Finite Element Analysis and Material Optimization for Equivalent Strength of Composite Connecting Rod
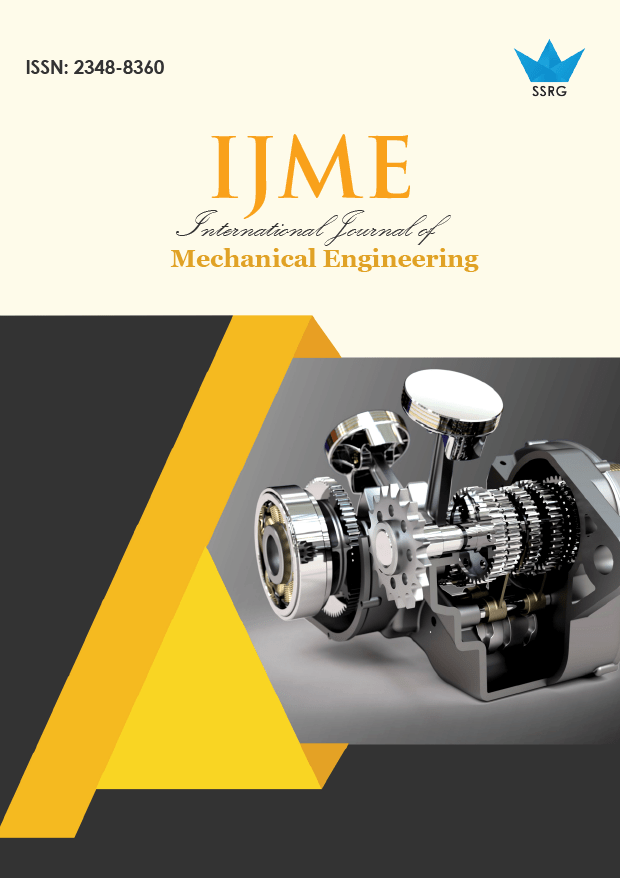
International Journal of Mechanical Engineering |
© 2015 by SSRG - IJME Journal |
Volume 2 Issue 2 |
Year of Publication : 2015 |
Authors : Mr. Vivek T. Fegade, Dr. Kiran S. Bhole |
How to Cite?
Mr. Vivek T. Fegade, Dr. Kiran S. Bhole, "Finite Element Analysis and Material Optimization for Equivalent Strength of Composite Connecting Rod," SSRG International Journal of Mechanical Engineering, vol. 2, no. 2, pp. 27-33, 2015. Crossref, https://doi.org/10.14445/23488360/IJME-V2I2P106
Abstract:
This work describes about weight reduction opportunities for forged steel connecting rod of internal combustion engine. The existing connecting rod is modified to make it composite connecting rod using two materials: forged steel and titanium without disturbing its existing geometry. The design and weight affects the performance of connecting rod. With the implementation of optimization approach connecting rod of stronger but equally lighter can be obtained with minimum cost. Therefore, this study has dealt with two subjects, first, static load with detailed stress analysis of the connecting rod and second optimization of rod to reduce the weight and production cost. A appropriate CAD model of connecting rod was designed in CATIA V5, after that FEA was carried out in ANSYS WORKBENCH to determine maximum vonmisses stresses acting on it. In response to an increasing demand for fuel-economy, weight reduction technique have been proposed to create an optimum connecting rod design. The research aims to maximize weight savings in a connecting rod, without sacrificing the structural performances such as strength and stiffness.
Keywords:
Connecting Rod, FEA, Optimization, Static
References:
[1] M. SC. Anna Ulatowska, (2008) “Shape Optimization of the Connecting Rod”
[2] Pravardhan S. Shenoy and Ali Fatemi, (2005), “Connecting Rod Optimization for Weight and Cost Reduction”,The University of Toledo, SAE Interantional.
[3] Augugliaro G.a, Biancolini M.E.,(2003) “Optimization of fatigue performance of a Titanium Connecting Rod, SAE technical paper 980800, 1-3.
[4] Moon Kyu Lee, Hyungyil Lee,Tae Soo Lee, Hoon Jang, (2010) “Buckling Sensitivity of a Connecting Rod to the Shank sectional area Reduction” Journal of Materials and Design, 31, pp. 2796–2803.
