Hardening of Low and Optimal Hardenability Steels and their Physical Processes Explanation
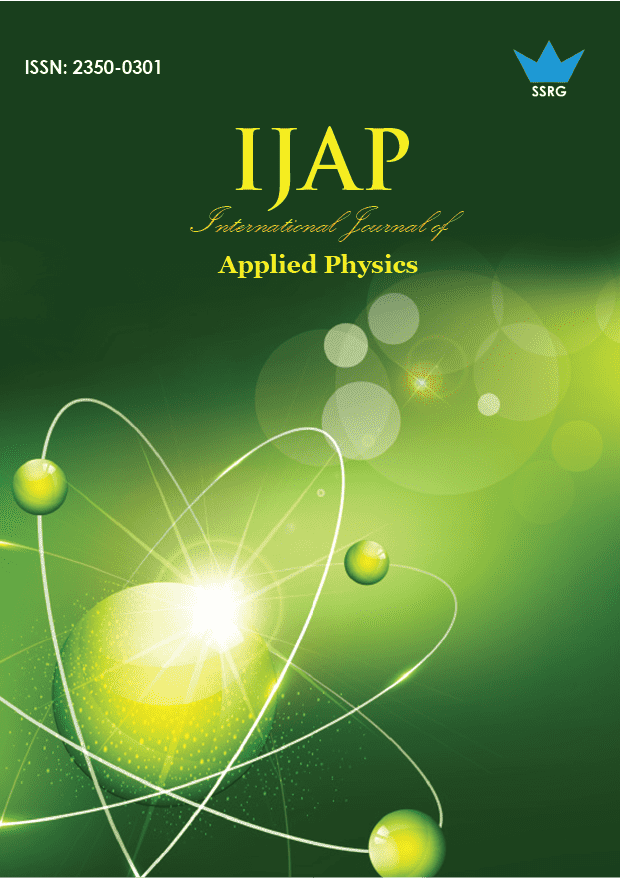
International Journal of Applied Physics |
© 2020 by SSRG - IJAP Journal |
Volume 7 Issue 2 |
Year of Publication : 2020 |
Authors : Nikolai I. Kobasko |
How to Cite?
Nikolai I. Kobasko, "Hardening of Low and Optimal Hardenability Steels and their Physical Processes Explanation," SSRG International Journal of Applied Physics, vol. 7, no. 2, pp. 20-31, 2020. Crossref, https://doi.org/10.14445/23500301/IJAP-V7I2P104
Abstract:
The main idea of this paper is the possibility of cardinal improving quenching technologies, reduce their cost, increase service life of machine components and tools and make technology green based on accurate investigations of the behavior a liquid coolant during hardening in it heated to high temperature metal. It is shown in the paper that recently discovered new features of transient nucleate boiling process allow designing new technologies for optimal hardenability steels comprising mentioned above characteristics. It is underlined in the paper that many already existing
grades of steels can serve as low hardenability (LH) steel for large steel parts to provide similar stress distribution after quenching (high surface compression residual stresses and low tensile stresses at the core). Moreover, it is proposed by author a new criterion for designing quenching processes for low hardenability and optimal hardenability steels that always provide surface compression residual stresses. Along with mentioned above, the paper continues discussion the possibility of performing intensive quenching (IQ) processes in slow agitated water and water solutions.
This fact cardinally reduces the cost of technological process and makes it as a mass production technology to be used worldwidly. It is shown in the paper that without investigation of physics of quench process, it is impossible to design appropriate software for governing and controlling of quenching processes. All provided information can be useful for investigators, scientists and engineers.
Keywords:
Physics of quench process; LH and OH steels; Hardenability criterion; Mass production; Power density; Low cost.
References:
[1] Kern Roy F., (1986). “Intense quenching”, Heat Treating, No. 9, pp. 19 -23.
[2] Russian Patent No. 2158320, “Construction Steel of Low Hardenability”, Application No. 99125102, Filed on Nov. 29, 1999.
