Optimization of Bead Geometrics for GMAW-Based Wire Arc Additive Manufacturing Using 1.36 Cr-0.5 Mo Steel Metal-Cored Wires
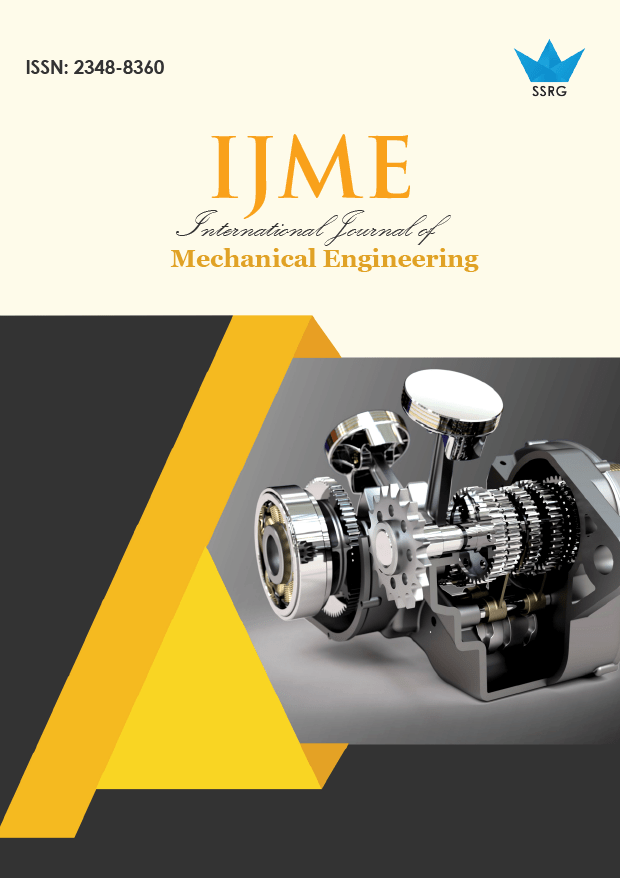
International Journal of Mechanical Engineering |
© 2025 by SSRG - IJME Journal |
Volume 12 Issue 4 |
Year of Publication : 2025 |
Authors : Prerna Shah, Vyomesh Buch, Jay Vora |
How to Cite?
Prerna Shah, Vyomesh Buch, Jay Vora, "Optimization of Bead Geometrics for GMAW-Based Wire Arc Additive Manufacturing Using 1.36 Cr-0.5 Mo Steel Metal-Cored Wires," SSRG International Journal of Mechanical Engineering, vol. 12, no. 4, pp. 82-108, 2025. Crossref, https://doi.org/10.14445/23488360/IJME-V12I4P108
Abstract:
Optimizing the process parameters to achieve optimal performance of gas metal arc welding technique of wire arc additive manufacturing using Metalloy 80B2 (1.00-1.50 percent chromium and 0.50 percent molybdenum steel), a gas-shielded metal-cored wire, was the main goal of the current investigation. Depth of penetration (DOP), bead height (BH), and bead width (BW) of bead deposition were examined in relation to changes in input parameters (voltage (22 to 26 V), travel speed (1 to 6 mm/s), and shielding gas composition (CO2-1%, 5%, and 9%). Utilizing the Box Behnken Designs, the set of input variables for the experiment was determined. The significance and sufficiency of the correlation derived from the experiment's results were confirmed through the use of fit statistics and ANOVA. In contrast, to travel speed for BH, the voltage was determined to be a more significant parameter for DOP and BW. Externally studentized residual plots for DOP, BH, and BW were examined, and the results showed that created correlations are legitimate and don't require transformation. The optimum outcomes from Stat-Ease 360 software: DOP = 1.320 mm, BH = 8.381 mm, BW = 8.687 mm for voltage = 26 V, travel speed = 10 mm/s, % of CO2 into gas mixture = 8.317% was achieved with 0.895 desirability. The experimental work for optimum input parameters was conducted and found within the range of results obtained from State Ease 360 software. Experimental results showed that the bead-on-bead material was placed uniformly in a multilayer structure, merged flawlessly, and did not disperse.
