Electro Chemical and Mechanical Studies on Epoxy Coated Rebars in Marine Environment
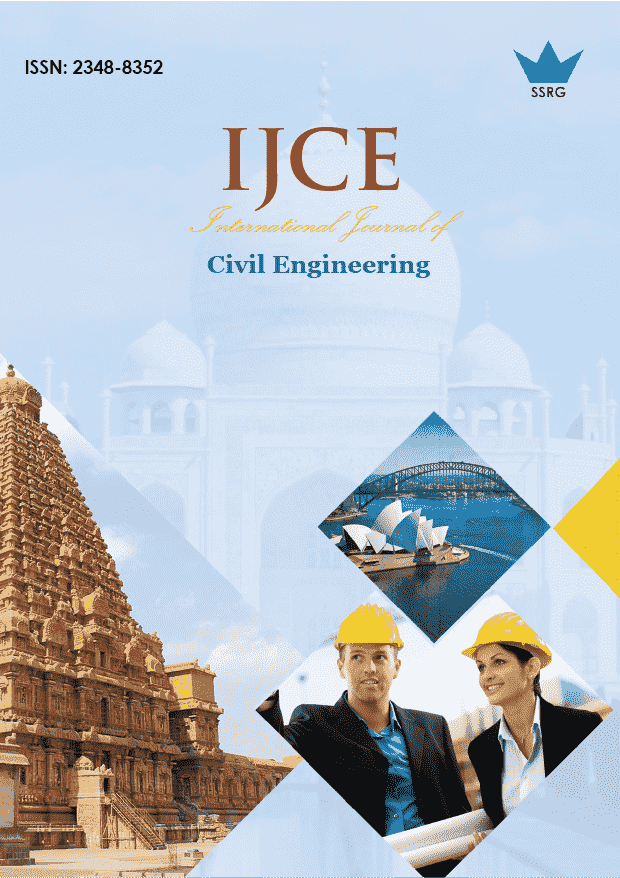
International Journal of Civil Engineering |
© 2017 by SSRG - IJCE Journal |
Volume 4 Issue 5 |
Year of Publication : 2017 |
Authors : Sindhu. R, Preethiwini. B, Sudhan Nayak Raj. S. P |
How to Cite?
Sindhu. R, Preethiwini. B, Sudhan Nayak Raj. S. P, "Electro Chemical and Mechanical Studies on Epoxy Coated Rebars in Marine Environment," SSRG International Journal of Civil Engineering, vol. 4, no. 5, pp. 70-74, 2017. Crossref, https://doi.org/10.14445/23488352/IJCE-V4I5P125
Abstract:
Corrosion is a natural process, which converts refined metal to a more stable form such as its oxide, hydroxide, or sulfide. It is the gradual destruction of materials by chemical and electrochemical reaction with their environment. In order to prevent the corrosion of steel in concrete a number of protection techniques such as coatings to steel, coatings to concrete, cathodic protection, addition of super plasticizers, electrochemical removal of chloride, desalination, electrochemical realkalization and corrosion inhibiting admixtures is identified. Based on literature study rebar coating is found to be effective and economic. An experimental study was conducted to analyze the corrosion resistant property of Coal Tar Epoxy in marine environment. The rebars are subjected to chemical and electrochemical studies such as cathodic disbondment, accelerated corrosion and impressed voltage tests to analysis the effectiveness of coating. The mechanical properties of the coated rebars is analyzed by pull out test. The above test results indicated an appreciable adhesion and corrosion resistant property of Coal Tar Epoxy coating even under aqueous environment of 3.5% NaCl.
Keywords:
Corrosion, Coal Tar Epoxy, Electrochemical studies, Accelerated Corrosion, Cathodic Disbondment, Impressed Voltage.
References:
[1] Alan Kehr J. and Fikry F. Barouky (2006), ‘Fusion Bonded Epoxy coatings a technology for rebar corrosion’, Surf. Coat. Technol., 2006, 201, 3701–3708.
[2] Batis G., Pantazopoulou P. and Routoulas A. (2003), ‘Corrosion protection investigation of reinforcement by inorganic coating in the presence of alkanolamine-based inhibitor’, Cement and Concrete Composites, Vol. 25, pp.371– 377.
[3] Brian D. Chambers, S. Ray Taylor and D. Stephen Lane (2003), ‘An Evaluation of New Inhibitors for Rebar Corrosion in Concrete’, Virginia Transportation Research Council, Charlottesville.
[4] Enrique Vaca-Cortes, Miguel A. Lorenzo, James O. Jirsa, Harovel G. Wheat and Ramon L. Carrasquillo (1998), ‘Adhesion Testing of Epoxy Coating’, Texas Department of Transportation, No. 1265-6, pp. 1-115.
[5] IS:13620-1993 ‘Indian Standard for Fusion Bonded Epoxy coated reinforcing bars- specification’, Bureau of Indian Standards, New Delhi.
[6] Kingsley Lau and Alberto A. Sagues (2009), ‘Corrosion of Epoxy and Polymer/Zinc Coated Rebar in Simulated Concrete Pore Solution’, National Convention on Corrosion conf. and expo, pp. 09207.
[7] M. S. Shetty (2013), ‘Concrete Technology’, S. Chand and Company Pvt. Ltd. New Delhi.
[8] Mangaiyarkarasi G. and Muralidharan S. (2014), ‘Electrochemical Protection of Steel in Concrete to Enhance the Service Life of Concrete Structures’, Procedia Engineering, Vol. 86, pp. 615 – 622.
[9] Markus Betz, Christoph Bosch, Peter-Josef Gronsfeld, Marina Bagaviev, Ulrich Smit and Rainer Grabowski (2012), ‘Cathodic Disbondment Test’, National Convention on Corrosion conf. and expo, No. 0001285.
[10] Saraswathy V. and Karthick S. P. (2014), ‘Effect of ecofriendly sealing coat against corrosion protection of steel rebars in concrete’, Corrosion Engineering, Science and Technology, Vol. 49, No. 5, pp.327- 334.
[11] Saravanan K., Sathiyanarayanan S., Muralidharan S., Syed Azim S. and Venkatachari G. (2007), ‘Performance evaluation of polyaniline pigmented epoxy coating for corrosion protection of steel in concrete environment’, Progress in Organic Coatings, Vol. 59, pp.160–167.
[12] Theodosia Zafeiropoulou, Eleni in reinforced cement mortars’, Progress in Organic Coatings, Vol. 72, pp.175– 180.