Effects of Low-Frequency Vibration Integrated With Workpiece On Quality Indicators In Wire Electrical Discharge Machining
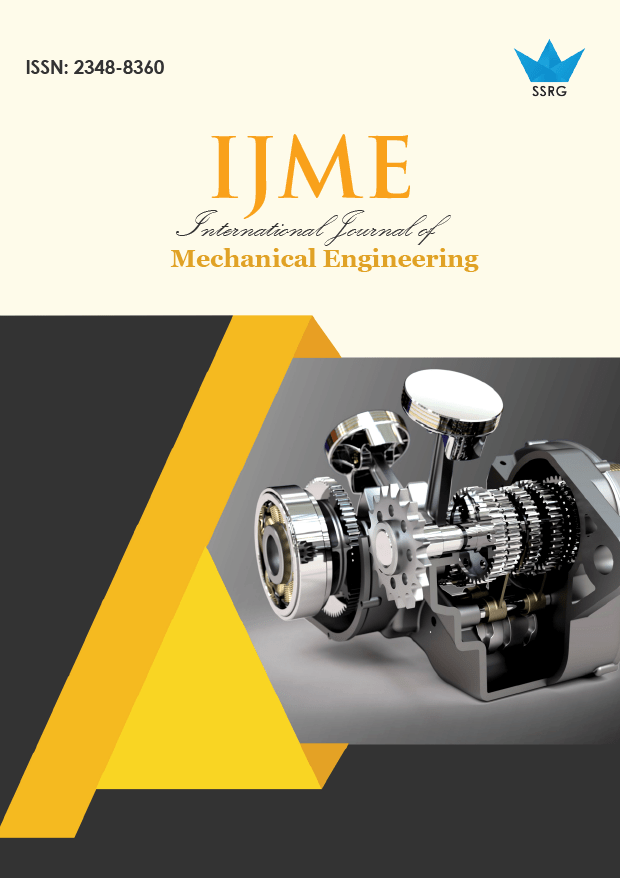
International Journal of Mechanical Engineering |
© 2020 by SSRG - IJME Journal |
Volume 7 Issue 9 |
Year of Publication : 2020 |
Authors : Nguyen Huu Phan, Kouamgmanivanh Vilasak, Nguyen Duc Luan, Bui Tien Tai, Nguyen Duc Minh, Tran Manh Thang |
How to Cite?
Nguyen Huu Phan, Kouamgmanivanh Vilasak, Nguyen Duc Luan, Bui Tien Tai, Nguyen Duc Minh, Tran Manh Thang, "Effects of Low-Frequency Vibration Integrated With Workpiece On Quality Indicators In Wire Electrical Discharge Machining," SSRG International Journal of Mechanical Engineering, vol. 7, no. 9, pp. 15-19, 2020. Crossref, https://doi.org/10.14445/23488360/IJME-V7I9P103
Abstract:
The improvement of productivity and surface quality in the WEDM process is an interesting research area in the present situation. In the present study, an attempt has been made to introduce low-frequency vibration assigned to the workpiece for improving machining surface quality and productivity. SKD11 die steel was used as a workpiece with the brass wire as the electrode. The moving direction of the wire perpendicular to the impact direction of vibrations has been investigated. It has been found that machining productivity has been improved. However, the machining surface texture is not significantly affected by the proposed method.
Keywords:
Electrical Discharge Machining, Vibration
References:
[1] Pandey, A., Singh, S., Current research trends invariants of Electrical Discharge Machining: A review, International Journal of Engineering Science & Technology. 2(6) 2010 2172-2191.
[2] Zhu, G., Zhang, M., Zhang, Q., Song, Z.C., Wang, K., Machining behaviors of vibration-assisted electrical arc machining of W9Mo3Cr4V, Int J AdvManuf Technol. 96(1-4) (2018) 1073–1080.
[3] Maity, K.P., Choubey, M., A review on vibration-assisted EDM, micro-EDM, and WEDM, Surface Review and Letters. 26(5) (2018).
[4] Kumar, S., Grover, S., OptimisationOptimization.strategies in ultrasonic vibration-assisted electrical discharge machining: a review, Int. J. Precision Technology. 7(1) (2017) 51-83.
[5] T. Endo, T. Tsujimoto, and K. Mitsui., Study of vibration-assisted micro-WEDM – The effect of vibration on machining time and stability of discharge, Precision Engineering. 32 (4) (2008) 269-277.
[6] Huu-Phan Nguyen, Ngoc-Vu Ngo., Quoc–Tuan Nguyen, OptimisingOptimizing process parameters in EDM using low frequency vibration for material removal rate and surface roughness, Journal of King Saud University-Engineering Sciences, https://doi.org/10.1016/j.jksues.2020.05.002. (2020).
[7] Guo, Z.N., Lee, T.C., Yue, T.M., Lau W.S., A study of ultrasonic-aided wire electrical discharge machining, Journal of Materials Processing Technology. 63 (1997) 823-828.
[8] Guo, Z.N., Lee, T.C., Yue, T.M., Lau W.S., Study on the machining mechanism of WEDM with ultrasonic vibration of the wire, Journal of Materials Processing Technology. 69 (1997) 212-221.
[9] HuuPhan, N., Muthuramalingam, T., Multi-Criteria Decision Making of Vibration Assisted EDM Process Parameters on Machining Silicon Steel Using Taguchi-DEAR Methodology, Silicon, https://doi.org/10.1007/s12633-020-00573-4.https://doi.org/10.1007/s12633-020-00573-4. (2020)
[10] Huu-Phan Nguyen, Van-Dong Pham., Single objective optimization of die-sinking electrical discharge machining with low-frequency vibration assigned on the workpiece by Taguchi method, Journal of King Saud University-Engineering Sciences, https://doi.org/10.1016/j.jksues.2019.11.001.(2019).
[11] HUU, P.N., TIEN, L.B., DUC, Q.T., et al., Multi-objective optimization of process parameter in EDM using low-frequency vibration of workpiece assigned for SKD61, Sādhanā 44, 211,https://doi.org/10.1007/s12046-019-118y.(2019).
[12] Tran Thanh Hoang, Tran AnhDuc, Nguyen ManhCuong, LuuAnh Tung, Le Xuan Hung, Vu Ngoc Pi., Modelling Surface Finish in Electrical Discharge Machining Tablet Shape Punches using Response Surface Methodology, SSRG International Journal of Mechanical Engineering. 4(9) (2017) 28-30.
[13] T Muthuramalingam, A. Ramamurthy, KhajaMoiduddin, Mohammed Alkindi, SundarRamalingam, Osama Alghamdi., Enhancing the Surface Quality of Micro Titanium Alloy Specimen in WEDM Process by Adopting TGRA-Based OptimisationOptimization, Materials. 13(6) (2020) 1440.
[14] T Muthuramalingam, A Ramamurthy, K Sridharan, S Ashwin., Analysis of surface performance measures on WEDM processed titanium alloy with coated electrodes, Materials Research Express. 5(12) (2018) 126503.
[15] Hoang, K.; Yang, S., A study on the effect of different vibration-assisted methods in micro-WEDM, J. Mater. Process. Technol. 213 (2013) 1616–1622.