Performance Evaluation of A Hydrodynamic Journal Bearing using Nano Ferro Fluid Lubricants with Varying Concentration of Iron Oxide Nanoparticle Additives (Fe3O4)
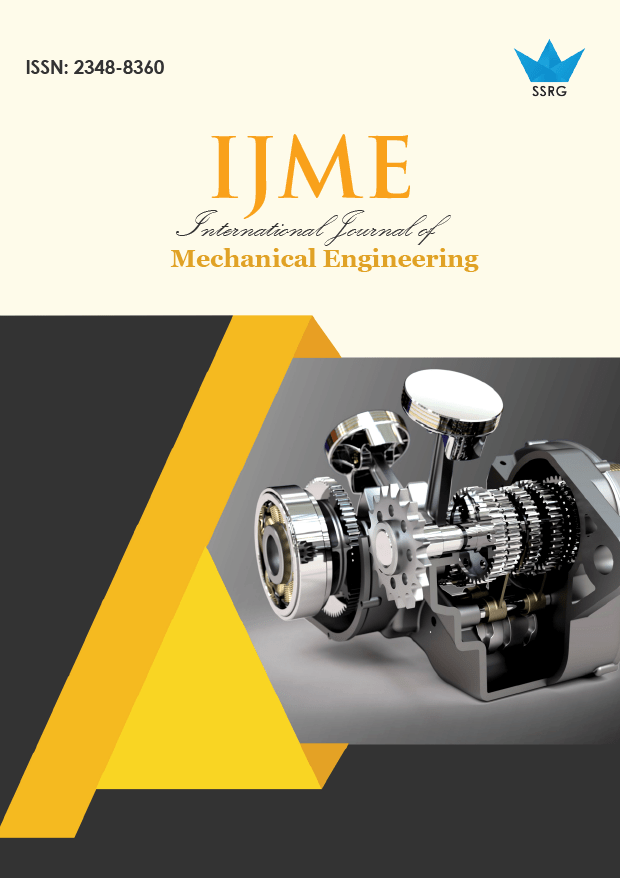
International Journal of Mechanical Engineering |
© 2023 by SSRG - IJME Journal |
Volume 10 Issue 8 |
Year of Publication : 2023 |
Authors : B. Vijaya Krishna, N. Seetharamaiah, L. Siva Rama Krishna |
How to Cite?
B. Vijaya Krishna, N. Seetharamaiah, L. Siva Rama Krishna, "Performance Evaluation of A Hydrodynamic Journal Bearing using Nano Ferro Fluid Lubricants with Varying Concentration of Iron Oxide Nanoparticle Additives (Fe3O4)," SSRG International Journal of Mechanical Engineering, vol. 10, no. 8, pp. 60-74, 2023. Crossref, https://doi.org/10.14445/23488360/IJME-V10I8P106
Abstract:
Hydrodynamic journal bearings are essential for boosting any machine’s dependability. When the interplay of geometry, surface motion, and fluid viscosity culminates in generating adequate fluid pressure to uphold the applied load, it gives rise to the formation of a hydrodynamic film. The additional pressure pushes the surfaces apart, preventing them from making contact. This phenomenon is known as hydrodynamic lift. Hydrodynamic lift supports the load on hydrodynamic bearings. Hydrodynamic journal bearings operate within a lubricated environment, where lubrication primarily aims to mitigate friction, wear, and heat generation among machine components undergoing relative motion. Therefore, advancements in lubrication techniques play a pivotal role in profoundly enhancing the effectiveness of these bearings. Modifications to oil lubrication properties are used to monitor bearing behavior. Variations in lubricant properties have a significant impact on how well a bearing works. In the present experimental investigations, the effects of the Nano Ferro particles on SAE 30 oil were examined. Experiments were conducted on a Hydrodynamic Journal bearing Test rig using Nano Ferro Fluid Lubricants. Nano Ferro Lubricants are made by altering the amounts of lubricant additives in concentrations such as 15%, 20%, and 25% in Castrol SAE 30 oil. The viscosity of the lubricating oil increased by adding nanoparticles, which improves the journal bearing’s performance characteristics, such as heat absorption and pressure reduction capacity. With the aid of a sophisticated mechanical agitator, nanoparticles utilized for work are combined with base oil in volume fractions of 15%, 20%, and 25%. Experimental research on pressure dissemination, load supporting capacity, bearing characteristic number, friction coefficient, Sommerfeld number, and heat generation is done using a hydrodynamic journal bearing test rig,500,600 and 700 rpm are used to assess a bearing’s performance along with 100 150 and 200 N of load. The results show that adding Nano Ferro Particles (Fe3O4) as lubricant additives increases the maximum pressure absorption capacity and load carrying capacity of journal bearings while decreasing bearing characteristic number, coefficient friction, Sommerfeld number, and heat generation when compared to base oil without nanoparticle additives.
