Maintenance Modularity Optimization using Clustering Algorithm: Application
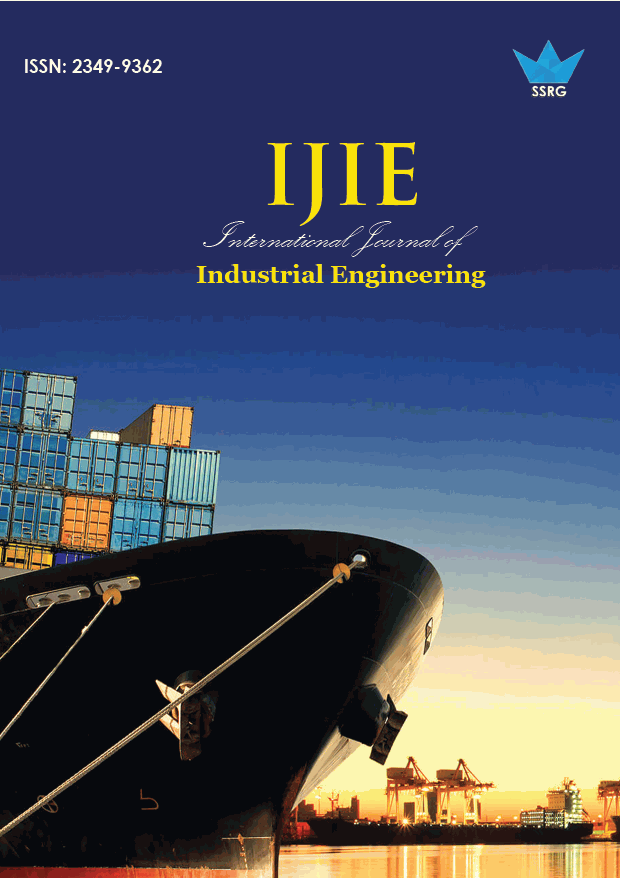
International Journal of Industrial Engineering |
© 2020 by SSRG - IJIE Journal |
Volume 7 Issue 1 |
Year of Publication : 2020 |
Authors : Ngnassi Djami Aslain Brisco, Nzié Wolfgang, DokaYamigno Serge |
How to Cite?
Ngnassi Djami Aslain Brisco, Nzié Wolfgang, DokaYamigno Serge, "Maintenance Modularity Optimization using Clustering Algorithm: Application," SSRG International Journal of Industrial Engineering, vol. 7, no. 1, pp. 12-24, 2020. Crossref, https://doi.org/10.14445/23499362/IJIE-V7I1P102
Abstract:
For a given product, knowledge of its modular architecture has the advantage of facilitating maintenance. Indeed, during a maintenance problem,
we will not act on all the product except on the module concerned and we would also gain time to detect the defect observed. Due to the major difficulties of maintenance of complex topology systems, modular design is therefore an asset for companies.On the other hand, the modular design
although with the advantages of standardization and reconfigurability is enormously expensive, which could require more resources, more time and more work designers. This has consequences for product maintenance because the more robust or dense product modules, the more expensive the
maintenance. This paper will therefore be used to deploy a clustering algorithm that will be subdivided into several steps in order to evaluate the coupling cost of the product modules in order to identify the most constraining modules for the design and consequently for maintenance.
Keywords:
Maintenance, Modularity, Clustering, Design Structure Matrix, Module Strength Indicator.
References:
[1] H. Ghassen, “Towards a joint conception of the architectures of the product and the organization of the project within the framework of the System Engineering “, Ph.D. thesis, University of Franche-Comté, UFR Sciences and Techniques, Doctoral School Physical Sciences for the Engineer and Microtechniques, 249 pages, 2007.
[2] A. Ericsson and G. Erixon, “Controlling design variants: Modular product platforms “, (p. pp145). New York: ASME press, 1999.
[3] A. Bourjault, State Thesis, “Contribution of a methodological approach to automated assembly: automatic development of operating sequences “, University of Franche-Comté, 1984.
[4] A. K. Subramani, and P. Dewhurst, “Automatic Generation of Product Disassembly Sequences “, CIRP Annals- Manufacturing Tehnology, 40 (1), 115-118, 1991.
[5] Y. Lee, and S. Kumana,” Individual and group disassembly sequence generation through freedom and interference spaces”, Journal of Design and Manufacturing, 2, 143-154, 1992.
[6] H. Srinivasan, and R. Gadh, “A geometric algorithm for single selective disassembly using wave propagation abstraction “, Computer-Aided Design, 30 (8), 603-613, 1998.
[7] T. Jabbour and C. Mascle, A Database for the representation of assembly features in mechanical products, International Journal of Computational Geometry & Applications, 8 (5-6), 1998.
[8] T. Kuo, H. C. Zhang, and S. Huang,” Disassembly analysis for electromechanical products: a graph-based heuristic approach”, International Journal of Production Research, 38 (5), 993-1007, 2000.
