Decreasing Machine Down Time by Enhancing Existing Preventive Maintenance System
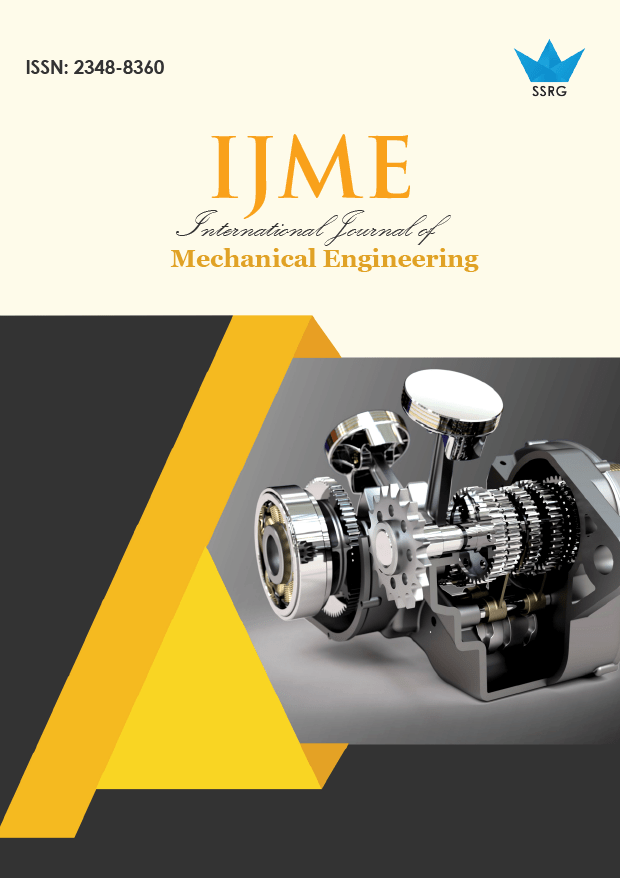
International Journal of Mechanical Engineering |
© 2020 by SSRG - IJME Journal |
Volume 7 Issue 6 |
Year of Publication : 2020 |
Authors : Temesgen Hailegiorgis Abebe |
How to Cite?
Temesgen Hailegiorgis Abebe, "Decreasing Machine Down Time by Enhancing Existing Preventive Maintenance System," SSRG International Journal of Mechanical Engineering, vol. 7, no. 6, pp. 33-40, 2020. Crossref, https://doi.org/10.14445/23488360/IJME-V7I6P106
Abstract:
This article aims to allow Minota Metalworks and Manufacturing share company in Sodo city. Ethiopia to achieve preventive Maintenance scheduling involves functional checks, repairing or replacing necessary devices, machinery, and supporting utilities in industrial and governmental installations. Maintenance is keeping something in good condition and the process of continuing something or keep it in existence. However, the company has faced high machine downtime caused by poor maintenance practice and leads the company to low productivity. Preventive maintenance is maintenance performed to avoid failures, safety violations, and unnecessary tasks to keep something such as a building, machine, or piece of equipment required and in production costs and losses. This article is conducted on Minota Metalworks and Manufacturing company to improve preventive maintenance (PM) scheduling and develop accidental budget planning for the maintenance department to enhance productivity. To address such a problem, this article mainly includes calculation and explanation. It also presents the company's existing problem and finally provides a solution by preparing an improved maintenance schedule to enhance the company loss due to poor preventive schedule practice.
Keywords:
ECU, Mean down time, preventive maintemance, PM scheduling, MTBF
References:
[1] Preventive Maintenance (PM) planning: a review, Journal of quality in maintenance engineering, 23( 2) .
[2] The reason, J., Cognitive Engineering in Aviation Domain, Lawrence Erlbaum Associates, Mahwah, NJ, (2000).
[3] Ab-Samat, H., Jeikumar, L.N., Basri, EI, Harun, NA, and Kamaruddin., Effective preventive maintenance scheduling: a case study, Proceedings of the 2012 International Conference on Industrial Engineering and Operations Management, July 3-6, Istanbul, Turkey, (2012) 1249 – 1257.
[4] Ahmed. S, Hassan, M. and Taha, Z, TPM Can Go Beyond Maintenance – Excerpt From A Case Implementation, Journal of Quality in Maintenance Engineering, 11(1) , (2005) 19-42.
[5] Dekker, R,Integrating optimization, priority setting, planning, and combining of maintenance activities. European Journal of Operational Research, 82 (2), (1995) 225 – 240.
[6] Duffuaa, S. O, Raouf, A. and Campbell, J., Planning, and Control of Maintenance Systems: Modelling and Analysis. John Wiley & Sons, Inc, New York. Fitouhi, C. M. and Nourelfath, M. (2014) Integrating noncyclical preventive maintenance scheduling and production planning for multi-state systems, Reliability Engineering and System Safety, 121 (1999) 175–186,.
[7] Khan, F. I., and Haddara, M.M., Risk-based maintenance (RBM): a quantitative approach for maintenance/inspection scheduling and planning. Journal of Loss Prevention in the Process Industries, 16 (6) (2003) 561 – 573.
[8] Muath Al-Falahi, Tang Sai Hong and Monaaf D.A. Al-Falahi, Reliability-based Maintenance Planning Methods in Power Industry: A Review, SSRG International Journal of Industrial Engineering 3(2) (2016) 8-12.
[9] Nakajima, S, TPM – challenge to the improvement of productivity by small group activities. Maintenance Management International, .6 (1986) 73 – 83.
[10] Kobbacy, K.A.H., Percy, D.F. and Fawzi, B.B., Small data sets, and preventive maintenance modeling. Journal of Quality in Maintenance Engineering, 3(2), (1997) 136 – 142,
[11] Doc palmer., Maintenance planning, and scheduling Hand Book: MC Graw-hill, New York, (1999).
[12] Lindley, R.H, Maintenance Engineering Hand Book: 5th Ed, MC Graw-hill, New York, (1995).
[13] Dhillo, B. S, Engineering Maintenance, a Modern Approach: CRC pre, Ney York, (2002).
[14] Kimura, Y., Maintenance Tribology: its significance and activity in Japan. Wear, 207 No.1-2, 63-66, 1997.