Analysis of the Fatigue Life of Matrix Elements in the Hole Drilling Process in Sheet Metal Forming Dies
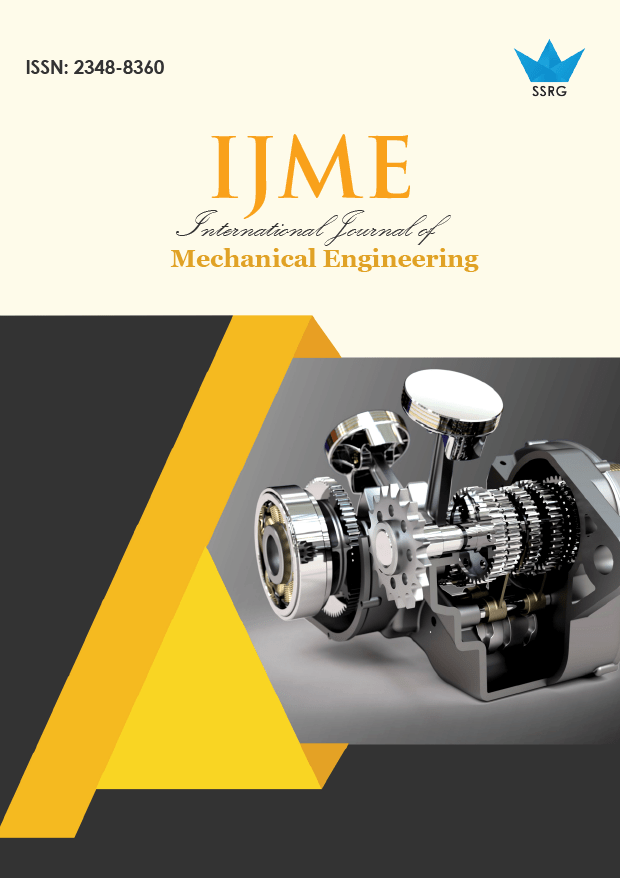
International Journal of Mechanical Engineering |
© 2022 by SSRG - IJME Journal |
Volume 9 Issue 7 |
Year of Publication : 2022 |
Authors : Yahya Işık, Hilal Kır, Mesut Mantarlar, Mustafa Yazar |
How to Cite?
Yahya Işık, Hilal Kır, Mesut Mantarlar, Mustafa Yazar, "Analysis of the Fatigue Life of Matrix Elements in the Hole Drilling Process in Sheet Metal Forming Dies," SSRG International Journal of Mechanical Engineering, vol. 9, no. 7, pp. 1-9, 2022. Crossref, https://doi.org/10.14445/23488360/IJME-V9I7P101
Abstract:
Sheet metal forming die technologies show great progress in the industry daily. Sheet metal dies design depends on many parameters such as the product's geometry, the die dimensions to be designed, the number of products, and part operation. The main purpose of the designs is to design the die with optimum parameters and to obtain high-quality products.One of the reasons for these errors is the damage to the die elements during operation. This studyanalyzed the final process of sheet metal forming dies using a progressive two-axis in-die conveying system designed with Catia V5 software. The lifetime analysis of the matrix element used in the hole drilling process was made with Ansys software, in which the finite element method was applied. The analysis compared two materials used in die design, AISI D2, and AISI A2 tool steels. The effects of matrix thickness on fatigue life were analyzed separately for matrices with 8 mm, 10 mm, and 12 mm thicknesses. According to the analysis results, it was concluded that the longest fatigue life is in the dies with a 12 mm thick matrix in which AISI D2 steel material is used.
Keywords:
Sheet metal forming, Drilling Process, Fatigue Analysis.
References:
[1] S. Mutlu, "Deep Drawing Automation with Progressive Dies," Trakya University Institute of Science and Technology, Edirne, MA, Mechanical Engineering, 2012.
[2] A. Baki et al., "Developing Innovative Feeder Bar Simulator for Transfer Press Dies," Engineer and Machinery, vol. 59, no. 692, pp. 68-85, 2018.
[3] M. Fırat, "Computer Aided Analysis and Design of Sheet Metal Forming Processes: Part III: Stamping Die-Face Design," Materials & Design, vol. 28, no. 4, pp. 1311-1320, 2007.
[CrossRef] [Google Scholar] [Publisher Link]
[4] I. N. Budak, and M. Pekedis, "Experimental and Numerical Analysis of Fatigue Behavior of Plastic Deformed Automobile Rod," Dokuz Eylul University Faculty of Engineering Journal of Science and Engineering, vol. 23, no. 68, pp. 647-659, 2021.
[5] Miao Wu et al., "Fatigue Analysis of İnjector Body Based on ANSYS Workbench," Vibroengineering Procedia, vol. 30, pp. 193- 198, 2020.
[CrossRef] [Google Scholar] [Publisher Link]
[6] K. Masuda et al., "Investigation of Subsurface Fatigue Crack Growth Behavior of D2 Tool Steel (JIS SKD11) Based on a Novel Measurement Method," International Journal of Fatigue, vol. 133, p. 105395, 2020.
[CrossRef] [Google Scholar] [Publisher Link]
[7] M.W. Fu, J. Lu, and W.L. Chan, "Die Fatigue Life İmprovement through the Rational Design of Metal-Forming System," Journal of Materials Processing Technology, vol. 209, no. 2, pp. 1074-1084, 2009.
[CrossRef] [Google Scholar] [Publisher Link]
[8] Ekici Bulent, and Kayabasi Oguz, "Predicted Fatigue Life of Sheet Metal Forming Die by Finite Element Method," UMTIK, 2008.
