A Proposed Model for Productivity Improvement by Implementation of Lean Manufacturing Techniques in a Textile Industry
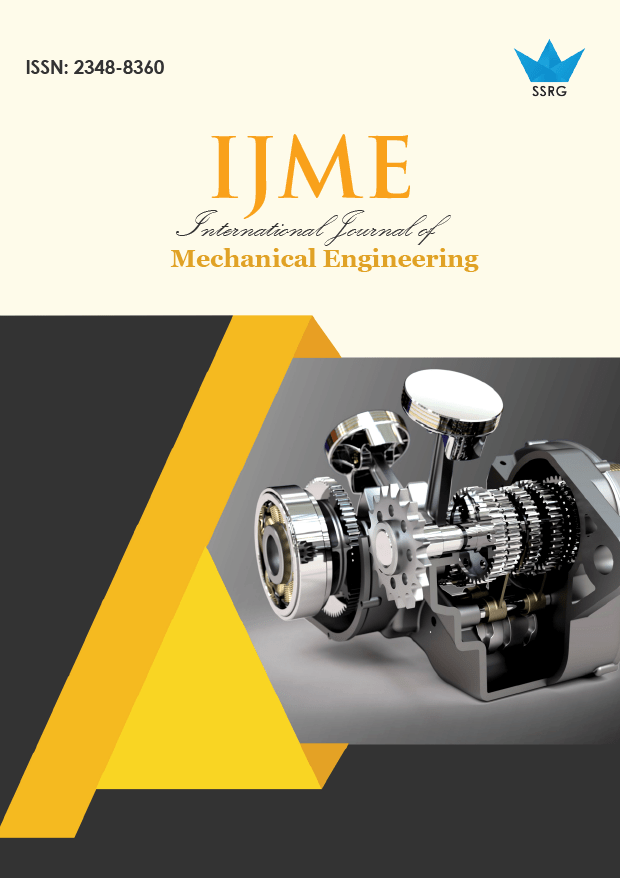
International Journal of Mechanical Engineering |
© 2023 by SSRG - IJME Journal |
Volume 10 Issue 8 |
Year of Publication : 2023 |
Authors : S. Saravanan, Partha Sarathi Chakraborty, S. Nallusamy, V. Kumar |
How to Cite?
S. Saravanan, Partha Sarathi Chakraborty, S. Nallusamy, V. Kumar, "A Proposed Model for Productivity Improvement by Implementation of Lean Manufacturing Techniques in a Textile Industry," SSRG International Journal of Mechanical Engineering, vol. 10, no. 8, pp. 31-48, 2023. Crossref, https://doi.org/10.14445/23488360/IJME-V10I8P104
Abstract:
The development of the textile sector in India has experienced significant growth in recent years, becoming one of the main economic activities of the textile-industrial sector in south India. Many organisations face new competition and macroeconomic conditions in the current textile manufacturing scenario. Lean manufacturing system adoption is increasing due to the industry’s challenges in this swiftly changing world. Lean manufacturing makes an organisation more flexible and adaptable as change occurs. More than ten per cent of Non-Value-Added Activities (NVA) from the total production of an organisation direct to loss. The main task of lean manufacturing is to maximise resource utilisation by minimising unwanted waste. This research aims to reduce waste by executing different lean techniques after adequately studying the current process. The lean execution in the textile industry is minimal, and different existing studies identify the research gap in implementing a sequence of lean elements in a selected industry. Implementing the proposed layout reduces the cycle time from 472 seconds to 438 seconds, and operator movement for the industry is reduced from 153 feet to 117 feet. After the proper execution of various lean techniques, it was observed that the overall productivity increased by 4.84%.
Keywords:
Textile industry, Waste reduction, Lean tools, Inventory control, Visual management.
References:
[1] Suraj Kumar, “Lean Manufacturing and Its Implementation,” International Journal of Advanced Mechanical Engineering, vol. 4, no. 2, pp. 231-238, 2014.
[Google Scholar] [Publisher Link]
[2] V. Saravanan, S. Nallusamy, and Abraham George, “Efficiency Enhancement in a Medium Scale Gearbox Manufacturing Company through Different Lean Tools - A Case Study,” International Journal of Engineering Research in Africa, vol. 34, pp. 128-138, 2018.
[CrossRef] [Google Scholar] [Publisher Link]
[3] Naveen Kumar et al., “Lean Manufacturing Techniques and Its Implementation: A Review,” Materials Today: Proceedings, vol. 64, no. 3, pp. 188-1192, 2022.
[CrossRef] [Google Scholar] [Publisher Link]
[4] R. Sundar, A. N. Balaji, and R. M. Satheesh Kumar, “A Review on Lean Manufacturing Implementation Techniques,” Procedia Engineering, vol. 97, pp. 1875-1885, 2014.
