Heat Transfer Enhancement through Perforated fin made by MMC by Reinforcing Aluminum with Graphite and Optimization of Design Parameters using Taguchi DOE Method
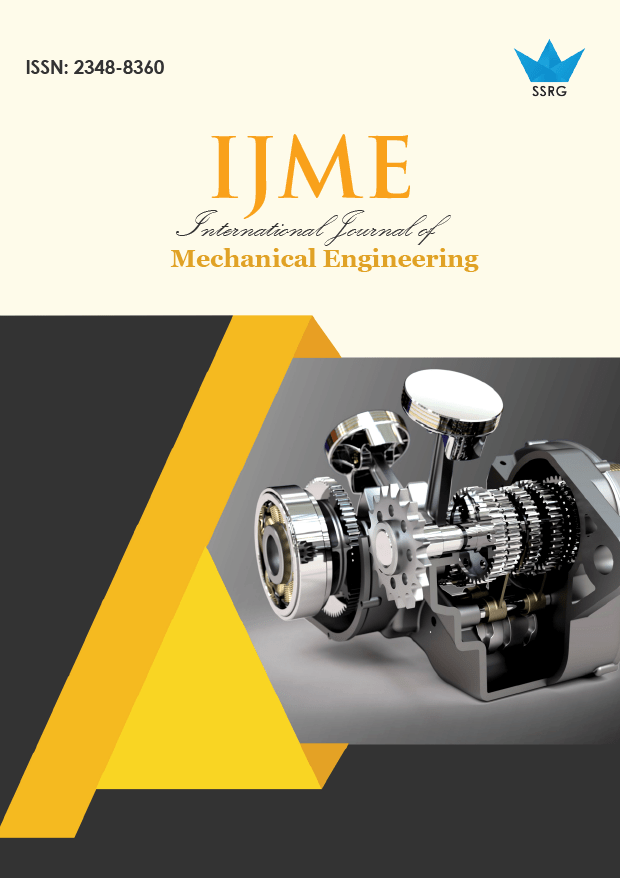
International Journal of Mechanical Engineering |
© 2022 by SSRG - IJME Journal |
Volume 9 Issue 4 |
Year of Publication : 2022 |
Authors : A. Kalyan Charan, R. Uday Kumar, B. Balunaik |
How to Cite?
A. Kalyan Charan, R. Uday Kumar, B. Balunaik, "Heat Transfer Enhancement through Perforated fin made by MMC by Reinforcing Aluminum with Graphite and Optimization of Design Parameters using Taguchi DOE Method," SSRG International Journal of Mechanical Engineering, vol. 9, no. 4, pp. 18-29, 2022. Crossref, https://doi.org/10.14445/23488360/IJME-V9I4P103
Abstract:
In comparison to other conventional fin materials, a stir casting process has been developed to produce aluminum–graphene (Al–Gr) metal matrix composites as a fin material. By Stir Casting, Fin Specimens were made with varied volume percentages of Graphite (5, 10, and 15%) in Al and Al as a base matrix. The rectangular fin's cross-sectional area was 40 mm x 3 mm, and its length was 100 mm. Experiments were conducted across a rectangular fin with lateral circular holes of varied porosities of 0.028, 0.038, 0.050, and 0.064, as well as variable flow rates from 4-7 m/s in 1 m/s increment. The design optimization parameters and associated levels were evaluated by using Taguchi L16 experimental design method. According to the findings, the heat transfer of the Al-Graphite nanocomposite was improved by increasing the volume percent of Gr particles. For porosity 0.064 friction factor and pressure drop, a combination of 85 percent Al-15 percent Gr produced a high heat transfer coefficient and enhanced heat transfer rate compared to standard aluminum. The optimal results were discovered for a fin composed of 85 percent Al - 15 percent Gr, which compares favorably to conventional fin materials while lighter and stronger than any of them. The fin's Porosity, velocity, and Composition yielded the best findings. According to research, the velocity, Porosity, and Composition have a greater influence on the heat transfer coefficient and Nusselt number.
Keywords:
Heat transfer coefficient, Heat transfer, Nusselt number, Perforations, Taguchi.
