Fatigue Life Prediction under Thermomechanical Loading in Cracked Structures: A Unified Approach
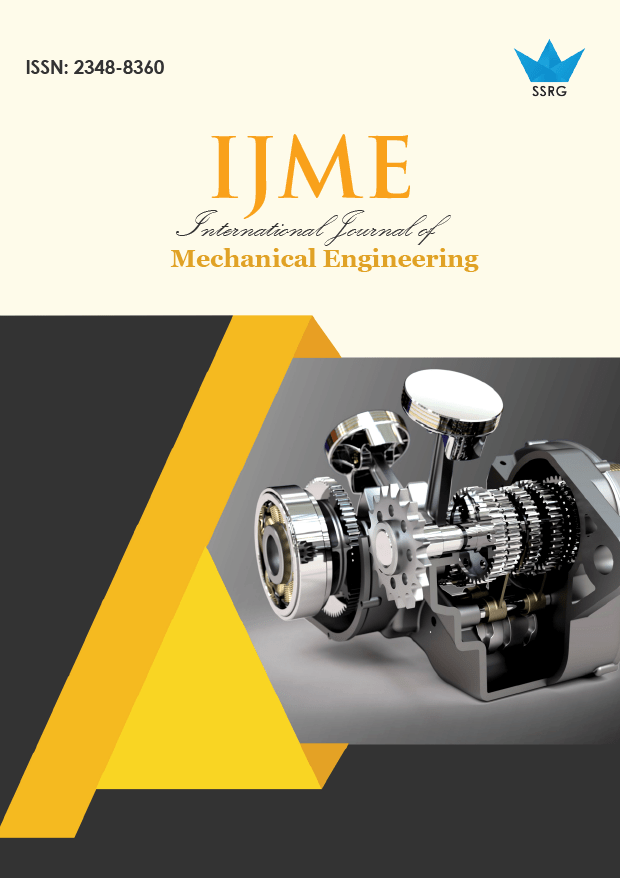
International Journal of Mechanical Engineering |
© 2025 by SSRG - IJME Journal |
Volume 12 Issue 4 |
Year of Publication : 2025 |
Authors : Otmane Aboulhassane, Abdelhadi El Hakimi, Abderrahim Chamat, Abdelhamid Touache |
How to Cite?
Otmane Aboulhassane, Abdelhadi El Hakimi, Abderrahim Chamat, Abdelhamid Touache, "Fatigue Life Prediction under Thermomechanical Loading in Cracked Structures: A Unified Approach," SSRG International Journal of Mechanical Engineering, vol. 12, no. 4, pp. 109-116, 2025. Crossref, https://doi.org/10.14445/23488360/IJME-V12I4P109
Abstract:
This study examines crack damage resulting from thermomechanical loading in tubular heat exchanger components, a vital concern for the safety and longevity of industrial facilities. The foundational concepts of fracture mechanics examine fatigue crack propagation mechanisms, emphasizing the characterization of stress fields at the crack tip via the stress intensity factor (K) and the J-integral. Focus is directed towards a comprehensive methodology for predicting fatigue life, namely empirical models based on Paris' rule and its adaptations, including the Elber, Tomkins, and Solomon-Skelton models, which additionally assess crack growth rates in relation to cyclic loading amplitude. A finite element numerical model is created to evaluate fracture propagation in a cracked tube under combined thermal and mechanical loading in real-world conditions. The research investigates the effects of temperature (300°C and 550°C), mechanical load, and the interplay between these factors on the kinetics of semi-elliptical crack propagation. The numerical results are subsequently checked with experimental data from the literature to verify the accuracy of the predictions. This comparison underscores the advantages and drawbacks of standard analytical models, especially concerning the impact of thermomechanical effects on the fatigue life of cracked structures.
Keywords:
Damage, J-integral, Paris' law, Stress Intensity Factor (SIF), Material behavior law, Stainless steel, 316L, Heat exchanger.
References:
[1] Elena Paffumi, Karl-Fredrik Nilsson, and Zoltan Szaraz, “Experimental and Numerical Assessment of Thermal Fatigue in 316 Austenitic Steel Pipes,” Engineering Failure Analysis, vol. 47, pp. 312-327, 2015.
