Review Parameters of Electrochemical Machining For 410b Stainless Steel
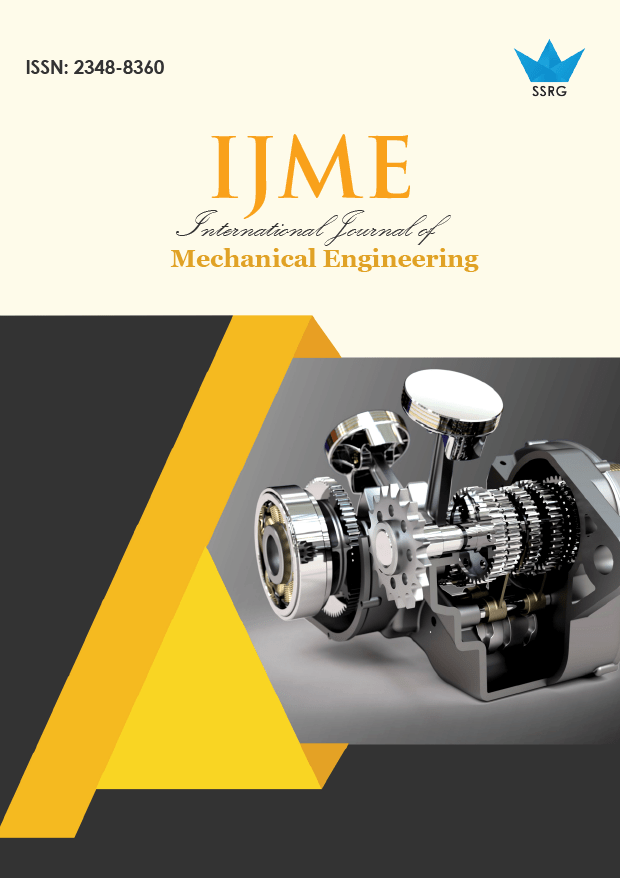
International Journal of Mechanical Engineering |
© 2019 by SSRG - IJME Journal |
Volume 6 Issue 1 |
Year of Publication : 2019 |
Authors : A.Rajeshkumar, Dr.S.Venkatesan |
How to Cite?
A.Rajeshkumar, Dr.S.Venkatesan, "Review Parameters of Electrochemical Machining For 410b Stainless Steel," SSRG International Journal of Mechanical Engineering, vol. 6, no. 1, pp. 1-6, 2019. Crossref, https://doi.org/10.14445/23488360/IJME-V6I1P101
Abstract:
This paper efforts to improve the prevailed machining parameters in electrochemical machining (ECM) of grade 410b stainless steel using reaction surface methodology (RSM). the chosen material has been used in gas turbines. The show examines researches on the impact of process factors, for example, electrolytic focus, voltage, and feed rate on execution attributes of surface roughness (SR) when ECM of grade 410b stainless steel by a copper tool in a fluid arrangement of NaClsolution. It was likewise watched that the ECM had been an economical and other option to traditional machining in the case of hard materials.Machining constraints affecting surface roughness and their influence have been discussed. This advancement, importance, and the increasing significance of electrochemical machining have been analyzed.
Keywords:
ECM, RSM, SR
References:
[1] Pott, P. G., 1989, "Modern Electrochemical in Practice," Proc. of the 9th International Symposium on Electromachining, Japan, pp. 146-150.
[2] Risko, D. G., 1989, "New ECM Systems and Applications," SME Tech. Paper MR89-418.
[3] Rajurkar, K. P., 1989, "Electrochemical and Electro-discharge Machining," Proc. of the Third Biennial International Manufacturing Technology Research Forum, pp. 219-240.
[4] McGeough, J. A., 1974, Principle of Electrochemical Machining, Chapman and Hall.
[5] Rajurkar, K. P., and Schnacker, C. L., 1988, "Some Aspects of ECM Performance and Control," Annals of the CIRP, Vol. 37/1, pp. 183-186.
