Numerical and Experimental Examination of Novel Delta Cut Winglet
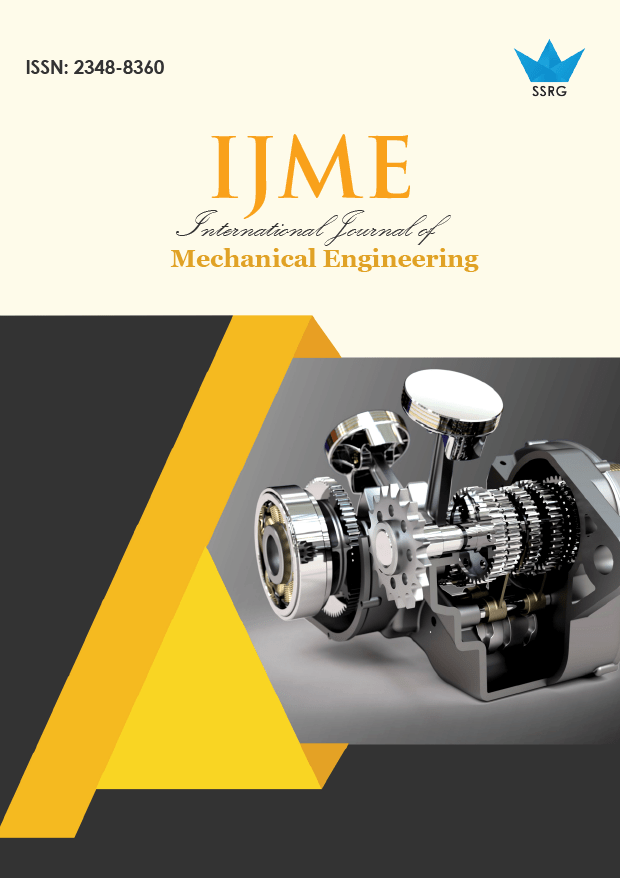
International Journal of Mechanical Engineering |
© 2023 by SSRG - IJME Journal |
Volume 10 Issue 7 |
Year of Publication : 2023 |
Authors : Vaibhav Pandey, Kaustubh Pawar, Shaunak Joshi, Sudesh Kadam, Harshad Deshpande |
How to Cite?
Vaibhav Pandey, Kaustubh Pawar, Shaunak Joshi, Sudesh Kadam, Harshad Deshpande, "Numerical and Experimental Examination of Novel Delta Cut Winglet," SSRG International Journal of Mechanical Engineering, vol. 10, no. 7, pp. 1-13, 2023. Crossref, https://doi.org/10.14445/23488360/IJME-V10I7P101
Abstract:
Details of a numerical and experimental investigation on the heat transfer characteristics for three-dimensional turbulent flows in a rectangular duct with punched Delta Cut Winglet are presented in the present article. The aim of the study is to examine the influence of the winglet shape, attack angles of 00 , 30°, 45°, 60°, 900 on different patterns viz., Inline and Staggered, Height of Perforation viz., H/2, H/3 and H/4, Diameter of Perforation 2.5mm, 3.25mm and 4mm on the Nusselt Number Ratio, Friction Factor Ratio and Thermal Enhancement Factor(TEF) for Reynolds numbers ranging from 12180.699 to 48722.796. The results are compared with turbulent flows' flow and heat transfer characteristics in rectangular ducts without winglets. Numerical results predict an augmentation in the thermal performance of the rectangular duct flows with winglets. Experimental results validate the results obtained in numerical analysis. By numerical analysis, we concluded that the ratio of Nusselt Number is more while the ratio of Friction Factor is less at an attack angle of 00 compared to 300 , 450 , 600 & 900 . By Numerical Analysis, we concluded that the Thermal Enhancement Factor is more at an attack angle of 00 than 300 , 450 , 600 & 900 . By Numerical Analysis, we concluded that the ratio of Nusselt Number is more while the ratio of Friction Factor is less, which complies with TEF is more when the height of perforation from the base of the winglet is H/2 as compared to H/3 and H/4. The values of Nu/Nu0 is 1.6248, and f/f0 is 0.8974. The highest value of TEF achieved is 1.6844.
Keywords:
Heat transfer, Rectangular Duct, Thermal Enhancement Factor, Turbulent Flow, Winglets.
References:
[1] Harshad Deshpande, Santosh Taji, and Vaijanath Raibhole, “Assessment of Heat Transfer Performance from Modified Horizontal Rectangular Heat Sink Under Forced Convection Dominating Mode of Mixed Convection,” Materials Today: Proceedings, vol. 47, pp. 5618–5628, 2021.
[CrossRef] [Google Scholar] [Publisher Link]
[2] Harshad Deshpande, and Vaijanath Raibhole, “Numerical Assessment of Thermal Performance of Heated Air Duct with Novel Arc Profile Ribs in Non-interrupted Arrangement,” Materials Today: Proceedings, vol. 63, pp. 6-14, 2022.
[CrossRef] [Google Scholar] [Publisher Link]
[3] Mehmet Dogan, and Sait Erzincan, “Experimental Investigation of Thermal Performance of Novel Type Vortex Generator in Rectangular Channel,” International Communications in Heat and Mass Transfer, vol. 144, p. 106785, 2023.
