Development of Servo Controlled Automation For Tmc (Tandem Master Cylinder) Performance Test Rig
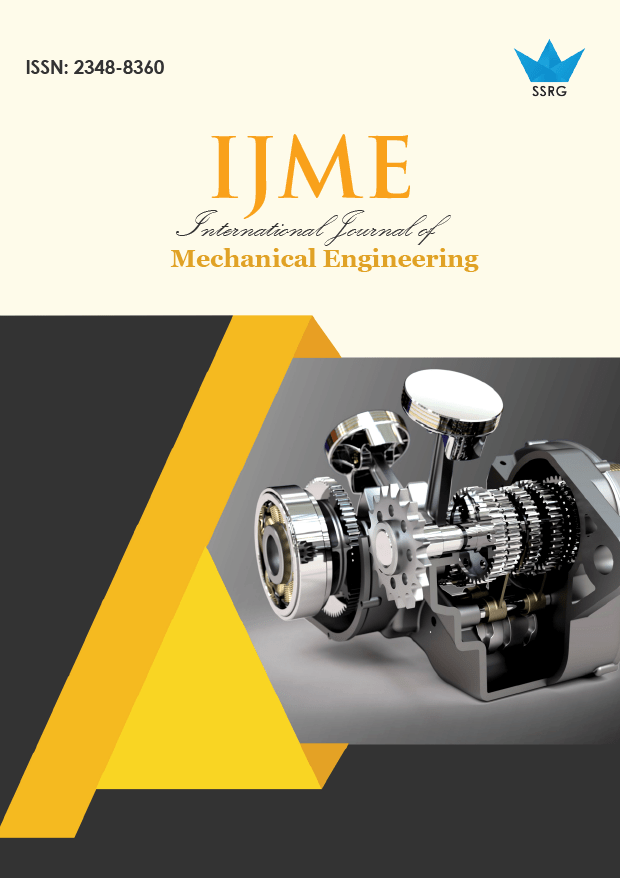
International Journal of Mechanical Engineering |
© 2021 by SSRG - IJME Journal |
Volume 8 Issue 5 |
Year of Publication : 2021 |
Authors : H.Venkatesh, Dr. K. Annamalai, S.Thiyagarajan |
How to Cite?
H.Venkatesh, Dr. K. Annamalai, S.Thiyagarajan, "Development of Servo Controlled Automation For Tmc (Tandem Master Cylinder) Performance Test Rig," SSRG International Journal of Mechanical Engineering, vol. 8, no. 5, pp. 41-46, 2021. Crossref, https://doi.org/10.14445/23488360/IJME-V8I5P106
Abstract:
The functional parameters of Tandem Master Cylinder of a braking system are evaluated through Tandem Master Cylinder Performance Test Rig.Tandem Master Cylinder ensures required pressure buildup in the hydraulic line of braking system.In existing Tandem Master Cylinder Performance Test Rig, two areas have been identified for improvement.First one is manual measurements of TMC Crack-off hole test and Piston Return Time Test.Second one is inability to achieve accurate travel ramp rate.Manual measurement of TMC Crack-off hole test is overcome by incorporating pressure and travel sensor for data measurement and also developing a new pneumatic circuit.Manual measurement of TMC Piston Return Time Test is overcome by designing and fabricating a new test fixture assembly.To achieve accurate travel ramp rate, a servo motor with inbuilt servo drive programming unit is incorporated.To interface the servo drive program with LabVIEW application for achieving the travel ramp rate and test data capturing in LabVIEW.Comparison of existing test method data and experimental new test sequence graphical data can be generate based on the results, identify the test quality improvement and accuracy.
Keywords:
Tandem Master Cylinder, LabVIEW, Kollmorgen Automation Suite, Performance Test rig, Virtual Instrumentation.
References:
[1] Von Thun HJ. -test bench for testing the drive train of a vehicle. Patent 4939985, USA, 1990.
[2] Yuan Y, Zhang JZ,Li YT, et al. – A novel regenerative electrohydraulic brake system: development and hardware-in-loop tests. IEEE T Vehn Techno 2018;67:11440-11452.
[3] Hon Ping Ho – The influence of braking system component design parameters on pedal force and displacement characteristics (University of Bradford) 2009.
[4] ling Jun li – Simulation and control of servo hydraulic actuators for test applications-2015.
[5] Zeng-cheng Liao, Yang li, Xian-Xu bai Design, modeling and verification of a test bench for braking simulation of ¼ vehicle-2019.
[6] Bogdan Mihai Measurement Experiment, using NI USB-6008 data acquisition-2009.
[7] Subhransu Padhee Umesh C. Pati Design of an educational laboratory for measurement and data acquisition system-2016.
[8] Aldo Sorniotti, Gianfrancesco Maria Repici Politecnico di Torino Hardware in the loop with electro-hydraulic brake system.
[9] Wolf D.Jonner, H. Winner, L. Dreilich, E. Schunck, Electrohydraulic brake system – The first approach to brake-BY-Wire Technology, SAE Technical paperseries 960991, 1996;
[10] Richard Philippe, chelles (FR), Franoois Gaffe,Bondy (FR), Bastien, Cagnac, Cramoisy (FR) electrically boosted braking system Aug 2015.