[CrossRef] [Google Scholar] [Publisher Link]
[5] Helena Dahlbo et al., “Increasing Textile Circulation - Consequences and Requirements,” Sustainable Production and Consumption, vol. 9, pp. 44-57, 2017.
[CrossRef] [Google Scholar] [Publisher Link]
[6] P. Neves et al., “Implementing Lean Tools in the Manufacturing Process of Trimmings Products,” Procedia Manufacturing, vol. 17, pp. 696-704, 2018.
[CrossRef] [Google Scholar] [Publisher Link]
[7] Oluwatosin Babalola, Eziyi O. Ibem, and Isidore C. Ezema, “Implementation of Lean Practices in the Construction Industry: A Systematic Review,” Building and Environment, vol. 148, pp. 34-43, 2019.
[CrossRef] [Google Scholar] [Publisher Link]
[8] V. Saravanan, S. Nallusamy, and K. Balaji, “Lead Time Reduction through Execution of Lean Tool for Productivity Enhancement in Small Scale Industries,” International Journal of Engineering Research in Africa, vol. 34, pp. 116-127, 2018.
[CrossRef] [Google Scholar] [Publisher Link]
[9] T. Karthik, “Improvisation of Productivity through Layout Optimisation in Pump Industry,” International Journal of Lean Thinking, vol. 3, pp. 90-10, 2012.
[Google Scholar]
[10] Bobby John, Jubin James, and R. Mahesh Rengaraj, “Analysis and Optimisation of Plant Layout using Relative Allocation of Facilities Techniques,” International Journal of Emerging Technology and Advanced Engineering, vol. 3, no. 8, pp. 514-520, 2013.
[Google Scholar] [Publisher Link]
[11] S. Santhoshkumar, and M. Pradeepkumar, “Cycle Reduction of a Truck Body Assembly in an Automobile Industry by Lean Principles,” Procedia Materials Science, vol. 5, pp. 1853-1862, 2014.
[CrossRef] [Google Scholar] [Publisher Link]
[12] Samuel V. Pandit et al., “Productivity Improvement by Application of Line Balancing,” International Journal of Innovative Research in Science, Engineering and Technology, vol. 3, no. 4, pp. 11495-11502, 2014.
[Google Scholar] [Publisher Link]
[13] Gunji Venkata Punna Rao, S. Nallusamy, and M. Rajaram Narayanan, “Augmentation of Production Level using Different Lean Approaches in Medium Scale Manufacturing Industries,” International Journal of Mechanical Engineering and Technology, vol. 8, no. 12, pp. 360-372, 2017.
[Google Scholar] [Publisher Link]
[14] D. Sobya, and S. Jeyabalan, “Enhancement of Production Rate and Flexibility in an Assembly Line by Execution of Various Lean Techniques-A Case Study,” International Journal of Engineering Research in Africa, vol. 51, pp. 15-27, 2020.
[CrossRef] [Google Scholar] [Publisher Link]
[15] Qiong Mou, Yunlong Cheng, and Huchang Liao, “A Note on Lead Time Reduction Strategies in a Single-Vendor-Single-Buyer Integrated Inventory Model with Lot Size-Dependent Lead Times and Stochastic Demand,” International Journal of Production Economics, vol. 193, pp. 827-831, 2017.
[CrossRef] [Google Scholar] [Publisher Link]
[16] Muhammad Kholil et al., “Implementation of Continuous Review System Method, Periodic Review System Method and Min-Max Method for Cheese Powder Inventory (Case Study: PT. Mayora IndahTBK),” SSRG International Journal of Industrial Engineering, vol. 7, no. 2, pp. 17-22, 2020.
[CrossRef] [Google Scholar] [Publisher Link]
[17] Fikile Poswa, Olukorede Tijani Adenuga, and Khumbulani Mpofu, “Productivity Improvement using Simulated Value Stream Mapping: A Case Study of the Truck Manufacturing Industry,” Processes, vol. 10, no. 9, pp. 1-17, 2022.
[CrossRef] [Google Scholar] [Publisher Link]
[18] Qingqi Liu, Hualong Yang, and Yuchen Xin, “Applying Value Stream Mapping in an Unbalanced Production Line: A Case Study of a Chinese Food Processing Enterprise,” Quality Engineering, vol. 32, no. 1, pp. 111-123, 2020.
[CrossRef] [Google Scholar] [Publisher Link]
[19] Abhishek P G, and Maheshwar Pratap, “Achieving Lean Warehousing through Value Stream Mapping,” South Asian Research Journal of Business and Management Cases, vol. 9, no. 3, pp. 387-401, 2020.