Keywords:
Metal cored wire, Low alloy steel, Wire arc additive manufacturing, Response surface methodology, Stat-Ease 360 Software.
References:
[1] Mohsen Attaran, “The Rise of 3-D Printing: The Advantages of Additive Manufacturing Over Traditional Manufacturing,” Business Horizons, vol. 60, no. 5, pp. 677-688, 2017.
[CrossRef] [Google Scholar] [Publisher Link]
[2] Nor Ana Rosli et al., “Review on Effect of Heat Input for Wire Arc Additive Manufacturing Process,” Journal of Materials Research and Technology, vol. 11, pp. 2127-2145, 2021.
[CrossRef] [Google Scholar] [Publisher Link]
[3] Ilbey Karakurt, and Liwei Lin, “3D Printing Technologies: Techniques, Materials, and Post-Processing,” Current Opinion in Chemical Engineering, vol. 28, pp. 134-143, 2020.
[CrossRef] [Google Scholar] [Publisher Link]
[4] Vishal Kumar, Deepti Ranjan Sahu, and Amitava Mandal, “Parametric Study and Optimization of GMAW based AM Process for Multi layer Bead Deposition,” Materials Today: Proceedings, vol. 62, pp. 255-261, 2022.
[CrossRef] [Google Scholar] [Publisher Link]
[5] Cleber Marques et al., “Analysis of the Solid Wire Dip in the GMAW-CMT Melting Pool as a Means for Enhancing Additive Manufacturing,” Journal of the Brazilian Society of Mechanical Sciences and Engineering, vol. 45, 2023.
[CrossRef] [Google Scholar] [Publisher Link]
[6] Jayaprakash Sharma Panchagnula, and Suryakumar Simhambhatla, “Manufacture of Complex Thin-Walled Metallic Objects using Weld Deposition based Additive Manufacturing,” Robotics and Computer-Integrated Manufacturing, vol. 49, pp. 194-203, 2018.
[CrossRef] [Google Scholar] [Publisher Link]
[7] Junbiao Shi et al., “Effect of In-Process Active Cooling on Forming Quality and Efficiency of Tandem GMAW–based Additive Manufacturing,” The International Journal of Advanced Manufacturing Technology, vol. 101, pp. 1349-1356, 2019.
[CrossRef] [Google Scholar] [Publisher Link]
[8] Philipp Henckell et al., “In Situ Production of Titanium Aluminides during Wire Arc Additive Manufacturing with Hot-Wire Assisted GMAW Process, Metals, vol. 9, no. 5, pp. 1-13, 2019.
[CrossRef] [Google Scholar] [Publisher Link]
[9] Philipp Henckell et al., “Reduction of Energy Input in Wire Arc Additive Manufacturing (WAAM) with Gas Metal Arc Welding (GMAW),” Materials, vol. 13, no. 11, pp. 1-18, 2020.
[CrossRef] [Google Scholar] [Publisher Link]
[10] Ashish Kumar, and Kuntal Maji, “Selection of Process Parameters for Near-Net Shape Deposition in Wire Arc Additive Manufacturing by Genetic Algorithm,” Journal of Materials Engineering and Performance, vol. 29, pp. 3334-3352, 2020.
[CrossRef] [Google Scholar] [Publisher Link]
[11] C.H. Bharat Kumar, and V. Anandakrishnan, “Experimental Investigations on the Effect of Wire Arc Additive Manufacturing Process Parameters on the Layer Geometry of Inconel 825,” Materials Today: Proceedings, vol. 21, pp. 622-627, 2020.