[3] Bogatyrev, Yu.M., Shepelyakovskii, K. Z., Shklyarov, I.N., (1967). “Cooling rate edffect on crack formation during steel quenching”, MiTOM, No. 4, pp. 15 – 22.
[4] Natanzon E.I., (1976). Temianko L.S., (1976). “Simultaneous quenching of truck semi – axles”, Avtomobilnaya Promyshlennost, No. 10, pp. 33 – 35.
[5] Shepelyakovskii, K. Z. (1972). “Strengthening of Machine Components by Induction Surface Hardening”. Moscow: Mashinostroenie, 288.
[6] Kobasko, N.I., (1980). “Steel quenching in liquid media underf pressure”, Naukova Dumka, Kiev, 206 p.
[7] Shepelyakovskii, K. Z., Ushakov, B. K. (1990, December). “Induction surface hardening-progressive technology of XX and XXI centuries”. In Proc. 7th Int. Congress on Heat treatment and technology of surface coatings, 33–40.
[8] Ukrainian Patent UA 114174, C2, “Alloyed Low Hardenability Steel and Method of its Composing”, Filed on Sep.23, 2013, File number: a 2013 11311.
[9] Kobasko N., (2018). “Optimal Hardenability Steel and Method for Its Composing.” Lambert Academic Publishing, Germany,122 p. IBSN-13: 978-613-9-82531-8.
[10] Kobasko N., (2019). “High Quality Steel vs Surface Insulating Layer Formed during Quenching”. Lambert Academic Publishing, Germany, 108 p.
[11] Kobasko N., (2017). “A method for optimizing chemical composition of steels to reduce radically their alloy elements and increase service life of machine components”. EUREKA: Physics and Engineering. Number 1, pp. 3 – 12. DOI: 10.21303/2461-4262.2016.00253
[12] Kobasko N.I., (2019). “Uniform and Intense Cooling During Hardening Steel in Low Concentration of Water Polymer Solutions”, American Journal of Modern Physics, Vol. 8, Issue 6, pp. 76-85. DOI: 10.11648/j.ajmp.20190806.11.
[13] Kobasko N.I., (2020). “Mechanism of film elimination when intensively quenching steel parts in water polymer solutions of low concentration”, Global Journal of Science Frontier Research – A: Physics and Space Science, Vol. 20, Issue 7, pp. 39 – 56.
[14] Kobasko N.I., (2019). “Austempering Processes That are Performed via Cold Liquids”, Lambert Academic Publishing, Germany, 116 p., DOI: 10.1520/mnl64-eb, ISBN: 978-620-0-11330-6.
[15] Kobasko N.I., (2019). “Transient Nucleate boiling as a Basis for Designing Austempering and Martempering New Technologies”, SSRG International Journal of Applied Physics (SSRG-IJAP), Vol. 6, Issue 2.
[16] Kobasko N.I., Aronov M.A., Powell J.A., Totten G.E., (2010). “Intensive Quenching Systems: Engineering and Design”. ASTM International, USA, 234 p. doi: 10.1520/mnl64-eb.
[17] Kobasko, N. I. (2009). “Transient Nucleate Boiling as a Law of Nature and a Basis for Designing of IQ Technologies”. Proceedings of the 7th IASME/WSEAS International Conference on Heat Transfer, Thermal Engineering and Environment (HTE ‘09), Moscow, 2009, August 20–22, 67–
76.
[18] Kobasko, N. I., and Morhuniuk, W. S., (1983). Issledovanie teplovogo i napriazhenno-deformirovannogo sostoyaniya pri termicheskoy obrabotke izdeliy mashinostroeniya (Study of thermal and stress-strain state at heat treatment of machine parts), Znanie, Kyiv.
[19] Kobasko, N. I., and W. S. Morhuniuk, (1985). “Numerical Study of Phase Changes, Current and Residual Stresses at Quenching Parts of Complex Configuration”, Proceedings of the 4th International Congress of Heat Treatment Materials, Berlin, Vol. 1, pp. 465–486.
