Design of Roll Forming Mill
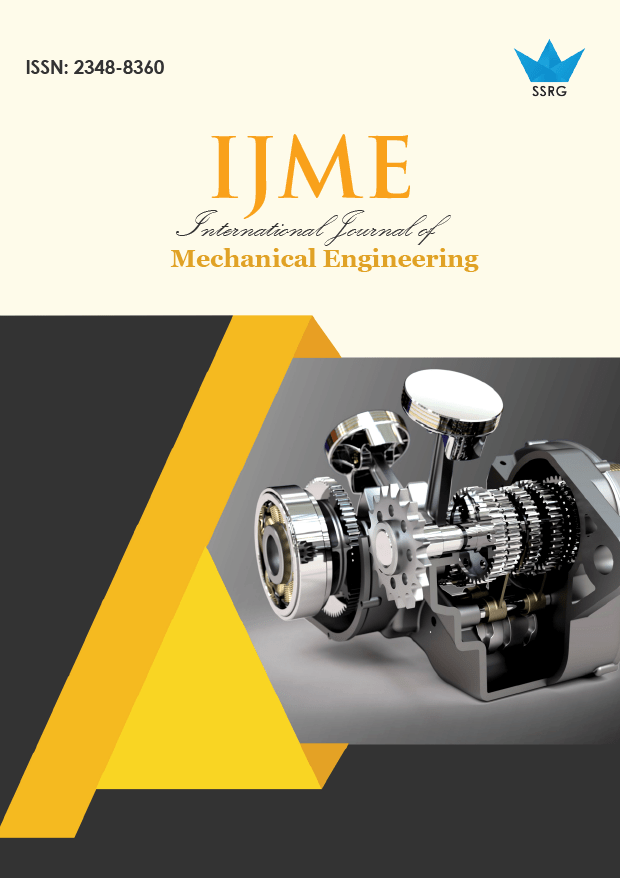
International Journal of Mechanical Engineering |
© 2021 by SSRG - IJME Journal |
Volume 8 Issue 4 |
Year of Publication : 2021 |
Authors : Kondusamy V, Jegatheeswaran D, Vivek S, Vidhuran D, Harishragavendra A |
How to Cite?
Kondusamy V, Jegatheeswaran D, Vivek S, Vidhuran D, Harishragavendra A, "Design of Roll Forming Mill," SSRG International Journal of Mechanical Engineering, vol. 8, no. 4, pp. 1-19, 2021. Crossref, https://doi.org/10.14445/23488360/IJME-V8I4P101
Abstract:
Sheet metal forming is widely used by the industries in the current scenario. Bending, Spinning, Deep drawing, Stretch forming & Roll forming is the major sheet metal forming processes. In this, roll forming is a unique continuous forming process, where 2D sheet metal is formed into various profiles like Rooftops, Window frames, Storage columns, etc., by using series of mated rollers. This project focuses on design considerations of roll forming tools and process parameters for a roll forming line. This design consideration discusses certain issues in the design of the roll forming tool, which includes Unfold length calculation, Flower pattern design, and Roller design by using an analytical solution. The constant bend allowance (arc) method of flower patterning was used to find the dimensions for the 2D die design. This dimension includes web length, flange length, and radius at each bend for both upper and lower roller. The roller design includes the proper shaft selection, key & keyway selection. This design was done based on force calculation. Major forces are considered to find the torque and bending moment.
Keywords:
Bending, Spinning, Deep drawing, stretch forming, Roll forming, Stretch forming, Hydroforming, Explosive forming, K – factor, Bend allowance and deduction, Unfold length, Bending moment, Rolling friction, Spring back force, Flower pattern.
References:
[1] Michael Lindgren., Experimental and Computational Investigation of the Roll Forming Process, ISSN: 1402-1544 ISBN 978-91-7439-031-5, Lulea university of technology, (2009).
[2] Chuck Summerhill., The basics of roll forming tool design, TPJ – The tube & pipe journal, March, (2003).
[3] John Paralikas ., Konstantinos Salonitis & George Chryssolouris, Optimization of roll forming process parameters—a semi-empirical approach, Int J Adv. Manuf. Tech, 47 (2010) 1041–1052.
[4] R. Safdarian, H.MoslemiNaeini., The effects of forming parameters on the cold roll forming of channel section, Thin-WalledStructures, 92 (2015) 130–136.
[5] Q.V. Bui, J.P. Ponthot., Numerical simulation of cold roll-forming processes, Journal of materials processing technology, 202 (2008) 275–282.
[6] A.Abvabi, B.Rolfe, P.D.Hodgson, M.Weiss., The influence of residual stress on a roll forming process, International Journal of Mechanical Sciences, 101-102 (2015)124–136.
[7] Christian Mueller, Xun Gu, Lars Baeumer, Peter Groche., Influence of friction on the loads in a roll forming simulation with compliant rolls, Key Engineering Materials, 611-612 (2014) 436-443. Online: 2014-05-23 © Trans Tech Publications.
[8] Jingang Wu, Qiang Li, Yu Yan., Emulation and prediction of the cold roll forming force, Advanced Materials Research, 472-475 (2012) 206-213.
[9] S.M. Panton, J.L. Duncan, S.D. Zhu, Longitudinal and shear strain development in cold roll forming, Journal of Materials Processing Technology, 60 (1996) 219-224.
[10] John Paralikas & Konstantinos Salonitis & George Chryssolouris., Energy efficiency of the cold roll forming process, Int J Adv. Manuf. Tech DOI 10.1007/s00170-012-4405-8.
[11] Machinery’s Handbook twenty-fifth edition, Industrial press inc, Newyork, 1246-1251, (1996).
[12] McGraw - Hill Macinning and metalworking handbook, Newyork,1200- 1204, (1994).
[13] George T. Halmos, Roll forming handbook, Delta Engineering, Inc. Toronto, Ontario, Canada, CRC Publications.
[14] Hong-Seok Park and Tran-Viet Anh, Optimization of bending sequence in roll forming using neural network And genetic algorithm, Engineering Materials, 48 (2012) 981-985.