[Google Scholar] [Publisher Link]
[9] Young-Bin Park, and Jonathan S. Colton, "Fatigue of Reinforced-Polyurethane-Based, Sheet Metal Forming Dies," International Journal of Fatigue, vol. 28, no. 1, pp. 43-52, 2006.
[CrossRef] [Google Scholar] [Publisher Link]
[10] C. R. Alavala, "Effect of Temperature, Straın Rate and Coeffıcıent of Frıctıon on Deep Drawıng Process of 6061 Alumınum Alloy," International Journal of Mechanical Engineering, vol. 5, no. 6, pp. 11-24, 2016.
[Google Scholar] [Publisher Link]
[11] B. Falk, U. Engel, and M.Geiger, "Fundamental Aspects for the Evaluation of the Fatigue Behaviour of Cold Forging Tools," Journal of Materials Processing Technology, vol. 119, no. 1-3, pp. 158-164, 2001.
[CrossRef] [Google Scholar] [Publisher Link]
[12] Wei Min Li, Yang Yang Yan, and Ying Xingg, "The Numerical Simulation of Punching and the Fatigue Analysis of Punch Based on ANSYS/LS-DYNA and ANSYS-Fatigue Tool," Advanced Materials Research, vol. 904, pp. 469-473, 2014.
[CrossRef] [Google Scholar] [Publisher Link]
[13] In-Kyu Lee et al., "Prediction of Punch Life in Notching Process for Automatic Transmission Retainer Considering Fatigue and Wear," Journal of Mechanical Science and Technology, vol. 29, no. 12, pp. 5387-5393, 2015.
[CrossRef] [Google Scholar] [Publisher Link]
[14] K. Tong et al., "CAE Enabled Methodology for Die Fatigue Life Analysis and İmprovement," International Journal of Production Research, vol. 43, no. 1, pp. 131-146, 2005.
[CrossRef] [Google Scholar] [Publisher Link]
[15] V. Naranje et al., "Prediction of Life of Deep Drawing Die Using Artificial Neural Network," Advances in Materials and Processing Technologies, vol. 2, no. 1, pp. 132-142, 2016.
[CrossRef] [Google Scholar] [Publisher Link]
[16] Ayush Garg, "Fatigue Analysis and Optimization of Upright of a FSAE Vehicle," International Journal of Science and Research, vol. 6, no. 9, 2017.
[Google Scholar] [Publisher Link]
[17] A. Şık, M. Önder, and M.S. Korkmaz, "Determination of Fatigue Strength of Vehicle Wheels by Structural Analysis," GU J Sci Part: C, vol. 3, no. 3, pp. 565-574, 2015.
[Google Scholar] [Publisher Link]
[18] S. Madhusudhanan et al., "Fatigue Analysis of Automative Steering Knucle," Mechanics and Mechanical Engineering, vol. 20, no. 1, pp. 5-13, 2016.
[Google Scholar] [Publisher Link]
[19] A. Özcan, "Investigation the Effects on Geometric Properties of Product and Wearing in Progressive Die," Pamukkale University Institute of Science Mechanical Education, Denizli, MA, 2018.
[20] Uzochukwu Chimezie Okafor, "Mechanical Characterization of A2 and D2 Tool Steels by Nanoindentation," University of North Texas, Ph.D. Thesis, 2012. [CrossRef] [Publisher Link]
[21] Y. Yıldız, "Sheet Metal Cutting Process Modeling," Gazi University Institute of Science and Technology, Ankara, MA, Mechanical Engineering, 2013.
[22] Brahim Ben Fathallah, Chedly Braham, and Habib Sidhom, "Combined Effects of Abrasive Type and Cooling Mode on Fatigue Resistance of AISI D2 Ground Surface," International Journal of Fatigue, vol. 138, p. 105665, 2020.
[CrossRef] [Google Scholar] [Publisher Link]
[23] Ferhat Akyürek, Kemal Yaman, and Zafer Tekiner, "An Experimental Work on Tool Wear Affected by Die Clearance and Punch Hardness," Arabian Journal for Science and Engineering, vol. 42, no. 11, pp. 4683-4692, 2017.
[CrossRef] [Google Scholar] [Publisher Link]
[24] J. Nowicke, "Why Didn't my Thread Rolling Dies Last Longer?," Fastern Technology International, pp. 18-22,1991.
[Google Scholar]
[25] Jessica Booth, "Surface and Materials Analysis of Thread Rolling Dies," Worcester Polytechnic Institute, Massachusetts, Ph.D. Thesis, Mechanical Engineering, 2012.
[Google Scholar]
[26] George Roberts, George Krauss, and Richard Kennedy, Tool Steels, 5th Edition, ASM International, USA, pp. 363, 1998.
[Google Scholar] [Publisher Link]
[27] H. Aydın, I. O. Yılmaz, and A. Bilici, "Investigation of Microstructure and Mechanical Properties of Dissimilar Electrical Resistance Spot Welded Tbf/Dp600 Steel Sheets," Journal of the Faculty of Engineering and Architecture of Gazi University, vol. 37, no. 2, pp. 609-624, 2022.
[CrossRef] [Google Scholar] [Publisher Link]
[28] A. C. Reddy, "Formability Analysis of 6063 Al Alloy for Deep Drawn Cylindrical Cups with Constant and Progressive Blank Holding Force," SSRG International Journal of Mechanical Engineering, vol. 4, no. 5, pp. 26-32, 2017.
[CrossRef] [Google Scholar] [Publisher Link]