Influence of Magnetic Abrasive Finishing Process Parameters on Surface Roughness of SAE 52100 Steel Using a Hemisphere Pole Geometry Electromagnet
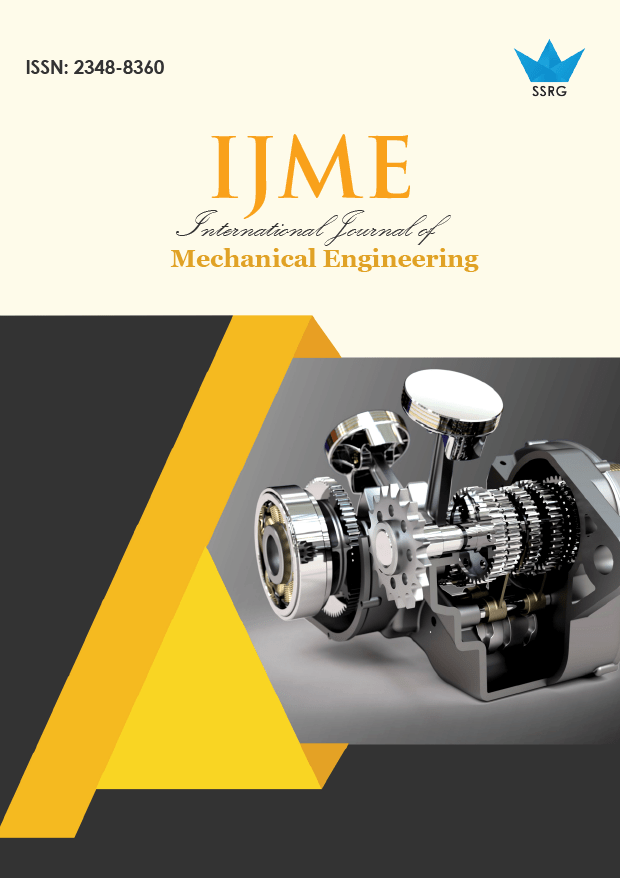
International Journal of Mechanical Engineering |
© 2025 by SSRG - IJME Journal |
Volume 12 Issue 4 |
Year of Publication : 2025 |
Authors : Rajendra E. Kalhapure, Mayank Shekhar, Ravindra R. Navthar, Prashant N. Nagare |
How to Cite?
Rajendra E. Kalhapure, Mayank Shekhar, Ravindra R. Navthar, Prashant N. Nagare, "Influence of Magnetic Abrasive Finishing Process Parameters on Surface Roughness of SAE 52100 Steel Using a Hemisphere Pole Geometry Electromagnet," SSRG International Journal of Mechanical Engineering, vol. 12, no. 4, pp. 11-19, 2025. Crossref, https://doi.org/10.14445/23488360/IJME-V12I4P102
Abstract:
Finishing is the last stage of the manufacturing of jobs that demand the utmost quality with regard to shape, precision, and surface integrity. Fine-finishing is a process that improves the surface of the workpiece, enhancing its functional and quality attributes. The automotive sector requires precise finishing to enhance the performance, appearance, and longevity of its components. 52100 bearing steel is widely utilized in the production of critical components for various bearings and other applications. However, conventional finishing methods can be difficult to apply when creating components of diverse shapes and sizes. To address this, advanced fine machining and finishing techniques are being employed. One such method is magnetic abrasive finishing (MAbF), a precision technique that produces outstanding quality components. This process utilizes a flexible magnetic abrasive brush (FMAB) guided by a magnetic field to achieve the desired finish. Typically, the magnetic abrasives used in MAbF consist of two key components: ferromagnetic materials and abrasives, which work in tandem. In this study, 52100 steel bars undergo fine polishing using an MAbF technique, with various process parameters being examined. Aluminum oxide (Al2O3) serves as the abrasive, while a hemisphere-shaped DC electromagnet is employed for the finishing process. Key variables can be adjusted to achieve optimal surface finishes, including magnetic flux density, component rotation speed, and the ratio of abrasive to ferrous powder in the mixer. The effectiveness of the process is influenced by factors such as the abrasive particle content in the mixing ratio, the speed of the workpiece, and the input DC power source that determines the magnetic flux density. The results indicate that increasing the rotation speed and DC voltage enhances the surface roughness of the 52100 bearing steel rods. Specifically, experiments reveal that improvements in rotation speed and DC voltage can lead to a 57% increase in the maximum enhancement of surface roughness.