[5] Tony George Thomas, S. Srikari, M. L. J Suman, (2010) “Design of connecting rod for heavy duty applications produced by different processes for enhanced Fatigue Life” SASTECH Journal Vol. 10, Issue 1.
[6] Zhixue Wu, (2005) “An efficient approach for Shape Optimization of components”, International Journal of Mechanical ciences 47 pp. 1595–1610.
[7] Xianjun Hou, Cuicui Tian, Dan Fang, Fuming Peng and Fuwu Yan,(2009) “Sensitivity Analysis and Optimization for Connecting Rod of LJ276M Electronic Gasoline Engine”, IEEE, 978-1-4244-4507-3
[8] Zheng Bin Liu Yongqi, Ji Lixia, (2010) “Finite Element Analysis and Structural Improvement of Diesel Engine Connecting Rod”, Second International Conference on Computer Modeling and Simulation.
[9] M.S. Shaari, M.M. Rahman, M.M. Noor, K. Kadirgama, A.K. Amirruddin, (2010) “Design of Connecting rod of Internal Combustion Engine: A Topology Approach” National Conference in Mechanical Engineering Research and Postgraduate Studies pp. 155-166.
[10] Ahamad Ridzuan Bin Ibrahim, (2010), “Analysis of Connecting Rod fracture using Finite Element Analysis”, Bachelor Thesis, University of Malaysia.
[11] Ed.Platt, (1922), “Design of connecting rods for High speed Engines”, Dailmer premium paper session.
[12] Dongkai Jia, Ke Wu, Shi Wu, Yuntong Jia, Chao Liang, (2011) “The Structural analysis and Optimization of Diesel Engine Connecting Rod” International Conference on Electronic & Mechanical Engineering and Information Technology, IEEE, pp. 3289-3292
[13] Pravardhan S. Shenoy, 2004, “Dynamic Load Analysis and Optimization of Connecting Rod”, Master’s Thesis, University of Toledo.
[14] Asadi, M.R., Rasekh M., Golmohammadi A., Jafari A., Kheiralipour, K., Borghei A.M., (2010) “Optimization of Connecting rod of MF-285 tractor” Journal of Agricultural Technology, Vol. 6(4), pp. 649-662.
[15] P. Brabec, P. Kefurt, C. Scholz, R. Vozenilek, “FEM Analysis of Connecting Rod for Stationary Engine” Josef Bozek Research Centre for Engine and Vehicle Technologies II
[16] B. Lawton, D. E. G. Crutcher, (1967) “Mechanical Stresses in Pistons, Gudegeon pins, and Connecting Rod” Proceedings of Institution Mechanical Engineers, Volume 181
[17] Rabb R, (1996) “Fatigue failure of a connecting rod,” Engineering Failure Analysis, Vol.3, No. 1, pp. 13-28.
[18] Zhou Qinghui, Wang Yunying, Ji Wei, (2010) “The Finite Element Analysis of Connecting Rod of Diesel Engine” International Conference on Measuring Technology and Mechatronics Automation, IEEE, pp. 870-873
[19] Yunliang Ding, (1986) “Shape Optimization of Structures: A Literature Survey” computer and Structures Vol. 24. No. 6. pp. 985-1004.
[20] Zhixue Wu, (2005) ,“An efficient approach for Shape Optimization of components”, International Journal of Mechanical Sciences 47 pp. 1595–1610
[21] Xiao Lei Xu, Zhi Wei Yu, (2007) “Failure Analysis of a Diesel Engine Connecting Rod” Journal of Failure Analysis and Prevention”, Vol. 7, pp. 316–320.
[22] Adila Afzal and Ali Fatemi, (2004) “A Comparative Study of Fatigue Behavior and Life Predictions of Forged Steel and PM Connecting Rods” The University of Toledo, SAE International.
[23] Mirehei, M. Hedayati Zadeh, A. Jafari, M. Omid, (2008), “Fatigue analysis of Connecting Rod of Universal Tractor through Finite Element Method” Journal of Agricultural Technology, Vol. 4, pp. 21-27.