Analysis on Four Stroke Single Cylinder Engine Piston by using Aluminum Alloys (Al-GHS 1300, Al-Sic- Graphite, A6061, Pure Aluminum)
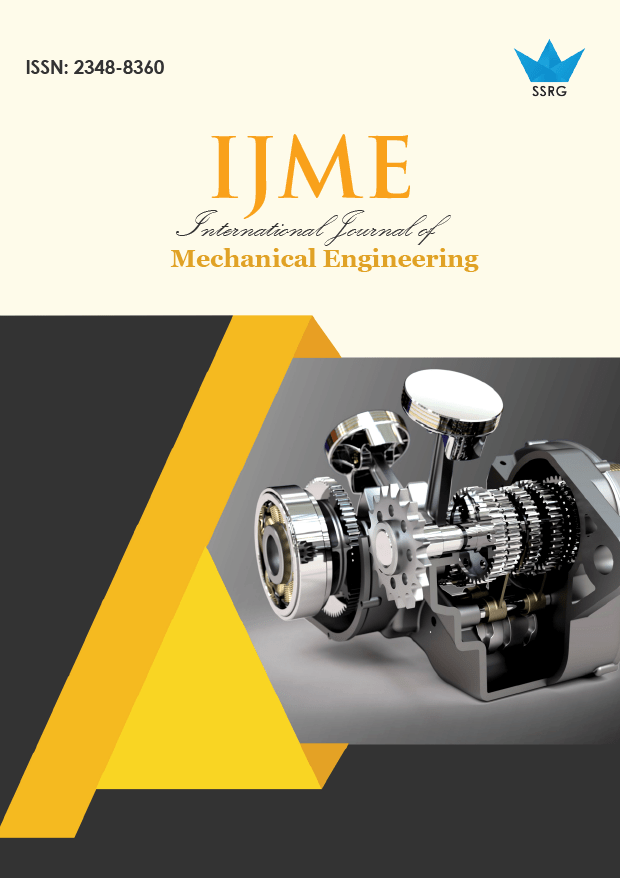
International Journal of Mechanical Engineering |
© 2016 by SSRG - IJME Journal |
Volume 3 Issue 1 |
Year of Publication : 2016 |
Authors : Tadala akhil, K.Naresh, Abdul khurshid, Purushotham anil kumar |
How to Cite?
Tadala akhil, K.Naresh, Abdul khurshid, Purushotham anil kumar, "Analysis on Four Stroke Single Cylinder Engine Piston by using Aluminum Alloys (Al-GHS 1300, Al-Sic- Graphite, A6061, Pure Aluminum)," SSRG International Journal of Mechanical Engineering, vol. 3, no. 1, pp. 4-11, 2016. Crossref, https://doi.org/10.14445/23488360/IJME-V3I1P102
Abstract:
This paper describes the thermal and the stress distribution of the piston which is initialized with four different materials by using the COUPLED field analysis by finite element method (FEM). The parameters used for the simulation are the temperature as thermal conditional and the force or the pressure applying on the piston crown and the material properties of the piston. The specifications used for the piston belong to four stroke single cylinder Hero-Honda motorcycle. Aluminum metal composites are increasing across the broad acknowledgement for vehicles, modern, aviation applications in view of their low thickness, high quality and great structural unbending nature. In present work the Piston is modeled using CATIA V5 modeling and Finite Element analysis (COUPLE FIELD analysis) by using the modules of both structural and thermal analysis are done for same model utilizing ANSYS software for Aluminum (pure) , Aluminum alloy (A6061), Al-GHS 1300 and Al-SiCgraphite and the results were discussed. The results predict the maximum stress and the critical region on the different aluminum alloys piston using FEA. It is important to locate the critical area of concentrated stress for appropriate modifications.
Keywords:
Aluminum (pure), Silicon Carbide, A6061 and Graphite, Al-GHS 1300, Coupled field analysis, Piston, Von-Mises stresses
References:
[1] E. Ramjee and K. Vijaya Kumar Reddy, “Performance analysis of a 4-stroke SI engine using CNG as an alternative fuel”, Indian Journal of Science and Technology, Vol. 4, No. 7, July 2011.
[2] Wilfried Wunderlich and Morihito Hayashi, “Thermal cyclic fatigue analysis of three aluminium piston alloys”, International Journal of Material and Mechanical Engineering, June 2012.
[3] Dallwoo Kim, Akemi Ito et.al., “Friction characteristics of steel pistons for diesel engines”, Journal of Materials Research and Technology, June 2012.
[4] Piotr Szurgott and Tadeusz Niezgoda, “Thermo mechanical FE analysis of the engine piston made of composite material with low hysteresis” Journal of KONES Powertrain and Transport, Vol. 18, No. 1, 2011.
[5] V. B. Bhandari, “Design of Machine Elements”, 3rd Edition, McGraw Hill.
[6] Technical Data, Advanced Materials Technology, Bickenbach, Germany, DB- AMT@web.de.
[7] F. S. Silva, “ Fatigue on engine pistons – A Compendium of case studies”, Department of Mechanical Engineering, University of Minho, Portugal, Engineering Failure Analysis 13 (2006) 480– 492.
[8] Shigley, Mechanical Engineering Design, 9th edition, McGraw-Hill.
[9] P. S. Shenoy and A. Fatemi, “ Dynamic Analysis of Loads and Stresses in Connecting Rods”, Journal of Mechanical Engineering Science, 2006, Vol. 220, No. 5.
[10] P. S. Shenoy and A. Fatemi, “ Connecting Rod Optimization for Weight and Cost Reduction”, SAE Paper No. 2005-01-0987, SAE 2005 Transactions: Journal of Materials and Manufacturing.
[11] P. Gudimetal P. and C. V. Gopinath, “ Finite Element Analysis of Reverse Engineered Internal Combustion Engine Piston”,© King Mongkut’s University of Technology,Bangkok, Thailand, AIJSTPME, 2009.