Installation of Suitable Sensors for Object Detection and Height Control on Combine Harvester
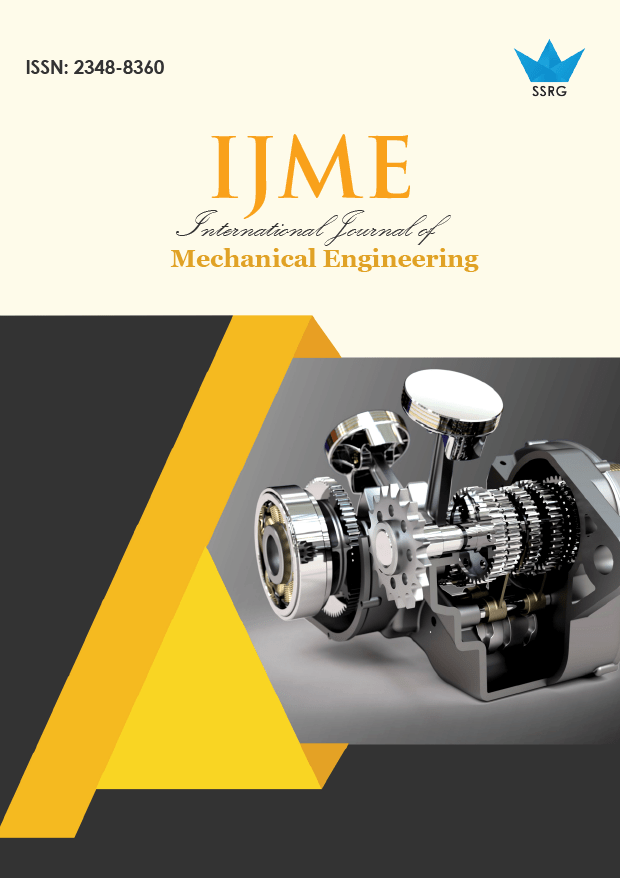
International Journal of Mechanical Engineering |
© 2021 by SSRG - IJME Journal |
Volume 8 Issue 5 |
Year of Publication : 2021 |
Authors : Esmaeil Mirmahdi, Omid Ghorbani Shirazi |
How to Cite?
Esmaeil Mirmahdi, Omid Ghorbani Shirazi, "Installation of Suitable Sensors for Object Detection and Height Control on Combine Harvester," SSRG International Journal of Mechanical Engineering, vol. 8, no. 5, pp. 12-19, 2021. Crossref, https://doi.org/10.14445/23488360/IJME-V8I5P103
Abstract:
Nowadays, agricultural industry has a lot of advancements and all its devices are mechanized. Combine harvester is one of the necessary devices in agricultural industry. A Combine harvester is a self-motor vehicle or machine that is used to reap grains. This machine has made its own progress, but due to some weakness, it still needs to be advanced. In this paper, we will be investigated New Holland Combine made in United States. First, it examines difficulties of Combine and it has made practical and operational suggestions which can be highly productive and satisfaction for the agricultural industry. In this paper, two sensors were used and it was proposed the best place for these sensors. The first sensor (Infrared sensor) is for detecting the object and the second sensor (Infrared sensor or Ocular sensor) is the height control (regulation) sensor, which is examined the benefits of these sensors for improvement of agricultural machinery by its practical and operational test on Combine. The findings indicated that the first sensor will actually reduce the risk of life to zero and the second sensor will be full satisfaction by working of Combine device. This practical and operational work can yield full productivity. In order to further examine the benefits of the plan and the idea, diagrams were plotted that they are indicated completely satisfactory and successful after the installation of sensor on Combine.
Keywords:
Combine harvester, Sensor of object detection, height control sensor, progress diagram
References:
[1] Zhang, Z. 2014. Development of a Robot Combine Harvester based on GNSS. PhD thesis. Graduation school of agriculture, Hokkaido University, Sapporo, Japan. DOI: info:doi/10.14943/doctoral.k11394.
