Finite Element Analysis and Mechanical Testing of Friction Stir Processed Low carbon Steel Plate
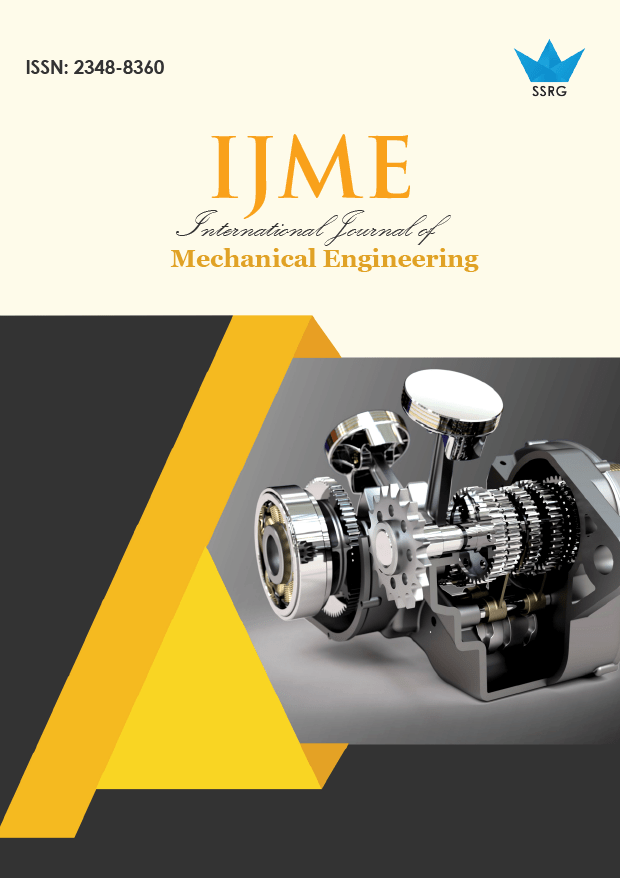
International Journal of Mechanical Engineering |
© 2016 by SSRG - IJME Journal |
Volume 3 Issue 8 |
Year of Publication : 2016 |
Authors : Gaurav S. Patil, N. V. Satpute |
How to Cite?
Gaurav S. Patil, N. V. Satpute, "Finite Element Analysis and Mechanical Testing of Friction Stir Processed Low carbon Steel Plate," SSRG International Journal of Mechanical Engineering, vol. 3, no. 8, pp. 16-20, 2016. Crossref, https://doi.org/10.14445/23488360/IJME-V3I8P103
Abstract:
Friction stir process is a solid state technology with increasing applications in the context of localized surface engineering. FSP has been investigated mainly for producing fine grained coatings, which exhibit superior wear and corrosion properties. Since no bulk melting takes place, this process allows dissimilar joining of materials that would be otherwise incompatible or difficult to deposit by fusion based methods. Main applications include surface properties improvement and coating. A wide range of material combinations have been deposited by FSP, mainly alloy and stainless steels. Aluminium, magnesium and titanium alloys have also been investigated, including the production of metal matrix composites. In this report coating of AISI 304 stainless steel powders was used as coating material and it is applied on low carbon steel. For above coating purpose we use non-consumable W C tool. The main process parameters are Tool RPM, Normal force, travel speed. In this report thermal model is made by using moving co-ordinate system in order to get temperature distribution across plate. This temperature data from FEA is used as input to the further analytical calculations. Free- Free vibration analysis is done on the steel plate and Zinc coated plate and natural frequencies are extracted. Stress analysis of steel plate and Zinc coated plate is done using experimentally and FEA. Bend test and Wear test is performed on Steel plate and Zinc coated plate.
Keywords:
FSP, Low Carbon Steel, AISI 304 Stainless steel, Bend Test, Wear Test, Modal Analysis.
References:
1. JinwenQian, ‗In situ synthesizing Al3Ni for fabrication of intermetallic-reinforced aluminum alloy composites by FSP‘, Materials Science & Engineering A, vol. 279 -285.
2. Ahmad Ghasemi-Kahrizsangi, ‗Microstructure and mechanical properties of steel/TiC nano-composite surface layer produced by FSP‘, Suraface and Coating Tchnlogy, vol. 462, 2007.
3. R.S. Mishra, ‗Friction stir processing: a novel technique for fabrication of surface composite‘, Materials Science and Engineering A341 (2003) 307/310
4. D.Dhmadkhaniha, M. HeydarzadehSohi, A. Zarei-Hanzaki, S.M. Bayazid, M. Saba. ―Taguchi optimization of process parameters in friction stir processing of pure Mg‖, Journal of Magnesium and Alloys 3 (2015) 168-172.
5. H Schmidt, J. Hattel and J Wert, An analytical model for the heat generation in friction stir welding, Modelling Simul. Mater. Sci. Eng. 12 (2004) 143–157.
6. R. Nandan, G.G. Roy, T.J. Lienert, T. Debroy, Threedimensional heat and material flow during friction stir welding of mild steel, ActaMaterialia 55 (2007) 883–895.
7. A. Arora,R. Nandan,A.P. Reynolds and T. DebRoy, Torque, power requirement and stir zone geometry in friction stir welding through modelling and experiments, ScriptaMaterialia 60 (2009) 13–16.
8. A. Arora, T. DebRoy, H.K.D.H. Bhadeshia, Back-of-theenvelope calculations in friction stir welding – Velocities, peak temperature, torque, and hardness, ActaMaterialia 59 (2011) 2020–2028.
9. J.H. Hattel, H.N.B. Schmidt and C. Tutum, Thermo mechanical Modelling of Friction Stir Welding, Stan A. David, TarasankarDebRoy, John N. DuPont, Toshihiko Koseki, Herschel B. Smartt, editors, p 1-10.
10. Y. Katayama, M. Takahashi, T. Shinoda, New friction surfacing application for stainless steel pipe, Welding in the World, Vol. 53, 11/12, 2009.