[CrossRef] [Google Scholar] [Publisher Link]
[4] Ashish J Modi, Navnath A Kalel, and Manish K Rathod, “Thermal Performance Augmentation of Fin-and-tube Heat Exchanger using Rectangular Winglet Vortex Generators having Circular Punched Holes,” International Journal of Heat and Mass Transfer, vol. 158, p. 119724, 2020.
[CrossRef] [Google Scholar] [Publisher Link]
[5] Arvind Gupta et al., “Numerical Investigation towards Implementation of Punched Winglet as Vortex Generator for Performance Improvement of a Fin-and-tube Heat Exchanger,” International Journal of Heat and Mass Transfer, vol. 149, p. 119171, 2020.
[CrossRef] [Google Scholar] [Publisher Link]
[6] S. Prathiban, and B. Sivaraman, “Experimental Investigation of Effective Adiabatic Length as A Heat Pipe Heat Exchanger,” International Journal of Engineering Trends and Technology, vol. 69, no. 6, pp. 43-49, 2021.
[CrossRef] [Publisher Link]
[7] KeWei Song et al., “Heat Transfer Characteristics of Concave and Convex Curved Vortex Generators in the Channel of Plate Heat Exchanger under Laminar Flow,” International Journal of Thermal Sciences, vol. 137, pp. 215–228, 2019.
[CrossRef] [Google Scholar] [Publisher Link]
[8] Pongjet Promvonge, and Sompol Skullong, “Enhanced Heat Transfer in Rectangular Duct with Punched Winglets,” Chinese Journal of Chemical Engineering, vol. 28, no. 3, pp. 660-671, 2020.
[CrossRef] [Google Scholar] [Publisher Link]
[9] Zhimin Han, Zhiming Xu, and Jingtao Wang, “Numerical Simulation on Heat Transfer Characteristics of Rectangular Vortex Generators with a Hole,” International Journal of Heat and Mass Transfer, vol. 126, pp. 993–1001, 2018.
[CrossRef] [Google Scholar] [Publisher Link]
[10] Naveen Sharma, Andallib Tariq, and Manish Mishra, “Detailed Heat Transfer and Fluid Flow Investigation in a Rectangular Duct with Truncated Prismatic Ribs,” Experimental Thermal and Fluid Science, vol. 96, pp. 383–396, 2018.
[CrossRef] [Google Scholar] [Publisher Link]
[11] Virendra Bisen, and N. K. Sagar, “A Review on Thermal Performance Analysis for Annular Fins of Various Profiles using Ansys,” SSRG International Journal of Thermal Engineering, vol. 4, no. 3, pp. 5-7, 2018.
[CrossRef] [Publisher Link]
[12] Varchasvi Nandana, and Uwe Janoske, “Numerical Study on the Enhancement of Heat Transfer Performance in a Rectangular Duct with New Winglet Shapes,” Thermal Science and Engineering Progress, vol. 6, pp. 95-103, 2018.
[CrossRef] [Google Scholar] [Publisher Link]
[13] S. Alfarawi, S. A. Abdel-Moneim, and A. Bodalal, “Experimental Investigations of Heat Transfer Enhancement from Rectangular Duct Roughened by Hybrid Ribs,” International Journal of Thermal Sciences, vol. 118, pp. 123-138, 2017.
[CrossRef] [Google Scholar] [Publisher Link]
[14] Hao Wu, David S. K. Ting, and Steve Ray, “The Effect of Delta Winglet Attack Angle on the Heat Transfer Performance of a Flat Surface,” International Journal of Heat and Mass Transfer, vol. 120, pp. 117–126, 2018.
[CrossRef] [Google Scholar] [Publisher Link]
[15] P. Selvakumar et al., “Thermal Plant Condenser Tube Advanced Applied Research on Scale Formation with and Without Magnets in the Water Lines,” International Journal of Engineering Trends and Technology, vol. 70, no. 5, pp. 173-184, 2022.
[CrossRef] [Publisher Link]
[16] Yonggang Lei et al., “Improving the Thermal Hydraulic Performance of a Circular Tube by using Punched Delta-Winglet Vortex Generators,” International Journal of Heat and Mass Transfer, vol. 111, pp. 299–311, 2017.
[CrossRef] [Google Scholar] [Publisher Link]
[17] Abhay P Asagaonkar, R. D. Shelke, and H. N. Deshpande, “Numerical Investigation of Flow and Heat Transfer Over a Flat Plate using Curved Rectangular Winglet Vortex Generators,” International Journal of Current Engineering and Technology, pp. 124-128, 2023.
[CrossRef] [Publisher Link]
[18] L. H. Tang et al., “A New Configuration of Winglet Longitudinal Vortex Generator to Enhance Heat Transfer in a Rectangular Channel,” Applied Thermal Engineering, vol. 104, pp. 74-84, 2016.
[CrossRef] [Google Scholar] [Publisher Link]
[19] Sombat Tamna, Somchai Sripattanapipat, and Pongjet Promvonge, “Numerical Heat Transfer Study of Turbulent Tube Flow Through Winglet-Pairs,” Energy Procedia, vol. 100, pp. 518-521, 2016.
[CrossRef] [Google Scholar] [Publisher Link]
[20] A. Lemouedda et al., “Optimization of the Angle of Attack of Delta-winglet Vortex Generators in a Plate-fin-and-Tube Heat Exchanger,” International Journal of Heat and Mass Transfer, vol. 53, no. 23-24, pp. 5386–5399, 2010.
[CrossRef] [Google Scholar] [Publisher Link]