[20] Kobasko, N.I., Morhuniuk, W.S., Ushakov, B.K., (2006). “Design of Steel – Intensive Quench Processes”. Steel Heat Treatment Handbook (Second Edition), George E. Totten (Ed.), CRC Press, Boca Raton – London – New York, pp. 193 – 217. ISBN – 13: 978-0-8493-8454-7.
[21] Kobasko, N.I., Morganiuk, V.S., Morganiuk, A.P., (1990). “Hardening of complex configuaration samples by intensive cooling”, Proc. of the 7th International Congress on Heat Treatment of Materials, Dec. 11 -14, Moscow, Vol. 2, pp. 232 – 239..
[22] Dowling, W., T. Pattok, B. L. Ferguson, D. Shick, Y. Gu, and M. Howes, “Development of a Carburizing and Quenching Simulation Tool,” The 2nd International Conference on Quenching and Control of Distortion, ASM International, Cleveland, OH, 1996.
[23] Ferguson, B. L., A. M. Freborg, G. J. Petrus, and M. L. Collabresi, “Predicting the Heat Treat Response of a Carburized Helical Gear,” Gear Technology, 2002, pp. 20–25.
[24] Grossmann, M. A. (1964). “Principles of Heat Treatment.” Ohio: American Society for Metals, 302.
[25] Totten, G. E., Bates, C.E., and Clinton ,M.A., , (1993). “Handbook of Quenchants and Quenching Technology”, ASM International, Materials Park, OH, USA.
[26] Kondrat’ev, G.M., (1957). Teplovye Izmereniya (Thermal Measurements). Moscow: Mashgiz, 1957.
[27] Kobasko, N.I., Moskalenko, A.A., Logvynenko, P.N, Dobryvechir, V.V., (2019). “New direction in liquid quenching media development”, Teplofizyka ta Teploenerhetyka (in Ukr), Vol. 41, No.3, pp. 33 -40. https:doi.org/10.31472/ttpe.3.2019.5.
[28] Кадинова А.С., Хейфец Г.Н., Тайц Н.Ю., (1963).. О характере теплообмена при струйном охлаждении, ИФЖ., 6, № 4, сс. 46 – 50.
[29] Kobasko N., Guseynov Sh., Rimshans J., (2019). “Core Hardness and Microstructure Prediction in Any Steel Part. Lambert Academic Publishing”, Germany, 104 p. IBSN-13: 978-613-9-94751-5
[30] Kobasko, N.I., (1992). “Intensive Steel Quenching Methods, A Handbook “Theory and Technology of Quenching’”, B.Liscic, H.M. Tensi, W.Luty (Eds.), Springer- Verlag, Berlin, pp. 367 – 389.
[31] Ferguson, B.L., (2013). “Applying DANTE Heat Treat Modeling to Intensive Quenching,” Presentation at the Intensive Quenching Workshop held on April 24 in Cleveland, Ohio, USA.
[32] Kobasko, N. I. (2005). “Quench Process Optimization for Receiving Super Strong Materials.” Proceedings of the 5th WSEAS Int. Conference on simulation, modeling and optimization, 365–372.
[33] Kobasko Nikolai., (2017). “A method for optimizing chemical composition of steels to reduce radically their alloy elements and increase service life of machine components.” EUREKA: Physics and Engineering. Number 1, pp. 3-12. DOI: 10.21303/2461-4262.2016.00253 .
[34] Bhadeshia, H.K.D.H., (2015). “Bainite in Steels: Theory and Practice” (3rd Edition), Money Publishing, 616 p.
[35] Kobasko, N. I. (2005). “The main principles of intensive quenching of tools and dies”, Proc. of the 1th International Conference on Heat Treatment and Surface Engineering of Tools and Dies, 39–44.
[36] Powell J.A., (2017). “Everything Matters to Reach ASM HTS’s Vision 2020 Goals” , ASM Heat Treating Society Conference Paper, Presented in Columbus, Ohio, October 24, 11 p.