Improving Machining Performance of ECM by Different Tool Geometry
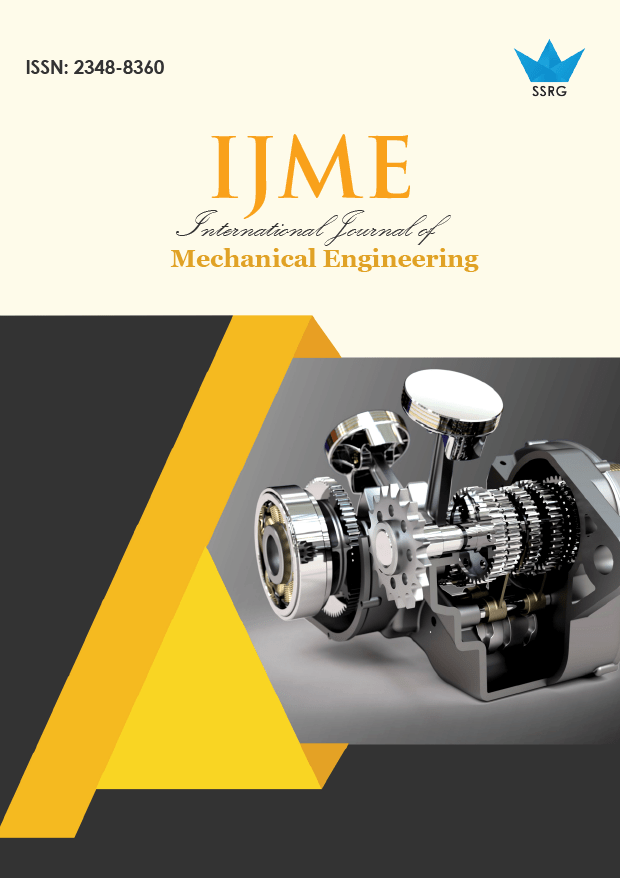
International Journal of Mechanical Engineering |
© 2020 by SSRG - IJME Journal |
Volume 7 Issue 6 |
Year of Publication : 2020 |
Authors : G.Arulmurugan, R.Bharath, P.Raja, R.Rajeshkannan |
How to Cite?
G.Arulmurugan, R.Bharath, P.Raja, R.Rajeshkannan, "Improving Machining Performance of ECM by Different Tool Geometry," SSRG International Journal of Mechanical Engineering, vol. 7, no. 6, pp. 13-19, 2020. Crossref, https://doi.org/10.14445/23488360/IJME-V7I6P102
Abstract:
Electrochemical machining (ECM) is a method of removing metal by an electrochemical process. The hard machine materials like high nickel, Cobalt, and titanium alloys can be machined by nonconventional machining. HC HCr dies steel is one of the hardest materials which are very difficult to machine using conventional machine tools because of its hardness values. Also, if used, the wear rate of the tool will be very high. Material removal is achieved by electrochemical dissolution of an anodically polarized workpiece, which is one part of an electrolytic cell in ECM. Hard metals can be shaped electrolytically by using ECM, and the rate of machining does not depend on their hardness. The tool electrode used in the process does not wear, and therefore soft metals can be used as tools to form shapes on harder workpieces, unlike conventional machining methods. The process is used to smooth surface, drill holes, form complex shapes, and remove fatigue cracks in steel structures. The Literature survey says that when velocity is directly proportional to MRR (Material Removal Rate). So we desired to improve the velocity of the electrolyte. The electrolytes pass through the tool holes. To enlarge the tool diameter 1 mm to 3 mm, finally, compare the experimental result of 1 mm and 3 mm diameter multi-jet tool. Which one are yield better MRR and Minimum surface roughness?
Keywords:
MATERIAL REMOVAL RATE, ECM, ELECTROLYTE
References:
[1] Lawrence, P., 1981 , Computer Aided Design for ECM Electrodes , Int. J. Mach. Tool Des. Res., V01.21 :379 385.
[2] E.J.Weller “Nontraditional Machining Soc iety of Manufacturing Engineers, Publications/Marketing Division, 1984 Technology & Engineering.
[3] “The Electronics Journal of the Electrochemical Society, Vol. 136, No.6: pp 285c 292c
[4] Ruszaj, A., Dziedzic, J., Czekaj, J., and Krehlik, M., 1995, Electrochemical Machining with Electrode Displacement Controlled in Three Axes” Axes”, Proceedings of the ISEM 11: 553 563.
