Enlargement of an Intellectual and Energy Proficient Spindle System
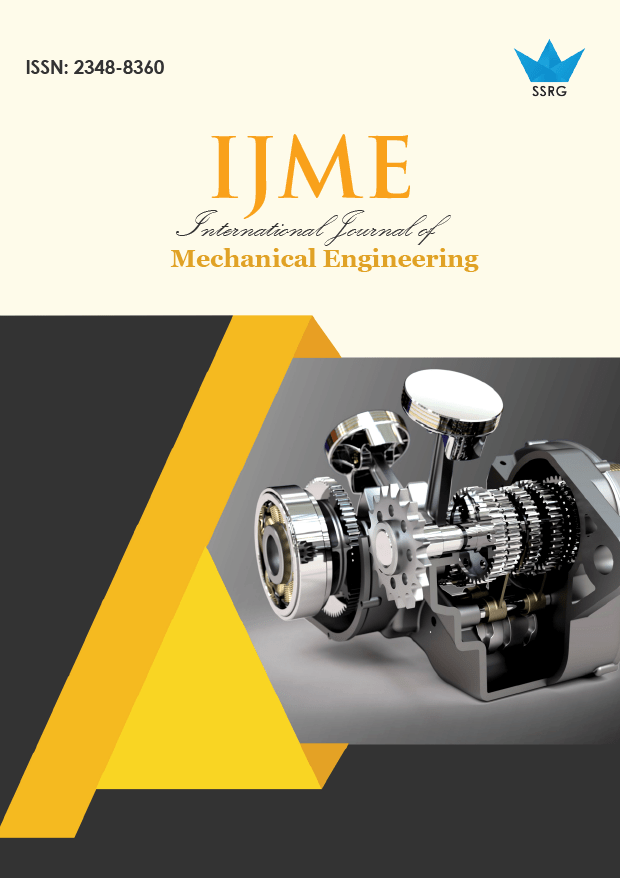
International Journal of Mechanical Engineering |
© 2016 by SSRG - IJME Journal |
Volume 3 Issue 12 |
Year of Publication : 2016 |
Authors : B.Sunaina Sharma |
How to Cite?
B.Sunaina Sharma, "Enlargement of an Intellectual and Energy Proficient Spindle System," SSRG International Journal of Mechanical Engineering, vol. 3, no. 12, pp. 5-9, 2016. Crossref, https://doi.org/10.14445/23488360/IJME-V3I12P103
Abstract:
Spindle scheme plays a very significant responsibility in CNC and milling machines; but the foremost inconvenience over these machines is - they disperse lots of energy which affects the generally effectiveness and accurateness of the process. On identifying the a variety of cause for the energy rakishness - major factors like inappropriate speed control and imperfections in intend may cause pulsation and thermal inactivity that may impart a great quantity of disturbance in the organization. This paper importance on a framework in the improvement of a smart spindle scheme innate with cutting border Mechatronics system that aims for its intellectual and dynamic organize. The projected system is prepared with sensory feedback to appreciate the environmental variations and spindling processes it also has an on-board manage system, clever enough to control the machining development successfully and resourcefully.
Keywords:
Spindle System, Energy Efficiency, Sensors Fusion, Intelligent Control
References:
1. Narrendar.R.C, Indira Kumar.S, Tilak, Development of an Intelligent and Energy Efficient Spindle System, International Journal of Advanced Research in Electrical, Electronics and Instrumentation Engineering, Vol. 3, Issue 11, November 2014.
2. Schuyler, C.K., “Federate Optimization and Tool Condition Monitoring of Flat End Milling Operations Utilizing Spindle Motor Power”, M.S. Thesis, UNH ME Department, 2005.
3. Xu, M., C.K. Schuyler, B.K. Fussell, R.B. Jerard, “Experimental Evaluation Of A Smart Machining System For Federate Selection And Tool Condition Monitoring,” Transactions of the North American Manufacturing Research Institution/SME Volume 34, NAMRC 34, Marquette University, 2006.
4. Jerard, R B. , Barry K. Fussell, Min Xu, Chad Schuyler, Donald Esterling, “Development of a Tested for Research on Smart Machine Tools, ”, Proceedings of 2006 NSF DMII Grantees Conference, St. Louis, July 24-27, 2006.
5. Atsushi Matsubara, Motoyuki Sugihara, Ahmed A.D.Sarhan., “ Research on spindle and machining process monitoring for intelligent machine tools”, International conference on Leading Edge manufacturing in 21st century, Nagoya-Japan. Oct, 2005.
6. Moon Jong Duk, Kim Bong-Suk, Lee Soo-Hun,” Development of the Active Balancing Device for High-Speed Spindle System Using Influence Coefficients” International Journal of Machine Tools and Manufacture, 46 (9): 978- 987,2006.
7. Chi-Wei Lin, Jay F. Tu, Joe Kamman, “An integrated thermo-mechanical-dynamic model to characterize motorized machine tool spindles during very high speed rotation”, International Journal of Machine Tools and Manufacture, Volume 43, Issue 10, Pages 1035–1050, Aug 2003.
8. M.Kaever, N.Brouer, M.Rehse and M.Weck, “NC integrated process monitoring and control for intelligent autonomous manufacturing systems”, 29th CIRP International seminar on manufacturing system, Osaka, 1997.