Experimental and FEA for stress, fatigue life and optimum weight of LCV leaf spring
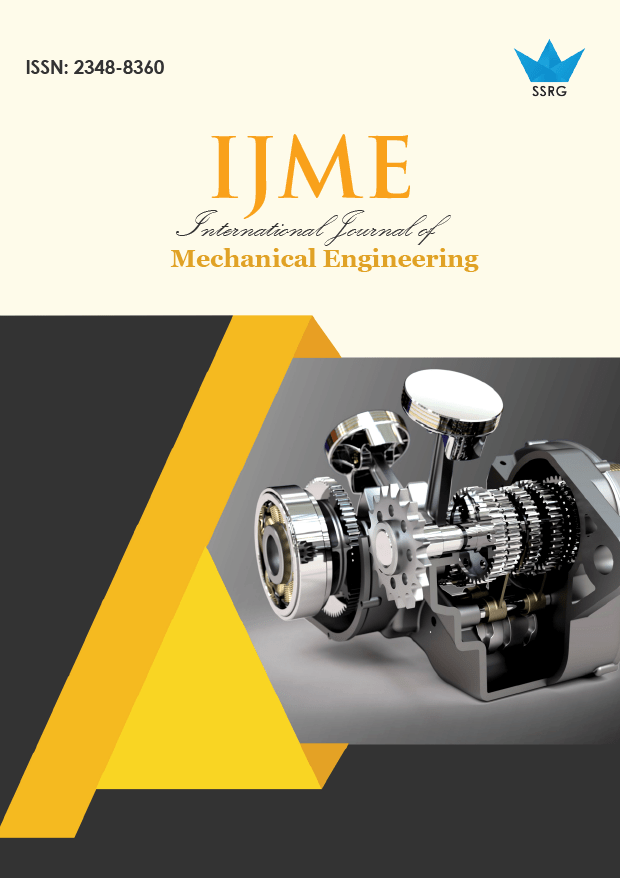
International Journal of Mechanical Engineering |
© 2017 by SSRG - IJME Journal |
Volume 4 Issue 9 |
Year of Publication : 2017 |
Authors : Vikas K. Joshi, Dr.Rachayya R. Arakerimath |
How to Cite?
Vikas K. Joshi, Dr.Rachayya R. Arakerimath, "Experimental and FEA for stress, fatigue life and optimum weight of LCV leaf spring," SSRG International Journal of Mechanical Engineering, vol. 4, no. 9, pp. 21-27, 2017. Crossref, https://doi.org/10.14445/23488360/IJME-V4I9P105
Abstract:
In this paper, a leaf spring with auxiliary spring is tested for its fatigue life and stiffness. The existing design is with both multi-leaf type springs whereas the modified design consists of auxiliary parabolic spring to have a increased fatigue life by reducing stress levels. The leaf spring is being tested for its targeted life of 1x105 and 5x104 fatigue cycles for main and auxiliary leaf springs respectively. All analytical calculations for the said leaf spring for its stiffness and fatigue life has been done by using SAE manual. Also, FEA for fatigue life and stiffness has been done by using Pro-Mechanica software. The experimental investigation is carried out on a leaf spring test rig with a maximum load of 12730 kg allowing maximum deflection of 146mm and maximum stresses up to 100kg/mm2. To increase the fatigue life of a leaf spring, leaves of the spring tension side is shot peened. Now in new leaf spring, main leaf spring consists of 9 leaves whereas auxiliary parabolic leaf spring consists of 3 leaves. The factor of safety for leaf spring is between the ranges 1.2 to 1.5. By using parabolic leaf spring on auxiliary pack, the weight of the leaf spring has been reduced by 43 Kg i.e. from 177 Kg (Existing) to 134 Kg (New) and approximately 24% weight is reduced per leaf spring. All the results i.e. analytical, FEA and experimental are compared in results and discussion.
Keywords:
Leaf spring, main spring, auxiliary spring, FEA, test rig, weight reduction and parabolic leaf spring
References:
[1] T.N.V.Ashok Kumar,E.Venkateswara Rao, S.V.Gopal KrishnaDesign and Material Optimization of Heavy Vehicle Leaf Spring IJRMET Vol. 4,Issue Spl – 1, Nov 2013 – April 2014.
[2] Malaga. Anil Kumar, T.N.Charyulu, Ch.Ramesh Design Optimization of Leaf Spring IJERA Vol.2, Issue 6, Nov.- Dec. 2012, pp. 759-756.
[3] Dhiraj K Bhandarkar, Sanjay P. Shekhawat Design, Analysisand Optimization of Leaf Spring IJIRSET Vol. 3, Issue 6, June 2014.
[4] Edward Nikhil Karlus, Rakesh L. Himte, Ram Krishna Rathore Optimization of Mono Parabolic Leaf Spring IJAET Vol. 7, Issue 1, pp.283-291.
[5] Kaveri A. Katake, S. H. Mankar, Samir J. Deshmukh A Review on Design and Optimization of Composite Leaf Spring IJIERE Vol. 2, Special Issue 1 MEPCON 2015.
[6] Yohannes Regassa, R. Srinivasa Moorthy & Ratnam Uppala Failure Analysis of Semi-elliptical Master Leaf Spring of Passenger Car using Finite Element Method GJREM & ME Vol. 13 , Issue 2, Version 1.0 Year 2013.
[7] Ajinkya Mahadev Mahajan, A. P. Shrotri, Swapnil Kulkarni Fatigue Failure Analysis & Validation of Mono Leaf Spring Design IJAERS E-ISSN2249–8974.
[8] Ajay B.K, Mandar Gophane, P.Baskar Design and Analysis of Leaf Spring with Different Arrangements of Composite Leaves with Steel Leaves National Journal on Advances in Building Sciences and Mechanics Vol.6, No.1.
[9] N.S. Mendhe, Dr.S.A. Sonawane, Prof.K.C. Rajapurkar Experimental Study and Optimization of Leaf Spring IJERT Vol. 4 Issue 01 Jan 2015.
[10] Vinkel Kumar Arora, Gian Bhushan, and M.L.Agarwal Fatigue Life Assessment of 65Si7 Leaf Spings: A Comparative Study Hndawi Publshing Corporation International Scholarly Research Notices Vol. 2014, Article ID607272,11Pages.
[11] R.B. Charde, Dr. D.V. Bhope Investigation of Stresses in Master Leaf of Leaf Spring by FEM and its Experimental Verification IJEST Vol.4 No.02 Feb 2012.
[12] S.Rajesh and G.B. Bhaskar Experimental Investigation on Laminated Composite Leaf Springs subjected to Cyclic Loading IJET Vol.6 No.1 Feb-Mar 2014.