[5] Prasanta Mishra 1997, Narosa Publishing House, Non Conventional Machining .
[6] Kozak, J., Rajurkar, K. P., Ruszaj, A., an d Slawinski, R. J., 1998, “Sculptured Surface By NCElectrochemica lMachining with Ball End Electrode, Advances in Technology of the Machines and Equipment, Vol. 22, No. 1: 53 74.
[7] S.K. Sorkhel, B. Bhattacharyya, C. Rudra. “Investigation for co ntrolled electrochemical machining through response surface methodology based approach” approach”, Jr. Mat. Proc.Tech, 1999; pp200 207
[8] M. Datta, D. Landolt, “Fundamental aspects and applications electrochemical micro fabrication”, Electro chemical Acta, 2000, pp2535 2558.
[9] R. Kurita, H. Jabei, Z. Liu, T. Hariuchi, O. Niwa, “Fabrication and electrochemical properties of an Inter digitated array electrode in a micro fabricated water jet cell, Sensors and Actuators‘ B’ Chemical” B71, 2000, pp 82 89.
[10] B. Bh attacharyya*, S. Mitra, A.K. Boro, “Electrochemical machining: new possibilities for micromachining. Robotics and Computer Integrated Manufacturing” 18 (2002) pp283 289
[11] B,Bhattacharyya and I.Munda, “Experimental investigations on influence of electr ochemical machining parameters on machining rate and accuracy in
micromachining domain”, International journal of machine tools and manufacture 43 (2003) pp 1301 1310
[12] H. Ohmori, K. Katahira, Y. Vehara, Y. Watanabe, W. Liu, “Improvement of mechanica l strength of micro tools by controlling surface characteristics”, Annals of the CIRP 52 (1), 2003, pp 467 470.
[13] A. Rajeshkumar, Dr.S. Venkatesan, Review Parameters of Electrochemical Maching For 410b Stinless Steel, SSRG International Journal of Mechanical Engineering 6(1)(2019)1-6.
[14] B.Bhattacharyya, J.Munda and M.Malapati, “Advancement in electrochemical micromachining, International Journal of Machine Tools and Manufac turer”, 2004, pp 1577 1589
[15] Anjali V. Kulkarni, “Electrochemical machining Defence Science journal Vol. 57, No 5, September 2007, pp.765 770
[16] Dr. T.Sekar and Marappan R, “Investigating the Material Removal Rate and Surface Roughness in El ectrochemical Machining of High Carbon High Chromium Die Steel” Steel”,Int. Journal of Engineering Research and Industrial Applications, Vol. 1, No. III, 2008, pp 121 130.
[17] Dr. T.Sekar and Marappan R, Dr. T.Sekar and Marappan R, “Improving Material “Improving Material Removal Rate of Electrochemical MachinRemoval Rate of Electrochemical Machining by Using ing by Using Rotating Tool”, Rotating Tool”, Int. Journal of Engineering Research and Int. Journal of Engineering Research and Industrial Applications, VoIndustrial Applications, Vol. 1, No. III, 2008, pp 121l. 1, No. III, 2008, pp 121--130130..
[18] V. Sathiyamoorthy and Dr. T.Sekar , Electrochemical V. Sathiyamoorthy and Dr. T.Sekar , Electrochemical Machining Machining –– A Review, 1st International Conference in A Review, 1st International Conference in South Asia OnSouth Asia On “Global Manufacturing Systems & “Global Manufacturing Systems & Management” Management” (ICGMSM 2011), 1st (ICGMSM 2011), 1st –– 3rd Augest2011, 3rd Augest2011, Coimbatore institute of technology, coimbatore.Coimbatore institute of technology, coimbatore.
[19] T.sekar Dr. R.marappan T.sekar Dr. R.marappan “Macro to Micro approach of “Macro to Micro approach of electrochemical machining electrochemical machining -- a review”, a review”, 2nd International 2nd International Conference OConference On Resource Utilization And Intelligent n Resource Utilization And Intelligent Systems, Kongu Engineering College, Erode, Tamilnadu, Systems, Kongu Engineering College, Erode, Tamilnadu, India.India.