References:
[1] S.Pradeep Narayanan, and G. Venkatarathnam, “Analysis of the Performance of Heat Exchangers Used in Practical Micro Miniature Refrigerators,” Cryogenics, vol. 39, no. 6, pp. 517-527, 1999.
[CrossRef] [Google Scholar] [Publisher Link]
[2] Banerjee R, Karve et al., “Evaluation of Enhanced Heat Transfer within a Four-Row Finned Tube Array of an Air-Cooled Steam Condenser,” Numerical Heat Transfer, Part A: Applications, vol. 61, no. 10, pp. 735–753, 2012.
[CrossRef] [Google Scholar] [Publisher Link]
[3] Maha A. Hussein, Vinous M. Hameed, and Hussein T. Dhaiban, “An Implementation Study on a Heat Sink with Different Fin Configurations under Natural Convective Conditions,” Case Studies in Thermal Engineering, vol. 30, 2022.
[CrossRef] [Google Scholar] [Publisher Link]
[4] Yakar Gülay, and Karabacak Rasim, “Effects of Different Fin Spacings on the Nusselt Number and Reynolds Number in Perforated Finned Heat Exchangers,” Heat Transfer Engineering, vol. 32, no. 5, pp. 399-407, 2011.
[CrossRef] [Google Scholar] [Publisher Link]
[5] M. Penchal Reddy et al., “Structural, Mechanical and Thermal Characteristics of Al-Cu-Li Particle Reinforced Al-Matrix Composites Synthesized by Microwave Sintering and Hot Extrusion,” Composites Part B: Engineering, vol. 164, pp. 485-492, 2019.
[CrossRef] [Google Scholar] [Publisher Link]
[6] Mirle K Surappa, “Aluminium Matrix Composites: Challenges and Opportunities,” Sadhana, vol. 28, pp. 319-334, 2003.
[CrossRef] [Google Scholar] [Publisher Link]
[7] Hansang Kwon, “Investigation of Carbon Nanotube Reinforced Aluminum Matrix Composite Materials,” Composites Science and Technology, vol. 70, pp. 546-550, 2010.
[CrossRef] [Google Scholar] [Publisher Link]
[8] V. Mohanavel et al., “Mechanical Behavior of Hybrid Composite (AA6351+Al2O3+Gr) Fabricated by Stir Casting Method,” Materials Today: Proceedings, vol. 4, no. 2, pp. 3093-3101, 2017.
[CrossRef] [Google Scholar] [Publisher Link]
[9] Dipen Kumar Rajak et al., “Recent Progress of Reinforcement Materials: A Comprehensive Overview of Composite Materials,” Journal of Materials Research and Technology, vol. 8, no. 6, pp. 6354-6374, 2019.
[CrossRef] [Google Scholar] [Publisher Link]
[10] K. N. Arunkumar, and G. B. Krishnappa, “Mechanical Properties of Aluminum Metal Matrix Composites – A Review,” International Journal of Engineering Research & Technology (IJERT), vol. 11, no. 3, 2022.
[CrossRef] [Publisher Link]
[11] Vishal Singh Patyal, Sachin Modgil, and K. Maddulety, “Application of Taguchi Method of Experimental Design for Chemical Process Optimisation: A Case Study,” Asia-Pacific Journal of Management Research and Innovation, vol. 9, no. 3, pp. 231-238, 2013.
[CrossRef] [Google Scholar] [Publisher Link]
[12] B.K.Prasad, and S. Das, “The Significance of the Matrix Microstructure on the Solid Lubrication Characteristics of Graphite in Aluminum Alloys,” Materials Science and Engineering, vol. 144, no. 1-2, pp. 229-235, 1991.
[CrossRef] [Google Scholar] [Publisher Link]
[13] S. Kiwan, and M. A. Al-Nimr, “Using Porous Fins for Heat Transfer Enhancement,” Journal of Heat Transfer, vol. 123, no. 4, pp. 790-795, 2000.
