Analysis of Welded Joint Used in Pipeline Support Using Finite Element Method
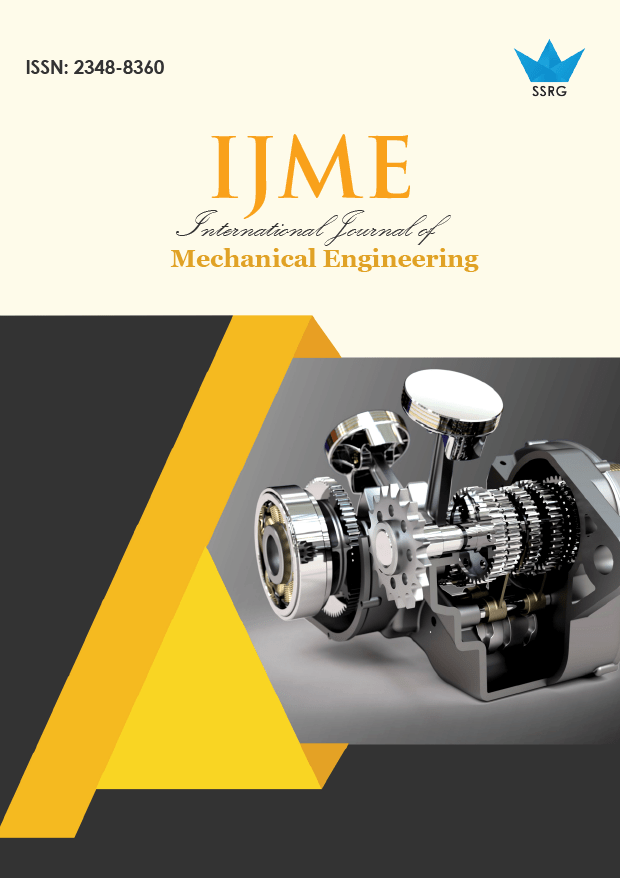
International Journal of Mechanical Engineering |
© 2020 by SSRG - IJME Journal |
Volume 7 Issue 6 |
Year of Publication : 2020 |
Authors : Samad Gadiwale, S. A. Kore |
How to Cite?
Samad Gadiwale, S. A. Kore, "Analysis of Welded Joint Used in Pipeline Support Using Finite Element Method," SSRG International Journal of Mechanical Engineering, vol. 7, no. 6, pp. 41-46, 2020. Crossref, https://doi.org/10.14445/23488360/IJME-V7I6P107
Abstract:
The design of the welded joint is a critical issue in the offshore industries. This paper presents the studies on the fillet welded joint analysis used in the offshore industry pipeline support. A fillet welded T-joint was designed theoretically according to the specifications. Linear static analysis was carried out in detail using the finite element method (FEM) for finding out the peak stress locations at the root of the joint. The experimental stress analysis of the joint was performed using the strain gauge technique. The results obtained using experimental analysis were in good agreement with the FEM analysis results. The T-joint dynamic response analysis was carried out at the end, using FEM to simulate the real loading conditions.
Keywords:
Fillet welded T-joint, finite element method, experimental stress analysis, strain gauge, dynamic analysis
References:
[1] Vakili-Tahami F, Zehsaz M, Saeimi-Sadigh MA and Seyedreyhani, Finite element analysis of the in-service-welding of t joint pipe connections, Eur. J. Sci. (2010) Res.40 557–68.
[2] Chee NC, Rahim A and Bakar A ,Finite element modeling of arc welded joints, J. Mek. (2010) 15–30.
[3] Anca,Andres,Cardona,Alberto,FachinottiV, Finiteelementmodeling of welded joints,Asoc.Argentina Mecánica Comput.XXVII, (2008 ) 10–3.
[4] Srivastava V and Rao A Modeling of Residual Stresses in a Butt-welded Joint with Experimental Validation Proceedings oftheCOMSOL Conference Pune, India .(2015).
[5] Vivio F, A new theoretical approach for structural modeling of riveted and spot welded multi-spot
structures,Int. J. Solids Struct. (2009) 46 4006–24.
[6] Erny C, Thevenet D, Cognard J-Y and Korner M, Fatigue assessment of naval welded assemblies,Procedia, (2010)Eng.2 603–12.
[7] Pakandam F and Varvani-FarahaniA, A comparative study on fatigue damage assessment of welded joints under uniaxial loading based on energymethods Procedia ,(2010) Eng.2 2027–35.
[8] Qu W, Wang M and Zhou Q , Effect of Welding Residual Stress on Along-Wind Fatigue Life of Welded Joints in Guyed Mast, Shock Vib.(2020).
[9] Khoshroyan A and Darvazi A , Effects of welding parameters and welding sequence on residual stress and distortion in Al6061-T6 aluminum alloy for T-shaped welded joint Tran"s. Nonferrous Met. Soc. China, (2010) English Ed.30 76–89.
[10] Barsoum Z and Barsoum I, Residual stress effects on fatigue life of welded structures using LEFM, (2009)Eng. Fail. Anal.16 449–67.
[11] Campagnolo A, Vormwald M, Shams E and MeneghettiG,Multiaxial fatigue assessment of tube-tube steel joints with weld end using the peak stress method,Int.J. Fatigue135 105495 (2020).
[12] Baik B, Yamada K, and IshikawaT,Fatiguecrack propagation analysis for welded joint subjected to bending, Int. J. Fatigue33 746–58 (2011).
[13] Neha B. Thakare, A. B. Dhumne, A Review on Design and Analysis of Adhesive Bonded Joint by Finite Element Analysis, SSRG International Journal of Mechanical Engineering. 2(4) (2015):17-20.
[14] COMSOL,Structural Mechanics Module User's Guide (Version 5.4), (2018).
[15] VISHAY PRECISION GROUP Strain Gage Rosettes: Selection, Application and Data Reduction(2010).
[16] Bhandari V B, Design of Machine Elements(Tata McGraw-Hill Education) (2010).