[2] J. James and M. P. Maheshwar, “Plant growth monitoring system, with dynamic user-interface,” in 2016 IEEE Region 10 Humanitarian Technology Conference (R10-HTC), pp. 1–5, Agra, India, December 2016. DOI: 10.1109/R10-HTC.2016.7906781
[3] D. Pimentel, B. Berger, D. Filiberto et al., “Water resources: agricultural and environmental issues,” Bioscience, vol. 54, no. 10, pp. 909–918, 2004. https://doi.org/10.1641/0006-3568(2004)054[0909:WRAAEI]2.0.CO;2
[4] M. Taher Kahil, J. Albiac, A. Dinar et al., “Improving the performance of water policies: evidence from drought in Spain,” Water, vol. 8, no. 2, p. 34, 2016. https://doi.org/10.3390/w8020034
[5] Abidine, A.Z.; Heidman, B.C.; Upadhyaya, S.K.; Hills, D.J. Autoguidance system operated at high speed causes almost no tomato damage. Calif. Agric. 2004, 58, 44–47. https://escholarship.org/uc/item/6w077946
[6] Case IH. Case IH Autonomous Concept Vehicle, 2016. Available online: http://www.caseih.com/apac/en-in/news/pages/2016-case-ih-
premieres-concept-vehicle-at-farm-progress-show.aspx (accessed on 9 August 2017). https://doi.org/10.3390/s17112579
[7] ASI. Autonomous Solutions, 2016. Available online: https://www.asirobots.com/farming/ (accessed on 9 August 2017). https://doi.org/10.3390/s17112579
[8] Kubota, 2017. Available online: http://www.kubota-global.net/news/2017/20170125.html (accessed on 16 August 2017). https://doi.org/10.3389/frobt.2018.00028
[9] Ollis, M.; Stentz, A. Vision-based perception for an automated harvester. In Proceedings of the 1997 IEEE/RSJ International Conference on Intelligent Robot and Systems, Innovative Robotics for Real-World Applications (IROS ’97), Grenoble, France, 11 September 1997; Volume 3, pp. 1838–1844. DOI: 10.1109/IROS.1997.656612
[10] Stentz, A.; Dima, C.;Wellington, C.; Herman, H.; Stager, D. A system for semi-autonomous tractor operations. Auton. Robots 2002, 13, 87–104. https://doi.org/10.1023/A:1015634322857
[11] Wellington, C.; Courville, A.; Stentz, A.T. Interacting markov random fields for simultaneous terrain modeling and obstacle detection. In Proceedings of the Robotics: Science and Systems, Cambridge, MA, USA, 8–11 June 2005; Volume 17, pp. 251–260. DOI: 10.15607/RSS.2005.I.001
[12] Griepentrog, H.W.; Andersen, N.A.; Andersen, J.C.; Blanke, M.; Heinemann, O.; Madsen, T.E.; Nielsen, J.; Pedersen, S.M.; Ravn, O.; Wulfsohn, D. Safe and reliable: Further development of a field robot. Precis. Agric. 2009, 9, 857–866.
[13] Benet, B.; Rousseau, V.; Lenain, R. 2017. Fusion between a color camera and a TOF camera to improve traversability of agricultural vehicles. The 6th Conference International Workshop Applications of Computer Image Analysis and Spectroscopy in Agriculture, Aarhus, Danemark.
[14] Cho, W.; Kurita, H.; Iida, M.; Suguri, M.; Masuda, R. 2015. Autonomous positioning of the unloading auger of a combine harvester by a laser sensor and GNSS. Engineering in Agriculture, Environment and Food, http://dx.doi.org/10.1016/j.eaef.2015.01.004.
[15] Peyns, P.; Missotten, B.; Ramon, H.; De Baerdemaeker, J. 2002. A review of combine sensors for precision farming. Precision Agriculture, 3, pp. 169–182, © 2002 Kluwer Academic Publishers. Manufactured in The Netherlands. https://doi.org/10.1023/A:1013823603735
[16] Yap, Y. K. Design and development of rice combine harvester instrumentation system for crop yield and field performance mapping; M.Sc. Thesis, University Putra Malaysia, Selangor, Malaysia, 2007. (AFITA 2006: The fifth international conference of the Asian Federation for Information Technology in Agriculture, J. N. Tata Auditorium, Indian Institute of Science Campus, Bangalore, India, 9-11 November , 2006 2006 pp.301-311 ref.5)
[17] Chartuni, E.; Carvalho, F. de A. de; Marc¸al, D.; Ruz, E. Precision agriculture—New tools to improve technology management in agricultural enterprises. In Communica, 1st ed., 2nd stage; January–April, 2007, 24–31. DOI: 10.22004/ag.econ.188574
[18] Yap Y. Kin , Sudhanshu S. Jamuar & Azmi Yahya. 2011. Combine Harvester Instrumentation System for Use in Precision Agriculture. Instrumentation Science & Technology, 39:4, 374-393, DOI: 10.1080/10739149.2011.585195.
[19] Luettel, T., Himmelsbach, M., Wuensche, H.J. 2012. Autonomous ground vehicles concepts and a path to the future. In: Proceedings of the IEEE, vol. 100, (Special Centennial Issue), pp. 1831–1839. DOI: 10.1109/JPROC.2012.2189803
[20] Kragh, M. F.; Christiansen, P.; Laursen, M. S.; Larsen, M.; Steen, K. A.; Green, O.; Karstoft, H.; Nyholm, R. 2017. FieldSAFE: Dataset for Obstacle Detection in Agriculture. Sensors, 17, 2579; DOI:10.3390/s17112579.
[21] Zhao, T.; Noboru, N.; Yang, L.; Kazunobu, I.; Chen, J. 2016. Development of uncut crop edge detection system based on laser rangefinder for combine harvesters. Int J Agric & Biol Eng, 9(2) 21-28. DOI: 10.3965/j.ijabe.20160902.1959.