[CrossRef] [Google Scholar] [Publisher Link]
[14] Jeom-Yul Yun, and Kwan-Soo Lee, “Influence of Design Parameters on the Heat Transfer and Flow Friction Characteristics of the Heat Exchanger with Slit Fins,” International Journal of Heat and Mass Transfer, vol. 43, no. 14, pp. 2529-2539, 2000.
[CrossRef] [Google Scholar] [Publisher Link]
[15] Nevin Celik, Gongur Pusat, and Emre Turgut, “Application of Taguchi Method and Grey Relational Analysis on a Tubulated Heat Exchanger,” International Journal of Thermal Sciences, vol. 124, pp. 85-97, 2018.
[CrossRef] [Google Scholar] [Publisher Link]
[16] Karima Boukhadia et al., “Effect of the Perforation Design on the Fluid Flow and Heat Transfer Characteristics of a Plate Fin Heat Exchanger,” International Journal of Thermal Sciences, vol. 126, pp. 172–180, 2018.
[CrossRef] [Google Scholar] [Publisher Link]
[17] Thamir K. Ibrahim et al., “Experimental Study on the Effect of Perforations Shapes on Vertical Heated Fins Performance Under Forced Convection Heat Transfer,” International Journal of Heat and Mass Transfer, vol. 118, pp. 832–846, 2018.
[CrossRef] [Google Scholar] [Publisher Link]
[18] Waleed Al-Salami, Amer Al-Damook, and H.M. Thompson, “A Numerical Investigation of the Thermal-Hydraulic Characteristics of Perforated Plate-Fin Heat Sinks,” International Journal of Thermal Sciences, vol. 121, pp. 266-277, 2017.
[CrossRef] [Google Scholar] [Publisher Link]
[19] Akhilesh Kumar Singh, and Rajiv Varshney, “Experimental Investigation on Rectangular Fins with Holes in Natural Convection,” International Journal of Engineering Development and Research, vol. 5, no. 4, pp. 157-166, 2017.
[Publisher Link]
[20] Assel Sakanova, “Heat Transfer Enhancement of Perforated Pin Heat Sink in Future Aircraft Applications,” Applied Thermal Engineering, vol. 124, pp. 315–326, 2017.
[CrossRef] [Google Scholar] [Publisher Link]
[21] R. Suresh, C. Srinivas, and Sneha. H. Doria, “Experimental Investigation of Thermal Conductivity of Aluminium Metal Matrix Composites,” International Journal of Engineering Development and Research, vol. 7, no. 3, pp. 341-346, 2019.
[Google Scholar] [Publisher Link]
[22] R. Akhil, “A Study on Recent Trends in the Applications of Metal Matrix Composites,” International Journal for Research in Applied Science & Engineering Technology, vol. 6, no. 5, pp. 172-180, 2018.
[CrossRef] [Google Scholar] [Publisher Link]
[23] Siddharth Swarnkar, and Ashish Kumar Upadhyay, “Comparison of Heat Transferring Fins of Conventional Aluminum and Metal Matrix Composites,” Journal of technological advances and scientific research, vol. 2, no. 2, pp. 131-134, 2016.
[Google Scholar]
[24] Lalit M Manocha, “High Performance Carbon–Carbon Composites,” Sadhana, vol. 28, pp. 349-358, 2003.
[CrossRef] [Google Scholar] [Publisher Link]
[25] Preetkanwal Singh Bains, Sarabjeet Singh Sidhu, and H. S. Payal, “Fabrication and Machining of Metal Matrix Composites : A Review,” Materials and Manufacturing Processes, vol. 31, no. 5, pp. 553-557, 2016.
[CrossRef] [Google Scholar] [Publisher Link]
[26] Y. Pratapa Reddy et al., “Fabrication and Thermal Analysis of Composite Pin-Fin,” International Journal of Core Engineering & Management, vol. 2, no. 5, pp. 77-89, 2015.
[Google Scholar] [Publisher Link]
[27] W. Kowbel, “High Thermal Conductivity SiC/SiC Composites for Fusion Applications,” Journal of Nuclear Materials, vol. 283-287, pp. 570-513, 2000.
[CrossRef] [Google Scholar] [Publisher Link]