[CrossRef] [Google Scholar] [Publisher Link]
[12] Justin Baby, and Murugaiyan Amirthalingam, “Microstructural Development during Wire Arc additive Manufacturing of Copper-based Components,” Welding in the World, vol. 64, pp. 395-405, 2020.
[CrossRef] [Google Scholar] [Publisher Link]
[13] Adam M. Pringle et al., “Open Source Arc Analyzer: Multi-Sensor Monitoring of Wire Arc Additive Manufacturing,” Hardware, vol. 8, pp. 1-23, 2020.
[CrossRef] [Google Scholar] [Publisher Link]
[14] E. Aldalur, A. Suárez, and F. Veiga, “Metal Transfer Modes for Wire Arc Additive Manufacturing Al-Mg Alloys: Influence of Heat Input in Microstructure and Porosity,” Journal of Materials Processing Technology, vol. 297, 2021.
[CrossRef] [Google Scholar] [Publisher Link]
[15] Wenyong Zhao et al., “Modeling and Simulation of Heat Transfer, Fluid Flow and Geometry Morphology in GMAW-based Wire Arc Additive Manufacturing,” Welding in the World, vol. 65, pp. 1571-1590, 2021.
[CrossRef] [Google Scholar] [Publisher Link]
[16] Rama Kishore Mookara et al., “Influence of Droplet Transfer Behaviour on the Microstructure, Mechanical Properties and Corrosion Resistance of Wire Arc Additively Manufactured Inconel (IN) 625 Components,” Welding in the World, vol. 65, pp. 573-588, 2021.
[CrossRef] [Google Scholar] [Publisher Link]
[17] Reyazul Warsi, and Kashif Hasan Kazmi, and Mukesh Chandra, “Mechanical Properties of Wire and Arc Additive Manufactured Component Deposited by a CNC Controlled GMAW,” Materials Today: Proceedings, vol. 56, pp. 2818-2825, 2022.
[CrossRef] [Google Scholar] [Publisher Link]
[18] Vishal Kumar et al., “Parametric Study and Characterization of Wire arc Additive Manufactured Steel Structures,” The International Journal of Advanced Manufacturing Technology, vol. 115, pp. 1723-1733, 2021.
[CrossRef] [Google Scholar] [Publisher Link]
[19] Teresa Artaza et al., “Wire Arc Additive Manufacturing Ti6al4v Aeronautical Parts using Plasma Arc Welding: Analysis of Heat Treatment Processes in Different Atmospheres,” Journal of Materials Research and Technology, vol. 9, no. 6, pp. 15454-15466, 2020.
[CrossRef] [Google Scholar] [Publisher Link]
[20] M.J. Bermingham et al., “High Strength Heat-treatable β-titanium Alloy for Additive Manufacturing,” Materials Science and Engineering: A, vol. 791, 2020.
[CrossRef] [Google Scholar] [Publisher Link]
[21] Rui Fu et al., “Large-size Ultra-High Strength-Plasticity Aluminum Alloys Fabricated by Wire arc Additive Manufacturing via Added Nanoparticles,” Materials Science and Engineering: A, vol. 864, 2023.
[CrossRef] [Google Scholar] [Publisher Link]
[22] Maximilian Gierth et al., “Wire Arc Additive Manufacturing (WAAM) of Aluminum Alloy AlMg5Mn with Energy-Reduced Gas Metal Arc Welding (GMAW),” Materials, vol. 13, no. 12, pp. 1-22, 2020.
[CrossRef] [Google Scholar] [Publisher Link]
[23] Angela Dean, Daniel Voss, and Danel Draguljić, Response Surface Methodology, Design and Analysis of Experiments, 2nd ed., Springer Cham, pp. 565-614, 2017.
[CrossRef] [Google Scholar] [Publisher Link]
[24] André I. Khuri, and Siuli Mukhopadhyay, “Response Surface Methodology,” WIREs Computational Statistics, vol. 2, no. 2, pp. 128-149, 2010.
[CrossRef] [Google Scholar] [Publisher Link]