Keywords:
Design parameters, Journal bearing, Lubricant additives, Nano ferro fluids, Volume concertation.
References:
[1] F. Quinci et al., “A Comparative Performance Assessment of a Hydrodynamic Journal Bearing Lubricated with Oil and Magnetorheological Fluid,” Tribology International, vol. 162, 2021.
[CrossRef] [Google Scholar] [Publisher Link]
[2] K. P. Gertzos, P. G. Nikolakopoulosm, and C. A. Papadopoulos, “CFD Analysis of Journal Bearing Hydrodynamic Lubrication by Bingham Lubricant,” Tribology International, vol. 41, no. 12, pp. 1190-1204, 2018.
[CrossRef] [Google Scholar] [Publisher Link]
[3] Satish C. Sharma, and Nathi Ram, “Influence of Micropolar Lubricants on the Performance of Slot-Entry Hybrid Journal Bearing,” Tribology International, vol. 44, no. 13, pp. 1852–1863, 2011.
[CrossRef] [Google Scholar] [Publisher Link]
[4] Robert Goraj, “Theoretical Study on a Novel Electromagnetically Supported Hydrodynamic Bearing under Static Loads,” Tribology International, vol. 119, pp. 775-785, 2018.
[CrossRef] [Google Scholar] [Publisher Link]
[5] J. Bouyer, Y. Alexandre, and M. Fillon, “Experimental Investigation on the Influence of a Multi-Scratched Shaft on Hydrodynamic Journal Bearing Performance,” Tribology International, vol. 153, 2021.
[CrossRef] [Google Scholar] [Publisher Link]
[6] Tushar P. Gundarneeya, and D. P. Vakharia, “Performance Analysis of Journal Bearing Operating on Nano Lubricants with TiO2, Cuo and Al2O3 Nanoparticles as Lubricant Additives,” Materials Today Proceedings, vol. 45, no. 6, pp. 5624-5630, 2021.
[CrossRef] [Google Scholar] [Publisher Link]
[7] Z. Rasep, M. N. A. W. Muhammad Yazid, and S. Samion, “Lubrication of Textured Journal Bearing by using Vegetable Oil: A Review of Approaches, Challenges and Opportunities,” Renewable and Sustainable Energy Reviews, vol. 146, 2021.
[CrossRef] [Google Scholar] [Publisher Link]
[8] Shasha Vali Shaik, D. Dev Singh, and Avinash Patil, “Experimental Investigation of Tribological Properties of TiO2 Nanoparticles in Engine Oil,” Materials Today Proceedings, vol. 46, pp. 883–889, 2021.
[CrossRef] [Google Scholar] [Publisher Link]
[9] Raman Kumar et al., “An Outline on Modern Day Applications of Solid Lubricants,” Materials Today Proceedings, vol. 28, no. 5, pp. 1962-1967, 2020.
[CrossRef] [Google Scholar] [Publisher Link]
[10] Vineet Sharma et al., “Improvement in Frictional Behaviour of SAE 15W40 Lubricant with the Addition of Graphite Particles,” Materials Today Proceedings, vol. 25, no. 4, pp. 719-723, 2020.
[CrossRef] [Google Scholar] [Publisher Link]
[11] Qin Dong et al., ”Simulation and Experimental Verification of Fatigue Strength Evaluation of Journal Bearing Bush,” Engineering Failure Analysis, vol. 109, 2020.
[CrossRef] [Google Scholar] [Publisher Link]
[12] Wenjie Zhou et al., “Research on the Lubricated Characteristics of Journal Bearing Based on Finite Element Method and Mixed Method,” Ain Shams Engineering Journal, vol. 13, no. 4, 2022.
[CrossRef] [Google Scholar] [Publisher Link]
[13] Lubos Smolik et al., “Comprehensive Analysis of Fluid Film Instability in Journal Bearings with Mechanically Indented Textures,” Journal of Sound and Vibration, vol. 546, 2023.
[CrossRef] [Google Scholar] [Publisher Link]
[14] Alexey V. Kornaev et al., “Enhanced Hydrodynamic Lubrication of Lightly Loaded Fluid-Film Bearings Due to the Viscosity Wedge Effect,” Tribology International, vol. 160, 2021.
[CrossRef] [Google Scholar] [Publisher Link]
[15] Jongin Yang, M. M. Khonsari, and Alan Palazzolo, “CFD Investigation of Oil-Free Granular Lubrication,” Tribology International, vol. 164, 2021.
[CrossRef] [Google Scholar] [Publisher Link]
[16] Bassam J. Alshaer, and Hamid M. Lankarani, “An Exact Analytical Solution for Dynamic Loads Generated by Lubricated Long Journal Bearings,” Mechanism and Machine Theory, vol. 183, 2023.
[CrossRef] [Google Scholar] [Publisher Link]
[17] Zhongliang Xie, Jian Jiao, and Stanislaw Wrona, “The Fluid-Structure Interaction Lubrication Performances of a Novel Bearing: Experimental and Numerical Study,” Tribology International, vol. 179, 2023.