[CrossRef] [Google Scholar] [Publisher Link]
[20] D. Roy, and D. Khan, “Assembly Line Balancing to Minimise Balancing Loss and System Loss,” International Journal of Industrial Engineering, vol. 6, no. 11, pp. 1-5, 2010.
[Google Scholar] [Publisher Link]
[21] Lucas Stelle Chemim, Nicolle Christine Sotsek, and Mariana Kleina, “Layout Optimisation Methods and Tools: A Systematic Literature Review,” Management of Production, Operations and Systems, vol. 16, no. 4, pp. 59-81, 2021.
[CrossRef] [Google Scholar] [Publisher Link]
[22] György Kovács, and Sebastian Kot, “Facility Layout Redesign for Efficiency Improvement and Cost Reduction,” Journal of Applied Mathematics and Computational Mechanics, vol. 16, no. 1, pp. 63-74, 2017.
[CrossRef] [Google Scholar] [Publisher Link]
[23] Chao Guan et al., “Multi-Objective Particle Swarm Optimization for Multi-Workshop Facility Layout Problem,” Journal of Manufacturing Systems, vol. 53, pp. 32-48, 2019.
[CrossRef] [Google Scholar] [Publisher Link]
[24] Ahmad M. Qamar et al., “Optimisation of Plant Layout in Jordan Light Vehicle Manufacturing Company,” Journal of the Institution of Engineers (India): Series C, vol. 101, no. 4, pp. 721-728, 2020.
[CrossRef] [Google Scholar] [Publisher Link]
[25] Senthil Kumar, and Samuel Thavaraj, “Impact of Lean Manufacturing Practices on Clothing Industry Performance,” SSRN Electronic Journal, vol. 5, no. 2, pp. 1-14, 2015.
[CrossRef] [Google Scholar] [Publisher Link]
[26] D. Vasanth Kumar, G. Madhan Mohan, and K. M. Mohanasundaram, “Lean Tool Implementation in the Garment Industry,” Fibres & Textiles in Eastern Europe, vol. 27, no. 2, pp. 19-23, 2019.
[CrossRef] [Google Scholar] [Publisher Link]
[27] Silva S K P N, “Applicability of Value Stream Mapping (VSM) in the Apparel Industry in Srilanka,” International Journal of Lean Thinking, vol. 3, no. 1, pp. 36-41, 2011.
[Google Scholar] [Publisher Link]
[28] B. Senthil Kumar, “Value Stream Mapping-A Lean Manufacturing Approach to Reduce the Process Wastages in Clothing Industry,” International Journal of Advances in Management and Economics, vol. 5, no. 5, pp. 22-33, 2016.
[Google Scholar] [Publisher Link]
[29] S. Nallusamy et al., “A Review on Supplier Selection Problem in Regular Area of Application,” International Journal of Applied Engineering Research, vol. 10, no. 62, pp. 128-132, 2015.
[Google Scholar]
[30] K. Balakannan et al., “Selection and Evaluation of Supplier by Decision Model of Hybrid Data Envelopment Analysis,” International Journal of Applied Engineering Research, vol. 10, no. 62, pp. 123-127, 2015.
[Google Scholar]
[31] Albari Antunes Junior, and Evandro Eduardo Broday, “Adopting PDCA to Loss Reduction: A Case Study in a Food Industry in Southern Brazil,” International Journal for Quality Research, vol. 13, no. 2, pp. 335-348, 2019.
[Google Scholar] [Publisher Link]
[32] D. Sri Lakshmana Kumar, S. Nallusamy, and V. Ramakrishnan, “Proposed Inventory Management Model to Improve the Supply Chain Efficiency and Surplus in Textile Industry,” International Journal of Mechanical Engineering and Technology, vol. 9, no. 5, pp. 675- 686, 2018.
[Google Scholar] [Publisher Link]
[33] Ali Khaleel Dhaiban, and Ehab A. Mahmood, “The Effect of Initial Inventory Level on the Rates of Deteriorating and Production,” SSRG International Journal of Economics and Management Studies, vol. 5, no. 2, pp. 12-15, 2018.
[CrossRef] [Google Scholar] [Publisher Link]
[34] Ravinder Kumar, “Kaizen a Tool for Continuous Quality Improvement in Indian Manufacturing Organization,” International Journal of Mathematical, Engineering and Management Sciences, vol. 4, no. 2, pp. 452-459, 2019.
[CrossRef] [Google Scholar] [Publisher Link]
[35] Jie Ma, Zhibin Lin, and Chi Keung Lau, “Prioritising the Enablers for the Successful Implementation of Kaizen in China: A Fuzzy AHP Study,” International Journal of Quality & Reliability Management, vol. 34, no. 4, pp. 549-568, 2017.
[CrossRef] [Google Scholar] [Publisher Link]