Optimization of Process Parameters in Wire EDM Taper Cutting Process
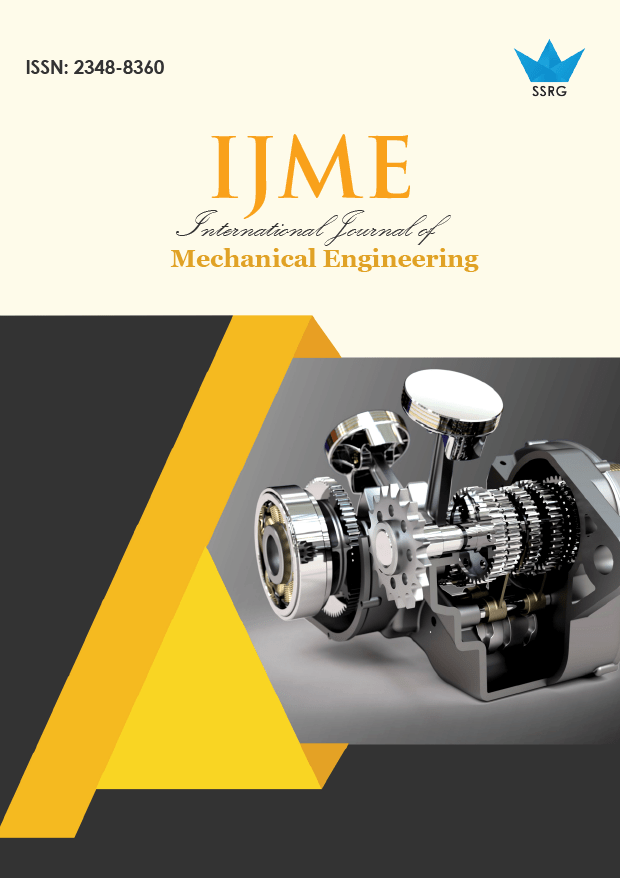
International Journal of Mechanical Engineering |
© 2021 by SSRG - IJME Journal |
Volume 8 Issue 9 |
Year of Publication : 2021 |
Authors : K.L. Uday Kiran, G. Chandra Mohan Reddy, A.M.K. Prasad |
How to Cite?
K.L. Uday Kiran, G. Chandra Mohan Reddy, A.M.K. Prasad, "Optimization of Process Parameters in Wire EDM Taper Cutting Process," SSRG International Journal of Mechanical Engineering, vol. 8, no. 9, pp. 11-16, 2021. Crossref, https://doi.org/10.14445/23488360/IJME-V8I9P102
Abstract:
Wire EDM taper cutting process is used to achieve curved surfaces for dies and moulds which is difficult by traditional machining and straight cutting. The present research deals with the parametric optimization of taper cutting process using wire EDM on AISI D2 steel. Taper angle, servo voltage and part thickness are the process parameters considered in this study along with angular error, cutting speed and surface roughness as responses. Response surface methodology with central composite design was employed to design the experiments. Relation between input parameters and responses is determined by developing regression mathematical models and analysis of variance is implemented to test the competence of the above analysis. Optimal combination of process parameters for minimum angular error and surface roughness with maximum cutting speed were identified by using desirability approach. Results show that the optimal set of process parameters are taper angle 6°, part thickness 30 mm and servo voltage 22 V respectively achieving desirability value of 0.749 with response values as angular error 0.078°, cutting speed 0.423 mm/min and surface roughness 1.511 μm.
Keywords:
Surface Finish, Wire EDM, Taper Angle, Cutting Speed, Angular Error, Response Surface Methodology, Analysis of Variance.
References:
[1] Albert Wen-Jeng Hsue, Hsin-Cheng Su, Removal analysis of WEDM’s tapering process and its application to generation of precise conjugate surface, Journal of Materials Processing Technology 149 (2004) 117–123
[2] N. Kinoshita, M. Fukui and T. Fujii, Study on Wire-EDM: Accuracy in taper cut, CIRP in Annals- Manufacturing Technology, 36 (1987) 119-122.
[3] M. Kinoshita, Control device for wire electric discharge machining with taper working correction function, Patent JP11165219A, (1997).
[4] D.F. Dauw, I. Beltrami, High-precision wire EDM by on-line wire position control, Annals of the CIRP 43/1 (1994) 193–197.
[5] A.B. Puri, B. Bhattacharyya, An analysis and optimisation of the geometrical inaccuracy due to the wire lag phenomenon in WEDM, International Journal of Machine Tools and Manufacture 43 (2003) 151–159.
[6] S. Plaza & N. Ortega & J. A. Sanchez & I. Pombo & A. Mendikute, Original models for the prediction of angular error in wire-EDM taper-cutting, Int J Adv Manuf Technol, 44 (2009) 529–538.
