Optimization of Process Parameters for Milling of Nickel Alloy Inconel 625 by Using Taguchi Method
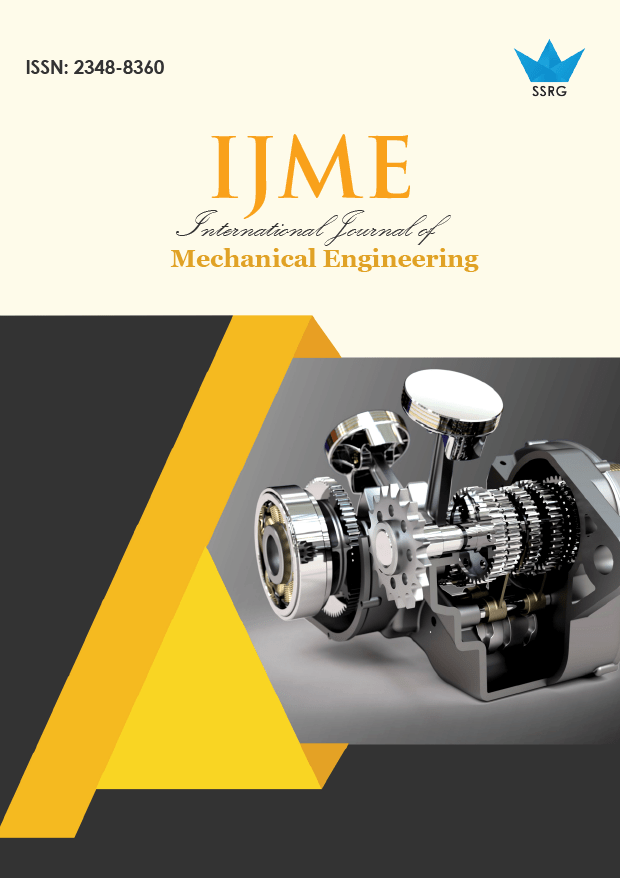
International Journal of Mechanical Engineering |
© 2015 by SSRG - IJME Journal |
Volume 2 Issue 2 |
Year of Publication : 2015 |
Authors : Pulavarthi raviteja, S. Raja Sekhar |
How to Cite?
Pulavarthi raviteja, S. Raja Sekhar, "Optimization of Process Parameters for Milling of Nickel Alloy Inconel 625 by Using Taguchi Method," SSRG International Journal of Mechanical Engineering, vol. 2, no. 2, pp. 15-21, 2015. Crossref, https://doi.org/10.14445/23488360/IJME-V2I2P104
Abstract:
Metal cutting is one of the most significant manufacturing processes in the area of material removal. Black defined metal cutting as the removal of metal chips from a work piece in order to obtain a finished product with desired attributes of size, shape, and surface roughness. The imperative objective of the science of metal cutting is the solution of practical problems associated with the efficient and precise removal of metal from work piece. It has been recognized that the reliable quantitative predictions of the various technological performance measures, preferably in the form of equations, are essential to develop optimization strategies for selecting cutting conditions in process planning. In this thesis experiments will be conducted to improve the surface finish quality of a nickel alloy Inconel 625 work piece by using carbide tips. The type is bull nose tip. A series of experiments will be done by varying the milling parameters spindle speed, feed rate and depth of cut. The spindle speeds are 3000rpm, 2500rpm and 2000rpm. The feed rates are 200mm/min, 300mm/min and 400mm/min. Depth of cut is 0.2mm and 0.3mm. Structural analysis will be also done to verify the strength. Modeling will be done in Pro/Engineer and analysis will be done in Ansys. Taguchi method is used to study the effect of process parameters and establish correlation among the cutting speed, feed and depth of cut with respect to the major machinability factor, surface finish. Validations of the modeled equations are proved to be well within the agreement with the experimental data.
Keywords:
spindle speed, feed rate and depth of cut
References:
[1] Modeling of the Influence of Cutting Parameters on the Surface Roughness, Tool Wear and Cutting Force in Face Milling in Off-Line Process Control by Dražen Bajić, Luka Celent, Sonja Jozić, University of Split, Faculty of Electrical Engineering, Mechanical Engineering and Naval Architecture, Croatia
[2] Optimization of surface roughness in face turning operation in machining of EN-8 by K. Adarsh Kumar, Ch.Ratnam, BSN Murthy, B.Satish Ben, K. Raghu Ram Mohan Reddy
[3] Effect of machining conditions on MRR and surface roughness during CNC Turning of different Materials Using TiN Coated Cutting Tools – A Taguchi approach by H. K. Dave, L. S. Patel, H. K. Raval
[4] Optimization of surface roughness in CNC end milling using response surface methodology and genetic algorithm by B. Sidda Reddy, J. Suresh Kumar, and K. Vijaya Kumar Reddy
[5] Prediction of surface roughness in end milling with gene expression programming by Yang Yang, Xinyu Li, Ping Jiang, Liping Zhang
[6] Furness, R.J., Ulsoy, A.G., Wu, C.L. (1996). Feed, speed, and torque controllers for drilling. ASME Journal for Manufacturing Scientists and Engineers, vol. 118, p. 2–9.
[7] Landers, R.G., Usloy, A.G., Furness, R.J. (2002). Process monitoring and control of machining operations. Mechanical Systems Design Handbook. CRC Press LLC, p. 85-119.
[8] Lu, C. (2008). Study on prediction of surface quality in machining process. Journal of Materials Processing Technology, vol. 205, no. 1-3, p. 439-450, DOI:10.1016/j.jmatprotec.2007.11.270.
[9] Bajić, D., Belaić, A. (2006). Mathematical modelling of surface roughness in milling process. Proceedings of the 1st International Scientific Conference on Production Engineering (ISC), p. 109-115.
[10] Oktem, H., Erzurumlu, T., Kurtaran, H. (2005). Application of response surface methodology in the optimization of cutting conditions for surface roughness. Journal of Materials Processing Technology, vol. 170, p. 11-16, OI:10.1016/j.jmatprotec.2005.04.096.