[CrossRef] [Google Scholar] [Publisher Link]
[2] P. Paris, “A Rational Analytic Theory of Fatigue,” Trends Engineering, vol. 13, pp. 9-14, 1961.
[Google Scholar] [Publisher Link]
[3] Wolf Elber, “Fatigue Crack Closure under Cyclic Tension,” Engineering Fracture Mechanics, vol. 2, no. 1, pp. 37-45, 1970.
[CrossRef] [Google Scholar] [Publisher Link]
[4] B. Tomkins, “Fatigue Crack Propagation-An Analysis,” The Philosophical Magazine: A Journal of Theoretical Experimental and Applied Physics, vol. 18, no. 155, pp. 1041-1066, 1968.
[CrossRef] [Google Scholar] [Publisher Link]
[5] Jaehoon Sim, Hyoin Lee, and Ji Hwan Jeong, “Optimal Design of Variable-Path Heat Exchanger for Energy Efficiency Improvement of Air-Source Heat Pump System,” Applied Energy, vol. 290, 2021.
[CrossRef] [Google Scholar] [Publisher Link]
[6] P. Paris, and F. Erdogan “A Critical Analysis of Crack Propagation Laws,” Journal of Basic Engineering, vol. 85, no. 4, pp. 528-533, 1963.
[CrossRef] [Google Scholar] [Publisher Link]
[7] H. Huthmann, and C. Picker, “Behaviour of Short Fatique Cracks in Austenitic Stainless Steels: Literature Review,” Final Report, Office for Official Publications of the European Communities, 1995.
[Google Scholar]
[8] R.P. Skelton, “High Strain Fatigue of 20Cr/25Ni/Nb Steel at 1025 K Part III: Crack Propagation,” Materials Science and Engineering, vol. 19, no. 2, pp. 193-200, 1975.
[CrossRef] [Google Scholar] [Publisher Link]
[9] HD Solomon, “Low Cycle Fatigue Crack Propagation in 1018 Steel,” Journal of Materials, vol. 7, pp. 299-306, 1972.
[Google Scholar]
[10] C. Bathias, and A. Pineau, Fatigue of Materials and Structures: Application to Design and Damage, ISTE/Hermes Science Publishing, pp. 1-512, 2008.
[Google Scholar] [Publisher Link]
[11] Bruce Alexander Bilby et al., “Plastic Yielding from Sharp Notches, Proceedings of the Royal Society of London Series A. Mathematical and Physical Sciences, vol. 279, no. 1376, pp. 1-9, 1964.
[CrossRef] [Google Scholar] [Publisher Link]
[12] Campbell Laird, The Influence of Metallurgical Structure on the Mechanisms of Fatigue Crack Propagation, ASTM International, pp. 1-50, 1967.
[CrossRef] [Google Scholar] [Publisher Link]
[13] R.M.N. Pelloux, “Mechanisms of Formation of Ductile Fatigue Striations,” American Society for Metals Transactions, vol. 62, pp. 281-285, 1969.
[Google Scholar]
[14] J.R. Rice, “A Path Independent Integral and the Approximate Analysis of Strain Concentration by Notches and Cracks,” Journal of Applied Mechanics, vol. 35, no. 2, pp. 379-386, 1968.
[CrossRef] [Google Scholar] [Publisher Link]
[15] J.D. Eshelby, “The Elastic Energy-Momentum Tensor,” Journal of Elasticity, vol. 5, pp. 321-335, 1975.
[CrossRef] [Google Scholar] [Publisher Link]
[16] N.E. Dowling, and J. A. Begley, Fatigue Crack Growth during Gross Plasticity and the J-Integral, Mechanics of Crack Growth, pp. 1 22, 1976.
[CrossRef] [Google Scholar] [Publisher Link]
[17] E. Paffumi et al., “Crack Initiation, Propagation, and Arrest in 316L Model Pipe Components under Thermal Fatigue,” Journal of ASTM International, vol. 2, no. 5, pp. 1-18, 2005.
[CrossRef] [Google Scholar] [Publisher Link]