[7] J.A. Sanchez, S. Plaza, N. Ortega, M. Marcos, J. Albizuri, Experimental and numerical study of angular error in wire-EDM taper-cutting, International Journal of Machine Tools & Manufacture 48 (2008) 1420– 1428.
[8] Y.Y.Chiu, Y.S.Liao, H.C. Li and P.C. Sue, Study of taper cut machining of WEDM machine”, Proceeding of the 2nd Manufacturing Engineering Society International conference, drid, (2007).
[9] Bijaya Bijeta Nayak and Siba Sankar Mahapatra, A Utility Concept Approach for Multi-objective optimization of Taper Cutting Operation using WEDM, 12th Global Congress On Manufacturing And Management, GCMM 2014, Procedia Engineering 97 ( 2014 ) 469 – 478.
[10] Bijaya Bijeta Nayak and Siba Sankar Mahapatra, A Utility Concept Approach for Multi-objective optimization of Taper Cutting Operation using WEDM, 12th Global Congress On Manufacturing And Management, GCMM 2014, Procedia Engineering, 97 ( 2014 ) 469 – 478.
[11] Derringer G, Suich R, Simultaneous optimization of several response variables. J Qual Technol 12(4) (1980) 214–219
[12] Bijaya Bijeta Nayak, Parametric Optimization of Taper Cutting Process Using Wire Electrical Discharge Machining (WEDM), Ph.D Thesis submitted to National Institute of Technology, Rourkela , (2015).
[13] K.H. Ho, S.T. Newman, S. Rahimifard & R.D. Allen, State of the art in wire electrical discharge machining (WEDM), International Journal of Machine Tools & Manufacture 44 (2004) 1247–1259
[14] F. Martin, F. Altpeter, Method and device for measuring and adjusting the electrode for taper machining on an electrical discharge machine, Patent KR200601105616, (2006).
[15] J. A. Sanchez , S. Plaza a, L. N. Lopez De Lacalle& A. Lamikiz , Computer simulation of wire-EDM taper-cutting, International Journal of Computer Integrated Manufacturing, 19(7) (2006) 727 – 735
[16] Bijaya Bijeta Nayak & Siba Sankar Mahapatra, A Neuro-Fuzzy Approach For Optimization Of Multiple Responses In Taper Cutting Using Wire Electrical Discharge Machining, 5th International & 26th All India Manufacturing Technology, Design and Research Conference (AIMTDR 2014) (2014), IIT Guwahati, Assam, India
[17] G. Selvakumar, K. BravilinJiju and R. Veerajothi, Experimental Study onWire Electrical Discharge Machining of Tapered Parts, Arab J SciEng (2016) 41:4431–4439, DOI 10.1007/s13369-016-2145-z
[18] V. Manoj, Ranjit Joy & S. Narendranath, Investigation on the Effect of Variation in Cutting Speeds and Angleof Cut During Slant Type Taper Cutting in WEDM of Hastelloy X, Arabian Journal for Science and Engineering, King Fahd University of Petroleum & Minerals (2019).
[19] Anmol Singh Verma, Shankar Singh and Abhishek Singh, An Exploratory Investigation and Optimization of Taper Cutting Operation with Wire Electro Discharge Machining, Materials Today: Proceedings 24 (2020) 388–397.
[20] Muhammad Wasif, Syed A. Iqbal, Anis Fatima, Saima Yaqoob and Muhammad Tufail, Experimental investigation for the effects of wire EDM process parameters over the tapered cross-sectional workpieces of titanium alloys (Ti6Al-4V), Mechanical Sciences, 11 (2020) 221–232.
[21] J.A. Sanchez, J.L. Rodil, A. Herrero, L.N. Lopez de Lacalle, A. Lamikiz, On the influence of cutting speed limitation on the accuracy of wire-EDM corner-cutting, Journal of Materials Processing Technology 182 (2007) 574–579
[22] Vikram Singh, Rakesh Bhandari &Vinod Kumar Yadav, An experimental investigation on machining parameters of AISI D2 steel using WEDM, Int J AdvManuf Technolgy.
[23] Gopalkannan S, Senthilvelan T &Ranganathan S, Modelling and optimization of EDM parameters on machining of AL 7075-B4C MMC using RSM, Procedia Engineering 38 (2012) 685 – 690.
[24] PragyaShandilya, P.K.Jain and N.K. Jain, Parametric optimization during wire electrical discharge machining using response surface methodology, Procedia Engineering 38 (2012) 2371 – 2377.
[25] Chorng-JyhTzeng and Rui-Yang Chen, Optimization of Electric Discharge Machining Process Using the Response Surface Methodology and Genetic Algorithm Approach, international journal of precision engineering and manufacturing ,14(5) (2013) 709-717.
[26] Siva Prasad Arikatla, K.Tamil Mannan and Arkanti Krishnaiah, Parametric Optimization in Wire Electrical Discharge Machining of Titanium Alloy Using Response Surface Methodology, Materials Today: Proceedings 4 (2017) 1434–1441