Keywords:
Magnetic abrasives finishing, Hemisphere electromagnet, Flexible magnetic abrasives-brush, Magnetic abrasives particles.
References:
[1] Rajendra E. Kalhapure, Gaurav Kumar Gugliani, Ravindra R. Navthar, Prashant N. Nagare, "Experimental Analysis for the Surface Roughness Improvement of Bearing Steel SAE 52100 Using Magnetic Abrasive Finishing Process," SSRG International Journal of Mechanical Engineering, vol. 12, no. 1, pp. 43-48, 2025.
[2] Ik-Tae Im, Sang Don Mun, and Seong Mo Oh, “Micro Machining of an STS 304 Bar by Magnetic Abrasive Finishing,” Journal of Mechanical Science and Technology, vol. 23, pp. 1982-1988, 2009.
[CrossRef] [Google Scholar] [Publisher Link]
[3] Yuri Mikhailovich Baron, S.L. Ko, and Jung Il Park, “Characterization of the Magnetic Abrasive Finishing Method and Its Application to Deburring,” Key Engineering Materials, vol. 291-292, pp. 291-296, 2005.
[CrossRef] [Google Scholar] [Publisher Link]
[4] T.C. Kanish et al., “Experimental Investigations on Magnetic Field Assisted Abrasive Finishing of SS 316L,” Procedia Manufacturing, vol. 30, pp. 276-283, 2019.
[CrossRef] [Google Scholar] [Publisher Link]
[5] R.S. Mulik, and P.M. Pandey, “Experimental Investigations into the Finishing Force and Torque in Magnetic Abrasive Finishing Process,” ASME International Mechanical Engineering Congress and Exposition, San Diego, California, USA, vol. 56192, pp. 1-7, 2013.
[CrossRef] [Google Scholar] [Publisher Link]
[6] A. Sinha, S. Singh, and Lakhvir Singh, “Comprehensive Review of Current Research Trends in Magnetic Abrasive Finishing (MAF) Process,” Advanced Materials Manufacturing & Characterization, vol. 8, no. 1, pp. 49-57, 2018.
[Google Scholar]
[7] Yuewu Gao et al., “Modeling of Material Removal in Magnetic Abrasive Finishing Process with Spherical Magnetic Abrasive Powder,” International Journal of Mechanical Sciences, vol. 177, 2020.
[CrossRef] [Google Scholar] [Publisher Link]
[8] Lida Heng et al., “Application of Al2O3/Iron-Based Composite Abrasives on MAF Process for Inner Surface Finishing of Oval-Shaped Tube: Predicting Results of MAF Process Using Artificial Neural Network Model,” Journal of Materials Research and Technology, vol. 15, pp. 3268-3282, 2021.
[CrossRef] [Google Scholar] [Publisher Link]
[9] Palwinder Singh et al., “Experimental Examination on Finishing Characteristics of Aluminum Pipes in Magnetic Abrasive Machining Using SiC Contained Glued Magnetic Abrasives,” Trends in Sciences, vol. 19, no. 19, pp. 1-17, 2022.
[CrossRef] [Google Scholar] [Publisher Link]
[10] Mahmmoud Abdallha, Salah Al-Zubaidi, and Ali H. Kadhum, “Effect of Magnetic Abrasive Finishing Process on the Surface Roughness of CuZn28 with New Pole Geometry,” Journal of Mechanical Engineering Research and Developments, vol. 43, no. 4, pp. 256-264, 2020.
[Google Scholar]
[11] Mehrdad Vahdati, and SeyedAlireza Rasouli “Evaluation of Parameters Affecting Magnetic Abrasive Finishing on Concave Freeform Surface of Al Alloy via RSM Method,” Advances in Materials Science and Engineering, vol. 2016, no. 1, pp. 1-14, 2016.
[CrossRef] [Google Scholar] [Publisher Link]