Conjugate Heat Transfer Analysis of Gas Turbine Disc and Cavities
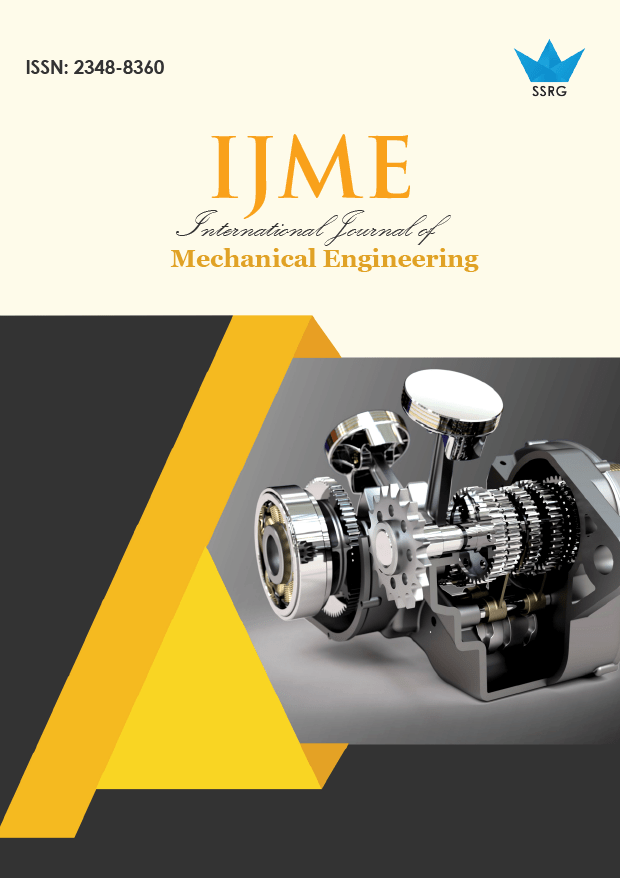
International Journal of Mechanical Engineering |
© 2018 by SSRG - IJME Journal |
Volume 5 Issue 9 |
Year of Publication : 2018 |
Authors : Chethan.K.R, Dr.H.R.Purushothama |
How to Cite?
Chethan.K.R, Dr.H.R.Purushothama, "Conjugate Heat Transfer Analysis of Gas Turbine Disc and Cavities," SSRG International Journal of Mechanical Engineering, vol. 5, no. 9, pp. 22-28, 2018. Crossref, https://doi.org/10.14445/23488360/IJME-V5I9P104
Abstract:
The Contemporary gas turbines are operated at very high main stream inlet temperatures to increase the thrust. The turbine inlet temperatures are far above the material temperature limits for turbine blades, these heat from the blade is conducted to blade platform and also to turbine disc. Hence the air is tapped at some stages of compressor and used as coolant. Thermal gradients are developed inside the material as it is exposed to low temperature secondary air. Thermal stress will develop inside the component if the thermal gradient factor is more, this will causes malfunctioning of the components which leads to failure of the disc. In order to avoid this, first we need to know the temperature distribution and thermal gradient over the material. The heat from the blade is transferred to disc and then heat will be taken away by the secondary air by convection. This process can be properly capture by conjugate heat transfer analysis. The primary aim of this project is to estimate the temperature (temperature gradient) on discs and also recognize the flow path inside the cavities. Hence conjugate heat transfer analysis is carried for the static and rotational case by considering it as 2D axi-symmetrical geometry. Mesh has been generated in Ansys pre-processor with acceptable mesh quality of 0.45. The analysis is carried out by using k-ϵ turbulence model with enhanced wall function, using Ansys Fluent16.0.
Keywords:
Turbine disc, Secondary air flow, Cavities, Conjugate heat transfer
References:
[1] P. R. Fathring1, C. A. Long, M. J. Owen2, J. R. Pincombe, “Rotating cavity with axial throughflow of colling air: heat transfer” journal of turbomachinery, Vol 144 January 1992.
[2] S. H. Bhavani, J. M. Khodadadi, J. S. Goodling, J. Waggott “An Experimental Study of Flow in Disc Cavities”. Transition of ASME, Vol. 114, April 1992.
[3] A. P. Morse, “Application of a low Reynolds number k-ϵ turbulence model to high- speed rotating cavity flows”, Transitions of ASME Vol. 113, Jaunuary 1991.
[4] P. R. Farthing1, C. A. Long, J. M. Owen2, J. M. Owen2, J. R. Pincomb, “ Rotating cavity with axial throughflow of cooling air: Flow structure” Vol 144 January 1992,
[5] G. P. Virr, J. W. Chew, J. Coupland “Application of Computational Fluid Dynamics to Turbine Disc Cavities”. Journal of Turbomachinery, Vol. 116 October 1994.
[6] Michael Ebert, Wei Shyy, Siddharth Thakur and Corin Segal, “Heat Transfer and Fluid Flow In Rotating Cavities”, 37th American Institute of Aeronautics and Astronautics Aerospace Sciences Meeting and Exhibit. AIAA-99-0737 January 11-14, 1999/ Reno
[7] Gain Paolo Berettaa, Enrico Malafab1, “Flow and Heat Transfer in Cavities Between Rotor and Stator Disc”. International Journal of heat and Mass Transfer 46 (2003).
[8] Z. X. Yuan, N. Saniel, X. T. Yan, “Turbulent heat transfer on the stationary disc in a rotor- stator system”.International Journal of heat and Mass Transfer 46 (2003).
[9] Peter E. J. Smith, Jonathan Mugglestone, kok Mu Tham, Christopher A. Long and Daniel D. Coren “Conjugate Heat transfer Analysis of Turbine Disc and Cavities”,ASME Turbo Expo 2012, Turbine technical conference and exposition, Vol.4 Heat transfer.
[10] Yoji Okita and Shigemichi Yamawaki “Conjugate Heat Transfer Analysis of Turbine”. ASME Turbo Expo Vol.3 2002.