[9] H. Srinivasan and R. Gadh, “Efficient geometric disassembly of multiple components from an assembly using wave propagation “, Journal of Mechanical Design, 122 (2), 179-184, 2000.
[10] A. Gungor and S. Gupta, “Disassembly sequence plan generation using a branch-and-bound algorithm “, International Journal of Production Research, 39 (3), 481-509, 2001.
[11] E. Moore, A. Gungor, and S. Gupta,” Petri net approach to disassembly process planning for products with complex AND/OR precedence relationships”, European Journal of Operational Research, 135 (2), 428-449, 2001.
[12] E. Kongar and S. Gupta,” Genetic algorithm for disassembly process planning”, in Proceedings of the SPIE International Conference on Environmentally Conscious Manufacturing II (pp. 54-62). Newton, Massachusetts, 2001.
[13] F. Failli and G. Dini, “Optimization of disassembly sequences for recycling of end-of-life products by using a colony of ant-like agents “, Engineering of Intelligent Systems, 2070, 632-639, 2001.
[14] H. Srinivasan, and R. Gadh, A non-interfering selective disassembly sequence for components with geometric constraints, IIE Transactions, 34, 349-361, 2002.
[15] F. Torres, S. T. Puente, and R. Aracil, Disassembly Planning Based on Precedence Relations among Assemblies, International Journal Advanced Manufacturing Technology, 21 (5), 317-327, 2003.
[16] J. F. Wang, J. H. Liu, S. Li, Y. F. Zhong, “Intelligent selective disassembly using the ant colony algorithm “, Artificial Intelligence for Engineering Design, Analysis and Manufacturing: AIEDAM, 17 (4-5), 325-333, 2003.
[17] A. Lambert, and S. Gupta,” Disassembly modelling for assembly, maintenance, reuse, and recycling (éd. CRC Press)”, 2005.
[18] E. Kongar, and S. Gupta,” Disassembly sequencing using genetic algorithm, International Journal Advanced Manufacturing Technology”, 30 (5-6), 497-506, 2006.
[19] F. Giudice and G. Fargione, “Disassembly planning of mechanical systems for service and recovery: A genetic algorithm based approach “, Journal of Intelligent Manufacturing, 18 (3), 313-329, 2007.
[20] Y. Tseng, H.T. Kao, and F.Y, Huang, “Integrated assembly and disassembly sequence planning using a GA approach “, International Journal of Production Research, 48 (20), 1-23, 2009.
[21] M. Tripathi, S. Agrawal, M. Pandeyc, Shankar, and M. T iwari, “Real world disassembly modeling and sequencing problem: Optimization by Algorithm of Self-Guided Ants (ASGA) “, Robotics and Computer-Integrated Manufacturing, 25 (3), 483-496, 2009.
[22] X. Zhang, and S. Y. Zhang, “Product cooperative disassembly sequence planning based on branch-and-bound algorithm “, International Journal Advanced Manufacturing Technology, 51 (9-12), 1139-1147, 2010.
[23] J. Xue, S. Qian, and Y. Zhang, “Disassembly sequence planning based on ant colony optimization algorithm “, IEEE Fifth International Conference on Bio-Inspired Computing: Theories and Applications, 1125-1129, 2010.
[24] P. J. Newcomb, B. Bras, and D. W. Rosen, “Implications of modularity on product design for the life cycle”, Journal of Mechanical Design, Volume 120, 1998, pp. 483-490.
[25] M. Blackenfelt, “Modularization by Relational Matrices - a Method for the Consideration of Strategic and Functional Aspects”, Proceedings of the 5th WDK Workshop on Product Structuring. January 2000, Edt. Riithahuhta A., Pulkkinen A., Springer- Verlag
[26] F. Guo, and J. K. Gershenson, “A comparison of modular product design methods on improvement and iteration”, In Proc of ASME Design Engineering Technical Conferences., Salt Lake City, UT. 2004.
[27] K. Hölttä, E. Suh, and De O. Weck, “Tradeoff Between Modularity and Performance for Engineering Systems and Products”,
International Conference On Engineering Design Iced 05 Melbourne, August 15 – 18, 2005.
[28] R.I. Whitfield, J.S. Smith, and A.H.B. Duffy, “Identifying Component Modules “, In Proceedings of Seventh International Conference on Artificial Intelligence in Design (AID’02), Cambridge, United Kingdom, pp. 571-592, 2002
[29] B. Eric, “Contributions to the instrumentation of the architectonic system: from the modular architecture of the product to the organization of the design system “, Habilitation to Direct Research, Université de Franche-Comté, Faculty of Science and Technology, FEMTO-ST Institute / Department AS2M .206 pages, 2008.
[30] J. Idicula,” Planning for Concurrent Engineering”, Thesis draft, Nanyang Technology University, Mars, 1995.