Role of Lean Manufacturing Tools in Soft Drink Company
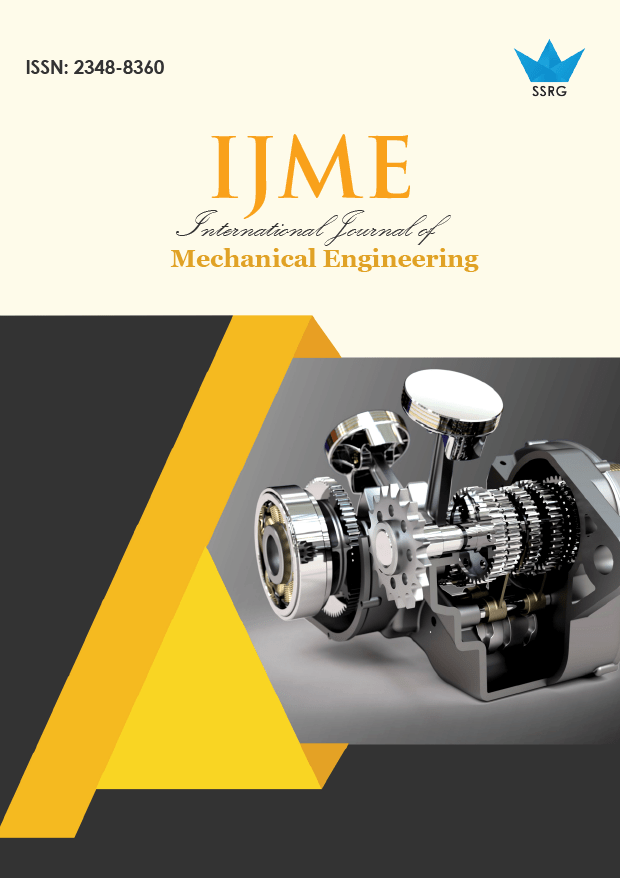
International Journal of Mechanical Engineering |
© 2018 by SSRG - IJME Journal |
Volume 5 Issue 1 |
Year of Publication : 2018 |
Authors : Shaik Dawood A.K., Elsayed A Elsayed, Abdul Rahaman, R. Karthikeyan |
How to Cite?
Shaik Dawood A.K., Elsayed A Elsayed, Abdul Rahaman, R. Karthikeyan, "Role of Lean Manufacturing Tools in Soft Drink Company," SSRG International Journal of Mechanical Engineering, vol. 5, no. 1, pp. 1-7, 2018. Crossref, https://doi.org/10.14445/23488360/IJME-V5I1P101
Abstract:
In a present customer-driven market, it urges the industry to implement lean tools to reduce waste. This paper utilizes the applications of Lean manufacturing tools like Value Stream Mapping (VSM) and Jidoka in continuously improving bottle filling and crowning operations at soft drink companies. Waste reduction becomes an increasingly dominant force in the modern manufacturing world. The most important tools in Jidoka are Andon and Poka-Yoke. Andonis a visual control that helps the operator notify the machines' status and manufacturing line in the manufacturing process. Poka-yoke devices are made for mistake-proving pieces. Because of that, they can be classified as proactive and reactive devices. The proactive prevents the defects, and the reactive detects the defects once they are already produced. The main parameters taken are missing operation, underfill, overfill, breakages. Data are collected for the filling and crowning operations so that the facts about the problem are accurately described. Pareto charts and cause & effect diagrams are used to present the key problems which can be improved. This paper also deals with the productivity improvement using VSM on the assembly line. It is a lean venture towards perfection and an attempt to identify non-value adding activities, thereby enhancing productivity.
Keywords:
Jidoka, Value stream mapping (VSM), Lean Manufacturing (LM), Andon, Poka-yoke
References:
[1] Abdulmalek FA, Rajgopal J, "Analyzing the benefits of lean manufacturing and value stream mapping via simulation: a process sector case study," Int J Prod Econ, 223–236, 2007.
[2] Serrano I, Ochoa C, de Castro R, "Evaluation of value stream mapping in manufacturing system redesign."Int J Prod Res, 4409–4430, 2008.
[3] Sahoo AK, Singh NK, Shankar R, Tiwari MK, "Lean philosophy: implementation in a forging company," Int J AdvManufTechnol, 451–462, 2008.
[4] Ohno, T., 1982. "The origin of the Toyota production system and kanban system."Prodcedings of the International Conference on Productivity and Quality Improvement.Tokyo, 1982.
[5] ShaikDawood A.K., RiyazAhamed A., Karthikeyan.R. "Lean manufacturing in measuring customer expectations at an airport," International Journal of current research, Volume 6, Issue 9 (2014).pp-8380-8383
[6] Womack JP, Jones DT, "Lean thinking: banish waste and create wealth for your corporation," Simon & Schuster, New York, 1996.
[7] Womack JP, Jones D, "Lean thinking: banishing waste and create wealth in your corporation," New York, 2003.
[8] Shah R, Ward PT, "Defining and developing measures of lean production," J OperManag 25:785–805, 2007
[9] Miltenburg J, "One-piece flow manufacturing on U-shaped production lines: a tutorial," IIE Trans 33(4):303–321, 2001
[10] Calvo R, Domingo R, Sebastián MA, "Operational flexibility quantification in a make-to-order assembly system," Int J FlexManufSyst, 247–263, 2007
[11] ElMaraghy HA, "Flexible and reconfigurable manufacturing systems paradigms," Int J Flex ManufSyst, 261–276, 2005
[12] Shingo, S. "Study of Toyota Production System from Industrial Engineering Viewpoint," Japan Management Association, Tokyo. (1981)
[13] Ortiz, C.A. (2006), Kaizen Assembly: "Designing, Constructing, and Managing a Lean Assembly Line," Taylor and Francis Group, Boca Raton, FL.
[14] Serrano I, Ochoa C, de Castro R, "Evaluation of value stream mapping in manufacturing system redesign."Int J Prod Res,4409–4430, 2008.
[15] Tommelein, I.D. and Grout, J, Mistake "Proofing Architecture, Engineering, and Construction Processes."Project Production Systems Laboratory (P2 SL), U.C. Berkeley, CA, forthcoming. (, 2008).