[6] Electrochemical Machining, Tech Application, 1987, Center for Metals Fabrication, Vol. 1, No. 10.
[7] Astroshchenko, V. V., 1988, "Automatic System for Adjusting the Electrode Gap," Soviet Engineering Research, Vol. 2, No. 4, pp. 99-100 (from Stanki Instrument, Vol. 53, No. 4, 1988, pp. 27-29).
[8] Kozak, J., et al., 1988, "Characteristics of the Pulse Electrochemical Machining," Research and Technological Development in Nontraditional Machining, PED-Vol. 34, K. P. Rajurkar, ed., ASME Winter Annual Meeting, Chicago.
[9] Kurita, T., et al., “Mechanical/electrochemical complex machiningmethod for efficient, accurate, and environmentally benignprocess”. International Journal of Machine Tools and Manufacture, 2008. 48(15): p. 1599-1604.
[10] Pa, P.S., “Electrode form design of large holes of die material inultrasonic electrochemical finishing”. Journal of MaterialsProcessing Technology, 2007. 192–193(0): p. 470-477.
[11] Zeng, Z., et al., “A study of micro-EDM and micro-ECM combined milling for 3D metallic micro-structures” Precision Engineering, 2012. 36(3): p. 500-509.
[12] Nguyen, M.D., M. Rahman, and Y.S. Wong, “Simultaneous micro-EDM and micro-ECM in low-resistivity deionized water”. International Journal of Machine Tools and Manufacture, 2012.54–55(0): p. 55-65.
[13] Nguyen, M.D., M. Rahman, and Y.S. Wong, “Enhanced surface integrity and dimensional accuracy by simultaneous micro-
ED/EC milling. CIRP Annals - Manufacturing Technology,", 2012. 61(1): p. 191-194.
[14] Mr. SumitBhandari, Mr. NitinShukla, "Parametric Optimization of Electrochemical Machining Process by Particle Swarm Optimization Technique" SSRG International Journal of Mechanical Engineering 2.5 (2015): 6-11..
[15] Stephen, A. and F. Vollertsen, “Mechanisms and processing limits in laser thermochemical machining”. CIRP Annals - Manufacturing Technology, 2010. 59(1): p. 251-254.
[16] De Silva, A.K.M., et al., “Thermal effects in laser-assisted jet electrochemical machining." CIRP Annals – Manufacturing Technology, 2011. 60(1): p. 243-246.
[17] Kawashima, N. and T. Kurita, “Laser and electrochemical complex machining of micro-stent with on-machine three-dimensional measurement.” Optics and Lasers in Engineering, 2012. 50(3): p. 354-358.
[18] Wang, W., et al., “Abrasive, electrochemical multi-wire slicing of solar silicon ingots into wafers”. CIRP Annals – Manufacturing Technology, 2011. 60(1): p. 255-258.
[19] Curtis, D.T., et al., “Electrochemical superabrasive machining of a nickel-based aero-engine alloy using mounted grinding points." CIRP Annals - Manufacturing Technology, 2009. 58(1): p. 173-176.
[20] Zhu, D., et al., “Precision machining of small holes by the hybrid process of electrochemical removal and grinding." CIRP Annals Manufacturing Technology, 2011. 60(1): p. 247-250.
[21] Skoczypiec, S., “Research on ultrasonically assisted electrochemical machining process”. The International Journal of Advanced Manufacturing Technology, 2011. 52(5): p. 565-574.
[22] Pa, P.S., “Superfinishing with ultrasonic and magnetic assistance in electrochemical micro-machining”.ElectrochimicaActa, 2009. 54(25): p. 6022-6027.
[23] D. L. Panchal, S. K. Biradar, V. Y. Gosavi" Analysis of EDM Process Parameters by Using Coated Electrodes", International Journal of Engineering Trends and Technology (IJETT), V41(4),181-185 November 2016. [24] Pajak, P.T., et al., “Precision and efficiency of laser-assisted jet electrochemical machining”.Precision Engineering, 2006. 30(3): p. 288-298.