[CrossRef] [Google Scholar] [Publisher Link]
[18] Shaoyu Zhu et al., “A Study of Misaligned Compliant Journal Bearings Lubricated by Non-Newtonian Fluid Considering Surface Roughness,” Tribology International, vol. 179, 2023.
[CrossRef] [Google Scholar] [Publisher Link]
[19] P. Chellapandi, and C. Lakhmana Rao, “Development and Application of a Numerical Analysis Method for Investigating Hydro Static and Hydrodynamic Responses of Pocket Bearing Rotor Systems,” Journal of Fluids and Structures, vol. 109, 2022.
[CrossRef] [Google Scholar] [Publisher Link]
[20] J. Bouyer, M. Wodtke, and M. Fillon, “Experimental Research on a Hydrodynamic Thrust Bearing with Hydrostatic Lift Pockets, Influence of Lubrication Modes on Bearing Performance,” Tribology International, vol. 165, 2022.
[CrossRef] [Google Scholar] [Publisher Link]
[21] Nino Dakov, “Elastohydrodynamic Lubrication Analysis of a Radial Oil Seal with Hydrodynamic Features,” Tribology International, vol. 173, 2022.
[CrossRef] [Google Scholar] [Publisher Link]
[22] Anil Singh, and Satish C. Sharma, “Behaviour of Conical Porous Hybrid Journal Bearing Operated with MHD Lubricant Considering Influence of Surface Irregularities,” Tribology International, vol. 174, no. 6, pp. 107730-107736, 2022.
[CrossRef] [Google Scholar] [Publisher Link]
[23] Hussein Sayed, and T. A. El-Sayed, “A Novel Method to Evaluate the Journal Bearing Forces with Application to Flexible Rotor Model,” Tribology International, vol. 173, no. 8, pp. 107593-107601, 2022.
[CrossRef] [Google Scholar] [Publisher Link]
[24] Long Zheng et al., “Numerical Simulation of Hydrodynamic Lubrication Performance for Continuous Groove-Textured Surface,” Tribology International, vol. 167, 2022.
[CrossRef] [Google Scholar] [Publisher Link]
[25] Shengbo Li et al., “Active Hybrid Journal Bearings with Lubrication Control: Towards Machine Learning,” Tribology International, vol. 175, 2022.
[CrossRef] [Google Scholar] [Publisher Link]
[26] Hussein Sayed, and T. A. El-Sayed, “Nonlinear Dynamics and Bifurcation Analysis of Journal Bearings Based on Second Order Stiffness and Damping Coefficients,” International Journal of Non-Linear Mechanics, vol. 142, 2022.
[CrossRef] [Google Scholar] [Publisher Link]
[27] Atulkumar S. Patil, Vishnu D. Wakchaure, and Uddhav M. Shirsat, “Experimental Investigation of Micro-Textured Piston Ring and Cylinder Liner Pair at Mid Stroke Operating Conditions,” International Journal of Engineering Trends and Technology, vol. 70, no. 10, pp. 381-392, 2022.
[CrossRef] [Publisher Link]
[28] Muhammad Imran Sadiq et al., “Investigation of Stiffness and Damping Coefficients in Fluid Film Bearing with Bio-Oils and MineralBased Oil,” Energy Reports, vol. 8, pp. 419-429, 2022.
[CrossRef] [Google Scholar] [Publisher Link]
[29] Shaswat Saincher et al., “Experimental Investigation of Hydrodynamic Loading Induced by Regular, Steep Non-Breaking and Breaking Focused Waves on a Fixed and Moving Cylinder,” European Journal of Mechanics - B/Fluids, vol. 93, pp. 42-64, 2022.
[CrossRef] [Google Scholar] [Publisher Link]
[30] N. S. C. Chaitanya, Y. V. V. Satyanarayana Murthy, and M. R. S. Satyanarayana, “Experimental Investigations on CI Engine for Performance, and Emissions Fuelled with Stabilised Binary Diesel/ JME Blends Doped with Nano Metallic Oxide Additive Particles using DEE, and Non- Ionic Surfactants,” International Journal of Engineering Trends and Technology, vol. 69, no. 8, pp. 161-173, 2021.
[CrossRef] [Publisher Link]
[31] Songlin Nie et al., “Failure Analysis of Auxiliary Support Bearing/Shaft Tribopair in Seawater Hydraulic Axial Piston Pump,” Engineering Failure Analysis, vol. 146, 2023.
[CrossRef] [Google Scholar] [Publisher Link]
[32] Huanhuan Wang et al., “Numerical Simulation on Hydrodynamic Lubrication Performance of Bionic Multi-Scale Composite Textures Inspired by Surface Patterns of Subcrenata and Clam Shells,” Tribology International, vol. 181, 2023.
[CrossRef] [Google Scholar] [Publisher Link]