Deep Cryogenically Treated Zinc Coated Diffused Brass Wire (ZCDBW) : State of the Art and Future Prospects
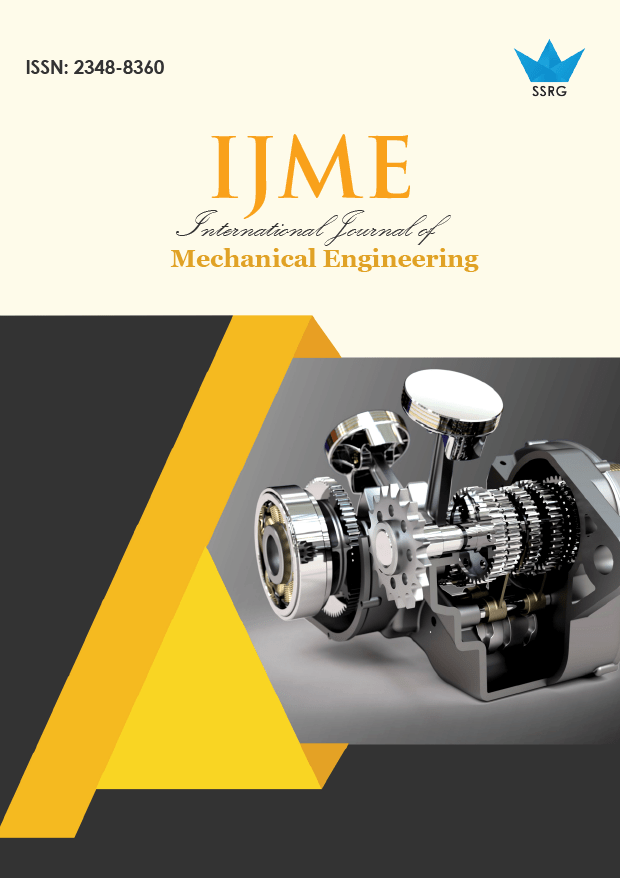
International Journal of Mechanical Engineering |
© 2020 by SSRG - IJME Journal |
Volume 7 Issue 10 |
Year of Publication : 2020 |
Authors : Kultar Singh |
How to Cite?
Kultar Singh, "Deep Cryogenically Treated Zinc Coated Diffused Brass Wire (ZCDBW) : State of the Art and Future Prospects," SSRG International Journal of Mechanical Engineering, vol. 7, no. 10, pp. 1-6, 2020. Crossref, https://doi.org/10.14445/23488360/IJME-V7I10P101
Abstract:
This paper reviews various aspects of deep cryogenically treated zinc coated diffused brass wire in this paper. Deep Cryogenic Treatment is carried out at about −184ºC (78 K). Deep cryogenic treatment is carried at -184ºC with a soaking time of 12 hours. Specimens were cooled at the rate of - 0.51ºC/min until they reach the final soaking temperature of -184ºC. Previously, when the zinc material was not coated on the diffused brass wire, it gave the following particulars, such as the zinc diffused brass wire was cryogenically treated and non-cryogenically treated which were being used as cutting tools. Now, in this paper, we will demonstrate the coating of zinc with diffused brass wire, which will perform certain functions such as an increase in wear resistance, increase in tool life, stepping - up of the tensile strength, toughness and also includes the release of internal stresses. With the coating of zinc material with brass wire gives us increased performance and durability. If we use the zinc coated material with diffused brass wire, it will be treated as a lifetime product.
Keywords:
Wire Cryogenically Treated, Deep Cryogenic Treatment, Brass wire, zinc.
References:
[1] A. Akhbarizadeh, Effects of cryogenic treatment on wear behavior of D6 tool steel, Materials & Design, 30(8) (2009) 3259-3264.
[2] A. Molinari, and M. Pellizzari, Effect of deep cryogenic treatment on the mechanical properties of tool steels, Journal of Materials Processing Technology, (118), pp. 350-355, 2001.
[3] KMW Seah, and M. Rahman, Performance evaluation of cryogenically treated tungsten carbide cutting tool inserts, Pro Engineering Manufacturing, 217 (2003) 29-43.
[4] YS. Liao, and YP Yu, Study of specific discharge energy in WEDM and its application, International Journal of Machining Tools & Manufacture. 44 (2004) 1373-1380.
[5] A. Bensely, and A. Prabbakaran, Enhancing the wear resistance of case carburized steel (EN 353) by cryogenic treatment,” Cryogenic, 45 (2006) 747-754.
[6] V. Leskovsek, and M. Kalin, Influence of deep cryogenic treatment on wear resistance of vacuum heat treated HSS,” Surface Instrumentation & Vacuum Technology, 80 (2006) 507-518,.
[7] S.S. Gill, and J. Singh, Effect of the deep cryogenic treatment on machinability of titanium alloy (Ti-6246) in electrical discharge drilling, International Journal of Materials & Manufacturing Processes. 25(6) (2010) 378-385.
[8] A. Okada, and T. Yamauchi, Effect of surface quality of brass coated wire on wire wire EDM characteristics, Journal of Advanced Mechanical Design, Systems and Manufacturing. 2(4) (2008) 735-741.
[9] A. Idayan, and A. Gnanavelbabu, Influence of deep cryogenic treatment on the mechanical properties of AISI 440 C bearing steel, Procedia Engineering, 97 (2014) 1683-1691.
[10] S.S. Gill, and R. Singh, Wear behavior of cryogenically treated tungsten carbide inserts under dry and wet turning conditions, International Journal of Machine Tool and Manufacturing, 49 (2009) 256-269.
[11] L.P. Singh, and J. Singh, “Effects of cryogenic treatment on high speed steel tool,” Journal of Engineering and Technology, vol. 1, pp. 41-47, 2011.
[12] J. Kapoor, and J.S. Khamba, Effects of cryogenic treated wire electrode on the surface of and EN-31steel machined by WEDM,” National Conference on Advancement and Futuristic Trends in Mechanical and Materials Engineering. 7 (2011) 100-106.
[13] N. Sharma, and R. Khanna, Optimization of process parameters of cryogenic treated D-3 in WEDM by Taguchi approach,
International Journal of Engineering and Applications, 1(3) (2011) 546-553.
[14] H. Singh, and A. Singh, Wear behaviour of AISI D3 die steel using cryogenic copper and brass electrode in electric discharge machining,” International Journal of Modern Engineering Research. 2(6) (2012) 4462-4464.
[15] A.S. Gill, and A. Thakur, Effect of Deep Cryogenic Treatment on the Surface Roughness of OHNS Die Steel after WEDM, International Journal of Applied Engineering Research, 7 (2012) 117-122.
[16] N. Singh, P. Kumar, and K. Goyal, Effect of two different cryogenic treated wires in wire electrical discharge machining of AISI D3 die steel,” Journal of Mechanical Engineering, 43(2) (2013) 54-60.
[17] D. Candane, N. Alagumurthi, and K. Palaniradja, Effect of cryogenic treatment on microstructure and wear characteristics of AISI M35 HSS, International Journal of Material Science and Applications, 2(2) (2013) 56-65.
[18] N. Singh, and P. Kumar, Experimental investigation of wire EDM variables on surface roughness of AISI D3 die steel by using two cryogenically treated different wires, Manufacturing Science and Technology, 2 (2014) 20-25.
[19] M. Kumar, and H. Singh, a review on Effect of deep cryogenic and shallow cryogenic heat treatment” on micro hardness and wear resistance of different steels, International Journal of Latest Trends in Engineering and Technology. e-ISSN: 2278-621X, (2017) 330-335.