor devices the replacement of the mechanical commutator with an electronic commutator in the form of an inverter was achieved. These two developments contributed to the development of PMSMs and Brushless dc machines. Due to many applications of PMSM like sensor less speed control, appropriate position control, Servo motor, etc. Mathematical modelling of permanent Magnet synchronous motor is carried out and simulated using MATLAB. The most important features of PMSM is its high efficiency given with the ratio of input power after deduction of loss to the input power. There is no field current or rotor current in the PMSM.
Keywords:
Permanent Magnet Synchronous Motor, Electrical driven Forklifts, Modelling of Permanent Magnet Synchronous Motor, Distributed Magneto motive force.
References:
[1] X. Jannot, J Vannier, C.Marchand, M Gabsi, J. Saint-Michel, and D.Sa, Multiphysic Modelling of a Highspeed Interior Permanent Magnet Synchronous Machine for a Multi objective Optimal Design, IEEE TRANSACTIONS ON ENERGY CONVERSION, VOL.26, NO.2, JUNE 2011, 457-467.
[2] S. Vaez-Zadeh, A.R. Ghasemi, Design optimization of permanent magnet synchronous motors for high torque capability and low magnet volume, Electric Power Systems Research 74 (2005) 307–313.
[3] Aaditya Khare, Dr. S.K. Shriwastava, A Survey of Traction Permanent Magnet Synchronous Motor, International Journal of Science Technology & Engineering, Vol. 1,Issue 10, April 2015 ISSN (online): 2349-784X 149- 152.
[4] N. Roshandel Tavana, A. Shoulaie, Pole-shape optimization of permanent-magnet linear synchronous motor for reduction of thrust ripple, Energy Conversion and Management 52 (2011) 349–354.
[5] Hassanpour Isfahani, S. Vaez-Zadeh, Design optimization of a linear permanent magnet synchronous motor for extra low force pulsations, Energy Conversion and Management 48 (2007) 443–449.
[6] L. Parsa, H. A. Toliyat and A. Goodarzi, Five- Phase Interior Permanent-Magnet Motors With Low Torque Pulsation, IEEE TRANSACTIONS ON INDUSTRY APPLICATIONS, VOL. 43, NO. 1, JANUARY/FEBRUARY 2007, 40-46.
[7] M. S. Islam, R. Islam and T. Sebastian, Experimental Verification of Design Techniques of Permanent-Magnet Synchronous Motors for Low-Torque-Ripple Applications, IEEE TRANSACTIONS ON INDUSTRY APPLICATIONS, VOL. 47, NO.1, JANUARY/FEBRUARY 2011, 88-95.
[8] Y.Li, J.Xing, T.Wang, and Y.Lu, Programmable Design of Magnet Shape for Permanent-Magnet Synchronous Motors With Sinusoidal Back EMF Waveforms, IEEE TRANSACTIONS ON MAGNETICS, VOL. 44, NO. 9, SEPTEMBER 2008, 2163-2167.
[9] Hassanpour Isfahani, S. Vaez-Zadeh, Line start permanent magnet synchronous motors: Challenges and opportunities, Energy 34 (2009) 1755–1763.
[10] N. Bianchi, S. Bolognani, and P. Frare, Design Criteria for High- Efficiency SPM Synchronous Motors, IEEE Transactions on energy conversion, Vol. 21, NO. 2, June 2006, 396-404.
[11] Eberhart, R. C., and Kennedy, J., “a new optimizer using particle swarm theory”, Proceedings of the Sixth International Symposium on Micro Machine and Human Science, Nagoya, Japan, 39-43. Piscataway, NJ: IEEE Service Center, 1995.
[12] CM, Yang, D, Simon, "A New Particle Swarm Optimization Technique”, Proceedings of the 18th international Conference on Systems Engineering (ISCEng 2005), IEEE Computer Society, Washington (2005).
[13] TAKAO, K., URUGA, K.Gauge change EMU train outline. Railway Technical Research Institute Report, 2003, vol. 44, no. 3, p. 103-108.
[14] YOSHIDA, K. Development of main circuit system using direct drive motor (DDM). JR East Technical Review, 2002, no. 1, p. 46-52.
[15] OSAVA, M. Toward creation of a railway car meeting the 21st-century requirements. JR East Technical Review, 2002, no. 1, p. 9-12.
[16] ŠIMÁNEK, J., NOVÁK J., ČERNÝ, O., DOLEČEK, R. FOC and flux weakening for traction drive with permanent magnet synchronous motor. In IEEE International Symposium on Indus-trial Electronics. Cambridge (United Kingdom), 2008, p. 753 - 758.
[17] MIHAILOVIC, Z. Modelling and Control Design of VSI-Fed PMSM Drive Systems with Active Load. M. S. Thesis. Virginia (USA): Virginia Polytechnic Institute and State University, 1999.
[18] LETTL, J. Matrix converter hybrid drive system. WSEAS Transactions on Power Systems, 2006, vol. 1, no. 7, p. 1217-1222.
[19] Mulukutla S. Sarma, “Direct-Current Machines,” in Electric Machines, 2nd ed. Thomson Learning Inc., 1994, ch. 9, pp. 408-430.
[20] M. Aydin et al., “Axial Flux Permanent Magnet Disc Machines: A Review,” in Wisconsin Electric Machines & Power Electronics Consortium, Wisconsin Power Electronics Research Center, 2004.