Pitting action due to bubble formation in the Cooling fluid of a piston liner
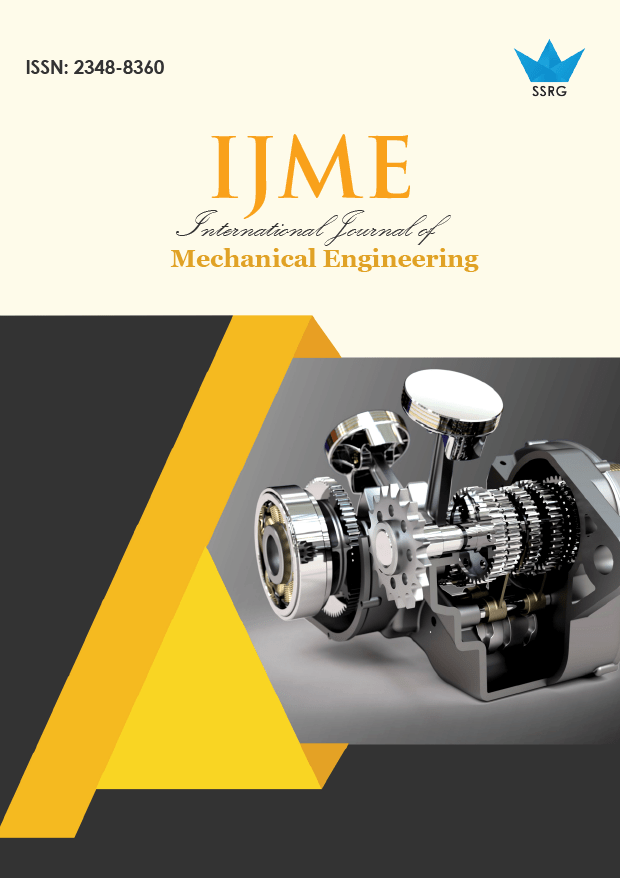
International Journal of Mechanical Engineering |
© 2014 by SSRG - IJME Journal |
Volume 1 Issue 6 |
Year of Publication : 2014 |
Authors : Mandadi Raviraju, Dr.V.Krishna Reddy |
How to Cite?
Mandadi Raviraju, Dr.V.Krishna Reddy, "Pitting action due to bubble formation in the Cooling fluid of a piston liner," SSRG International Journal of Mechanical Engineering, vol. 1, no. 6, pp. 5-10, 2014. Crossref, https://doi.org/10.14445/23488360/IJME-V1I6P103
Abstract:
During the reciprocation motion of the piston in the cylinder, the piston exerts small amount of forces on the piston skirt due to the taper in the piston design. These forces tend to develop deflections on the cylinder liner. Because of these deflections there is every possibility of disturbance in the coolant around the cylinder liner. Because of this reason bubbles are formed and destroyed in the coolant. These bubbles are also formed due to excessive harmonic vibrations of the engine and also by loosely fitted liners. The continuous formation and destruction of bubbles in the cylinder liner coolant releases energy which will attack the cylinder liner and pitting action is caused. Because of this pitting action the life of the cylinder liner decreases.
In this project study of these forces and vibrations are done using CAD/CAE softwares. The main objective of this project is to study the presence of cavitation and find the possible ways of increasing the life of the engine components. Modal analysis followed by harmonic analysis is carried out in the frequency range of 0-100Hz.The thermal loads applied from the combustion chamber and fluid structure interaction is also considered for the analysis. The presence of cavitation is shown as negative pressure in the analysis. A model has been built out using Modeling software UNIGRAPHICS NX.Finite Element Analysis software Ansys is used to performharmonic analysis. The pressure distribution in the cylinder liner is plotted and discussed.
Keywords:
Create the 3D model of the cylinder liner in UNIGRAPHICS NX
References:
1. AWWA Manual M49, Butterfly Valves: Torque, Head Loss, and Cavitation Analysis. pp. 27-32.
2. Rahmeyer, William J., Journal AWWA, November 1986. “Test Procedures for Determining Cavitation Limits in Control Valves,” pp 55-58.
3. Rahmeyer, William J., Val-Matic Test Report No. 1011, “Test Report on the Hydraulic Performance of a 4” Plug Valve Owned by Val-Matic Valve”, Utah State University Lab Report No. USU-180h. [Confidential].
4. Winn, W. Paul. Journal AWWA, March 1972. “Throttling Valves: Testing and Selection,” pp. 163-169
5. F.Ronald Young,(1989), Wartford college, Hertfordshire, Cavitation McGraw-Hill Publishing company.
6. E.E. Ungar, D.Ross, (1964),Journal of Vibration and Noise Due to Piston-Slap in reciprocating Machinery, PP(132-146).
7. R. T. Knapp, J.W.Daily, F.G.Hammitt, (1970), Cavitation, McGraw- Hill Publishing Company.
8. W.J. Griffiths and J. Skorecki, (1964). Journal of Some Aspects of Vibration of a Single Cylinder Diesel Engine PP(345-364)
9. S. D.Hadad and P.W Fortscue,(1976), Journal of Simulating Piston Slap by Analogue Computer PP(79-80)
10. Brennen, C. 1969. The dynamic balances of dissolved air and heat in natural cavity flows. J. Fluid Mech. 37: 1 15-27 (1 plate)
11. Edstrand, H. 1950. Cavitation tests with model propellers in natural sea water with regard to the gas content of the water and its effect upon cavitation point and propeller characteristics. SSPPA Rep. No. 5. Goteborg, Sweden