Implementation of Response Surface Methodology for Analysis of Milling Process Using Multi Point Cutting Tool for Surface Finish
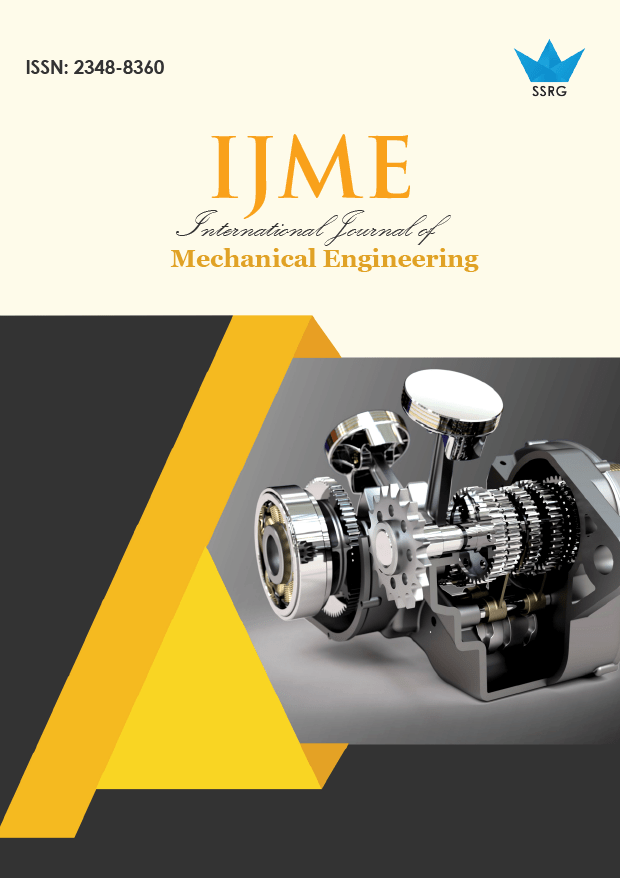
International Journal of Mechanical Engineering |
© 2015 by SSRG - IJME Journal |
Volume 2 Issue 7 |
Year of Publication : 2015 |
Authors : Prof. (Dr) .V. R. Naik, Mr.G.C.Mekalke, Mr.A.V.Sutar |
How to Cite?
Prof. (Dr) .V. R. Naik, Mr.G.C.Mekalke, Mr.A.V.Sutar, "Implementation of Response Surface Methodology for Analysis of Milling Process Using Multi Point Cutting Tool for Surface Finish," SSRG International Journal of Mechanical Engineering, vol. 2, no. 7, pp. 1-7, 2015. Crossref, https://doi.org/10.14445/23488360/IJME-V2I7P101
Abstract:
This paper investigates the effect of cutting speed, feed rate and depth of cut on the surface roughness of components of mild steel material. The response surface methodology (RSM) was employed in the experiment. The investigated milling parameters were cutting speed (105, 225RPM) and depth of cut (0.75 and 1.5 mm) and no. of cuts (1 and 2). The results showed that the speed and no. of cut were the primary factors controlling surface roughness. The responses of various factors were plotted using a three-dimensional surface graph. The optimum condition required for minimum surface roughness includes cutting speed of 225RPM and no. of cut 2. Depth of cut has no significant effect on surface roughness of the components. With this optimum condition, a surface roughness of 1.32μm was obtained.
Keywords:
High-speed milling, Surface roughness, Response surface method, etc.
References:
[1] G. Boothroyd, W.A. Knight, Fundamentals of Machining and MachineTools, third ed., CRC press, Taylor & Francis Group, 2006.
[2] D.C. Montgomery, Design and Analysis of Experiments, fourth ed.,John Wiley & sons Inc., 1997.
[3] Ashvin J. Makadiaa and J.I. Nanavatib, Optimisation of machining parameters for turning operationsbased on response surface methodology,Gujarat Technology University, At. Hadala,Rajkot 363 650, Gujarat, India.Measurement 46 (2013) 1521–1529.
[4] Lei Yu, Yunlong Zheng, and Purnendu K. Das “Stepwise Response Surface Method and its Application in Reliability Analysis of Ship Hull Structure”, Journal of Offshore Mechanics and Arctic Engineering NOVEMBER 2002, Vol. 124, Page no. 226 to 230.
[5] A. Brient, M. Brissot, T. Rouxel, J.-C. Sangleboeuf, “Influence of Grinding Parameters on Glass Workpieces Surface Finish Using Response Surface Methodology”, Journal of Tribology, ASME OCTOBER 2010, Vol. 132 / 044505-1-6.
[6] M. S. Patil, Jose Mathew, P. K. Rajendrakumar, Sumit Karade, “Experimental Studies Using Response Surface Methodology for Condition Monitoring of Ball Bearings”, Journal of Tribology ASME OCTOBER 2010, Vol. 132 / 044505-1-6.
[7] Sachindra K. Rout, Ahmed Kadhim Hussein,“Multi - Objective Optimization Of A Three-Dimensional Internally Finned Tube Based On Response Surface Methodology (RSM)”, Journal of Thermal Engineering, Vol. 1, No. 2, pp. 131-142, 2015.
[8] K.Logesh, P.Muralinath, N.Poyyamozhi ,N.Dilip Raja, A.Yassar Dawood, “Optimization of Cutting Factors Which influence Temperature on Tip of Tool in response to Surface Finish for an Aluminium Alloy AL6063 during Turning Process on CNC Lathe”, International Journal of Mechanical & Mechatronics Engineering IJMME-IJENS Vol:14 No:06, 72-75.
[9] M. Thiyagu, L. Karunamoorthy, N. Arunkumar, “Experimental Studies in Machining Duplex Stainless Steel using Response Surface Methodology”, International Journal of Mechanical & Mechatronics Engineering IJMME-IJENS Vol:14 No:03, 48-61.
[10] Pratik A. Patil, C.A. Waghmare, “Optimization Of Process Parameters In Wire-EDM Using Response Surface Methodology”, International Journal of Mechanical And Production Engineering, ISSN: 2320-2092, Volume- 2, Issue-8, Aug.-2014.